Equipment longevity and productivity are among the most effective ways to improve operating margins and costs. Preventive maintenance (PM) is the most reliable and accessible way to achieve these goals. What is preventive maintenance? It is a series of regularly scheduled, recurring steps that help ensure equipment remains at least at a baseline level of good repair, so that standard operating requirements are adhered to and that equipment is generally operating as intended.
With this understanding of the answer to “What is the definition of preventive maintenance?” we can now explore the practice of preventive maintenance in greater depth, while also examining preventive maintenance benefits. These include increased productivity, more effective equipment operation, lower overall maintenance costs and more.
Types of preventive maintenance
Broadly speaking, preventive maintenance refers to regularly scheduled checkups and tasks that keep equipment in good working order. To understand what this approach entails and how it is executed, it’s important to know the various preventive maintenance types.
The below strategies and approaches can all play a role in a comprehensive preventive maintenance plan:
- Calendar-based maintenance: A calendar-based maintenance approach calls for regularly scheduled maintenance checks and tasks based on an interval of time, such as daily, weekly or monthly. These types of tasks can generally be carried out visually or through a quick test, and may include oil checks and replacement, light cleaning, belt inspection, moving component inspection, and many more.
- Use-based maintenance: Use-based maintenance is similar to calendar-based maintenance, except that it occurs based on equipment usage metrics, such as a certain number of cycles or operational hours. These tasks would generally be similar to those for calendar-based maintenance: checking consumables and moving parts for wear and potential replacement.
- Failure-finding maintenance: Failure-finding maintenance involves regular checks of systems such as alarms, backups and fail safes: systems and parts that cannot be visually inspected, but which are nevertheless critical to continued operations. These types of tasks may include backup generator checks, electric system checks, alarm checks and more. Frequently, these tasks will involve a test or diagnostic process to confirm that the system is online and operating as intended.
- Risk-based maintenance: Risk-based maintenance is based upon an assessment of component criticality: components and equipment that would have the largest impact on production if they were to fail are checked and maintained more frequently. The maintenance checklist for these high-priority components may also be more in depth than for lower-criticality components.
When to utilize preventive maintenance
Although preventive maintenance can be extremely helpful for keeping your operations running as smoothly as possible, it may not be necessary in all cases. In general, it’s always a good idea to refer to the manufacturer’s guidelines when establishing any maintenance schedule. This will depend a great deal on the type of equipment you use and what you need it to do.
As a rule of thumb, however, assets that benefit the most from this approach are those that are critical to efficient operation as well as those that are required from a health and safety standpoint. If the machinery you use has failure modes that can be prevented with regular inspections and tune-ups, this is another strong candidate for preventive maintenance. On the other hand, equipment that does not serve critical functions or is prone to failures that are not related to maintenance would not benefit from this approach. Other assets that should not be targeted for preventive maintenance include those that would require repairs more expensive than the cost of simply replacing them. Once you evaluate which categories your machines fit into, you’ll have a much better idea of how you can deploy a preventive maintenance schedule to its best effect.
The benefits of preventive maintenance
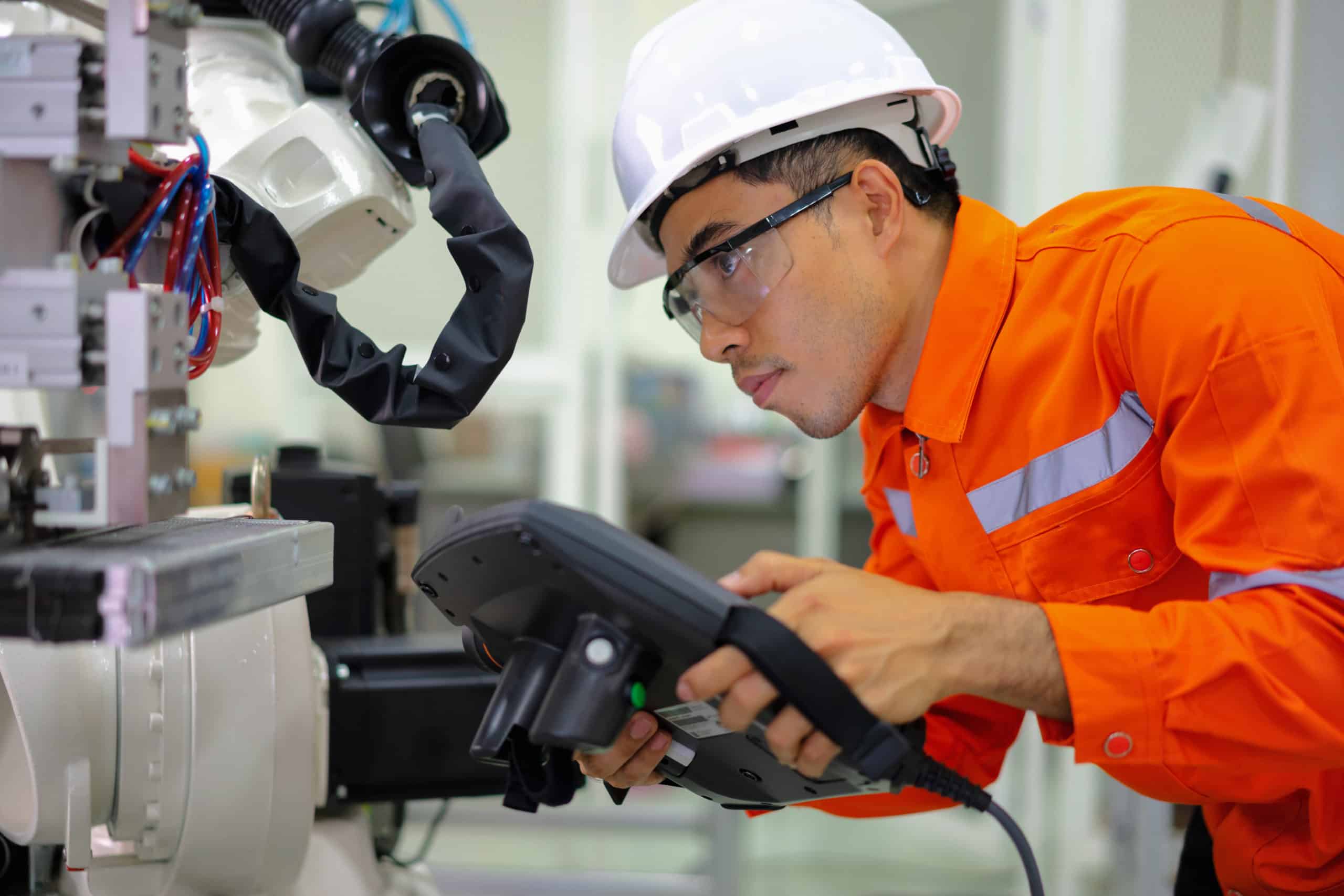
Even with an in-depth understanding of PM, you may still ask, “What is the purpose of preventive maintenance?” While we know that the immediate purpose is to keep equipment in good working order, in this section, we will examine the core “whys” of engaging in preventive maintenance: to achieve operational and organizational benefits.
The advantages of preventive maintenance include:
- Lower overall maintenance costs: Preventive maintenance yields one of the best returns on investment across industry. Dedicating the time and resources to execute standard maintenance checks and tasks on a regular basis can make a major impact on reduction of unplanned maintenance events down the line, since equipment is kept in optimal working order for longer, and potential issues may be identified in the course of preventive maintenance tasks. The small amount of downtime and resource usage for preventive maintenance is a small price to pay to reduce or prevent more costly and extensive equipment shutdowns and major repairs.
- Higher productivity: When equipment is kept in top working condition, it operates more consistently and predictably, and is better able to produce the intended output. Equipment that is allowed to languish without regular inspection and replacement of components — such as belts, pumps and gear — is more likely to operate out of spec, producing defective parts that require rework or rejection.
- Prevention of damage to equipment: Nearly every preventive maintenance checklist will include light cleaning and inspection and removal of debris from the equipment and the surrounding area. These relatively simple tasks can play a major role in preventing damage to equipment and subsequent malfunctions, as debris buildup in machinery can lead to extensive damage, well beyond normal wear and tear.
- A simple way to take a proactive approach: Proactive maintenance is always better than reactive maintenance: it costs less, takes less time, and allows for better planning in order to keep you on budget and on schedule. Preventive maintenance is one of the easiest steps you can take to implementing a proactive approach — even with a baseline PM plan that consists of visual inspection, light cleaning and standard component replacement.
All too often, facilities allow preventive maintenance to fall by the wayside due to the perception that there is not enough time or that the resources are not available. In reality, the consequences of ignoring PM may be exponentially negative compared to the resources and cost that routine maintenance would have involved.
Preventive maintenance examples
There are numerous tasks that can be considered preventive maintenance depending on the type of equipment and its needs. This means practically any type of task may fall into this category, depending on the circumstances and requirements. However, there are a few examples of preventive maintenance applications that are more common than others. These include regular cleaning of components to remove dust, grease and other potential contaminants before they have a chance to impact the machinery’s performance.
Other examples include replacing any components or parts that appear to be suffering from premature wear. This is critical for ensuring the equipment in question continues to operate as smoothly and efficiently as it can. Frequent lubrication is another core element of preventive maintenance, as it helps extend the lifespan of parts and prevents them from becoming worn out or failing at an inopportune moment.
In some cases, completely overhauling a system can be considered preventive maintenance. This is especially true for systems that see high-intensity use because the stresses they experience can add up quickly in a short period of time. These are just a few examples of maintenance work that can be considered preventive. Your facility’s schedule will depend on your specific use cases and setup. Having a partner with expertise in this area will ensure you have everything in place.
Who benefits from preventive maintenance?
Any facility or industry with production machinery can benefit from preventive maintenance. As discussed above, the modest upfront resource investment in preventive maintenance tasks can yield benefits and a continual return on investment.
Some specific industries that can particularly benefit from preventive maintenance include:
- Aerospace
- Automotive
- Building Products
- Consumer Packaged Goods
- Heavy Equipment
- Metal Products
- Paper & Pulp
- Pharmaceutical & Medical Devices
- Power Distribution
- Tire and Rubber
Helping manufacturers around the world
ATS is a global leader in industrial maintenance with decades of reliability expertise across a range of industries. We provide the solutions and services that resolve our clients’ preventive maintenance needs with best-in-class safety excellence, consistent service quality and a focus on developing a tailored plan with measurable KPIs to meet or exceed your objectives.
Our preventive maintenance services can include an assessment of the current state of your equipment, development of a routine preventive maintenance strategy, task checklists and plan implementation. Partnering with a maintenance service provider can help give you peace of mind that you have a technically skilled workforce and are able to reap the full benefits of an effective, maintenance strategy.
Our preventive maintenance services are flexible to fit your needs – whether you are looking for short term support with only a couple technicians, longer-term with a full technical workforce or as turn key, comprehensive maintenance solution. To learn how we can help you increase equipment longevity, optimize output and improve operating margins, contact us today.