Proactive approach
Our predictive maintenance services provide insight and analytics to help prevent downtime
Condition-based
We baseline current operating conditions, then use data and analytics to reveal important trends
Data-driven
Utilizing predictive maintenance tools allows for decisions based on data not instinct
Optimize technician and production efficiency
Many manufacturers are replacing preventive maintenance with predictive maintenance tools and technologies. Traditional time or usage-based maintenance helps protect against breakdowns, but leaves the risk of doing too much, too little or the wrong type of work. Predictive maintenance solutions provide a proactive data-driven approach that increases ROI, improves output, eliminates unplanned downtime and reduces equipment failures.
After baselining current operating conditions, ATS relies on data acquisition and predictive maintenance analytics to reveal important trends. Leveraging advanced machine learning algorithms and predictive maintenance software, our experts analyze sensor-collected data to identify problem areas and prioritize the necessary actions. Knowing what’s likely to happen inside production machinery allows your maintenance team to make better decisions. By revealing the true causes of failure, the data provided by predictive maintenance equipment can shape purchasing decisions, depreciation rates and planned replacement dates.
Machine health monitoring
to prevent unplanned downtime
As a technology-driven predictive maintenance company, we combine cutting-edge technologies including advanced sensors with industry-leading data analytics and reliability expertise to help you detect real-time issues before they cause an unexpected failure.
-
Data
Cloud-based condition monitoring products provide centralized data acquisition and analytics
-
Insights
Combines the efficiencies of cognitive and expert analysis with actionable insights across monitoring points
-
Results
Unparalleled support to prevent unplanned downtime and reduce labor and maintenance costs. Drive uptime with machine health monitoring, ROI guaranteed.
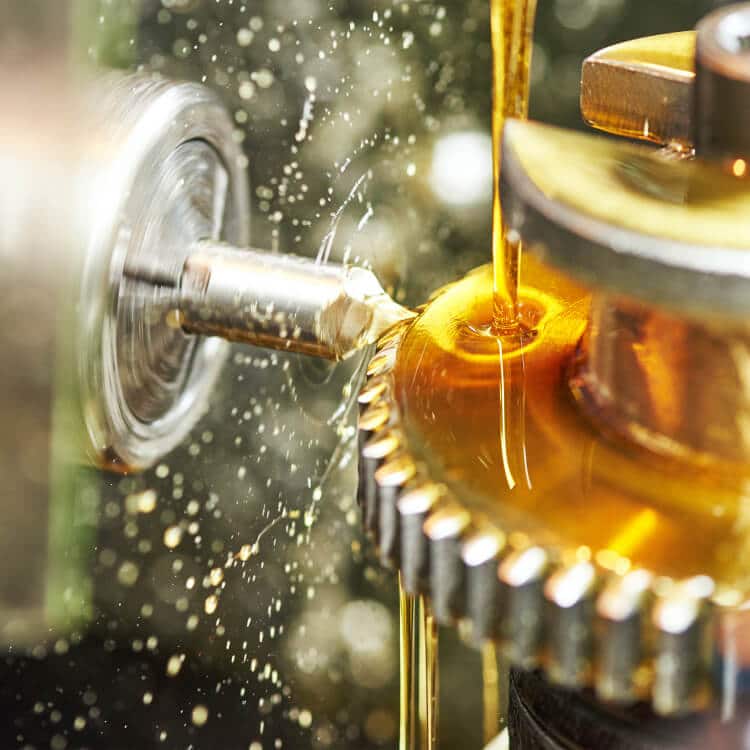
Keep fluids running with oil analysis
Undertaking oil changes based on time or usage can increase downtime and costs. Routine lubrication analysis lets manufacturers predict when fluid needs to be replaced while providing information about the machine’s overall health with this predictive maintenance solution.
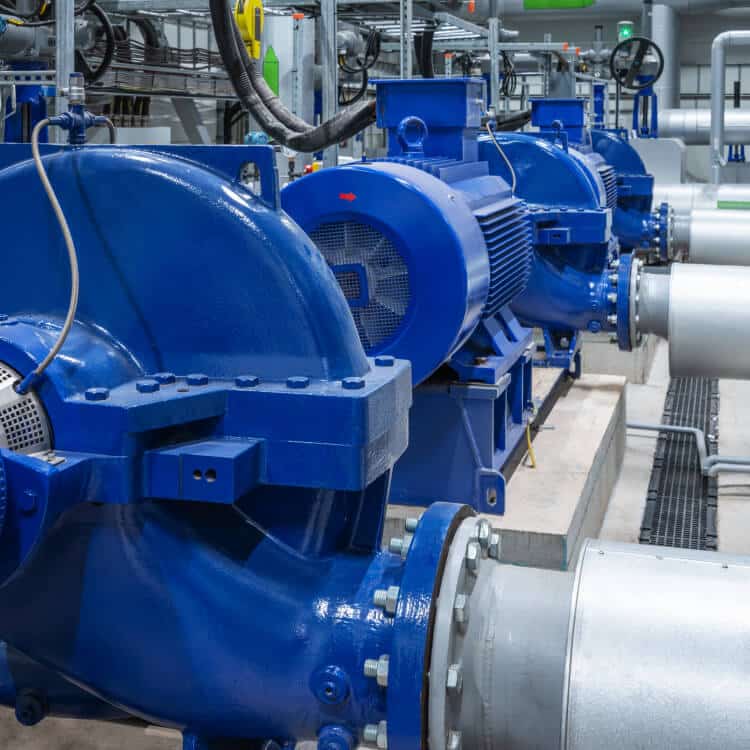
Keep rotating machinery in optimal condition
Vibration monitoring and machine vibration analysis prevent the deferred maintenance that can negatively impact product quality. A structured vibration analysis program helps manufacturers avoid quality and breakdown issues.
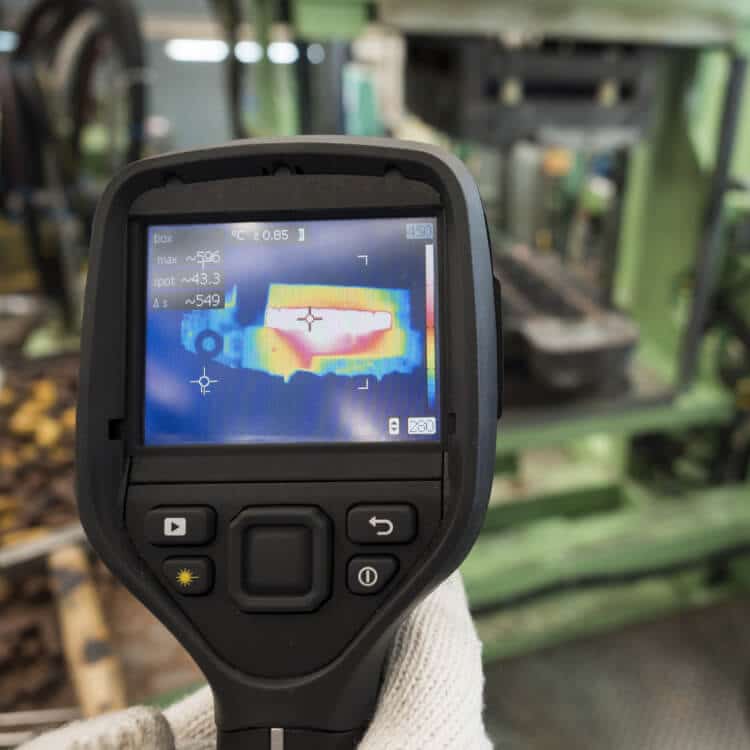
Detect issues early with thermographic imaging
Thermographic testing, or infrared inspection, is an industrial predictive maintenance method that helps extend equipment life. Infrared inspection identifies issues in real time, allowing manufacturers to assume a proactive position and reduce unplanned downtime, optimize repair schedules and lower maintenance costs.
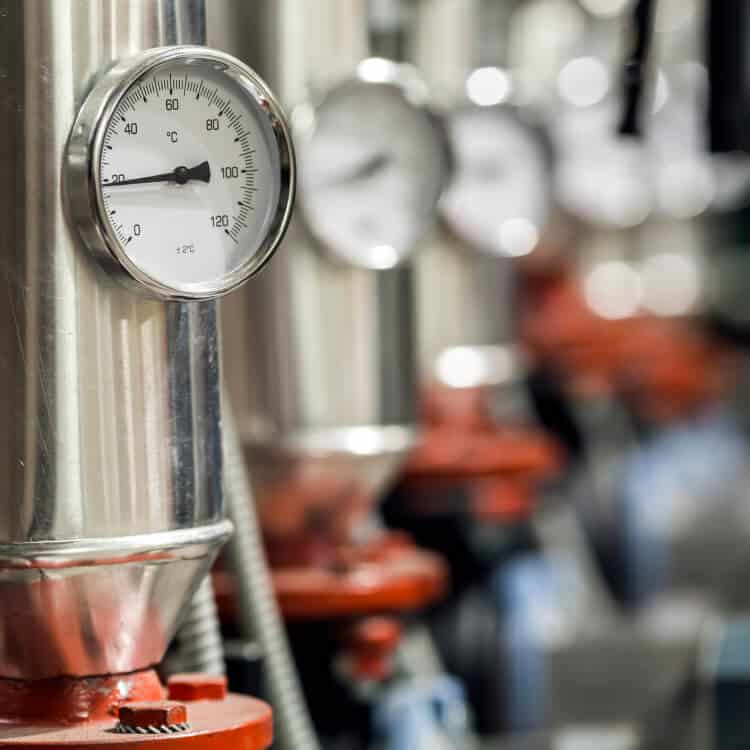
Reduce waste while improving reliability and safety
Adding ultrasonic leak detection service to your predictive maintenance strategy provides valuable insights into your equipment operation. It allows you to optimize maintenance management, extend mean-time-between-failures (MTBF), increase safety and reduce lost production time.
Be proactive against unplanned downtime
Explore predictive maintenance resources
Learn about predictive maintenance best practices and insights.
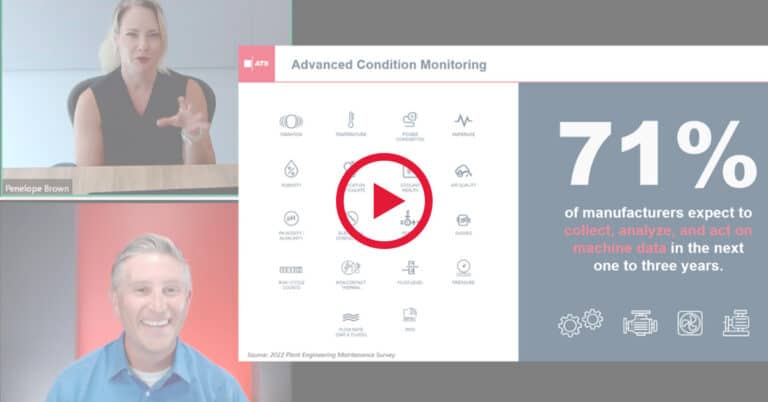
Webinar
Predictive maintenance programs for manufacturers
Our predictive maintenance services, technologies and best-in-class processes deliver measurable results across process and discrete manufacturing, optimizing business functions across organizations.