Improve productivity with heavy machinery maintenance
Many heavy equipment manufacturers like yourself are challenged with having both new, state-of-the-art and decades-old machines in your production facilities while improving asset performance. As the workforce retires and parts become obsolete, it becomes harder to keep assets performing. Our skilled technical talent, decades of experience and proven heavy equipment predictive and preventive maintenance solutions help reduce downtime, cut costs and increase ROI.
Our expertise in many aspects of heavy equipment maintenance allows us to help your factory overcome operational challenges while increasing uptime and optimizing productivity. Our knowledge of your equipment includes, but are not limited to:
CNC Machines
Laser Cutting
Shot Blasting
Parts Washers
Torches
Grinding
Sand Blasting
Testing Equipment
Reliability excellence and beyond
Our skilled workforce, established processes and innovative, data-driven technologies combine to help you meet your unique business needs. Whether you lack skilled workers with advanced training or are not currently operating at peak productivity, you can count on our heavy equipment management and industrial maintenance solutions to help your reliability soar.
- Recruitment and retention
- Skilled, technical workforce
- IIoT technologies
- World-class safety
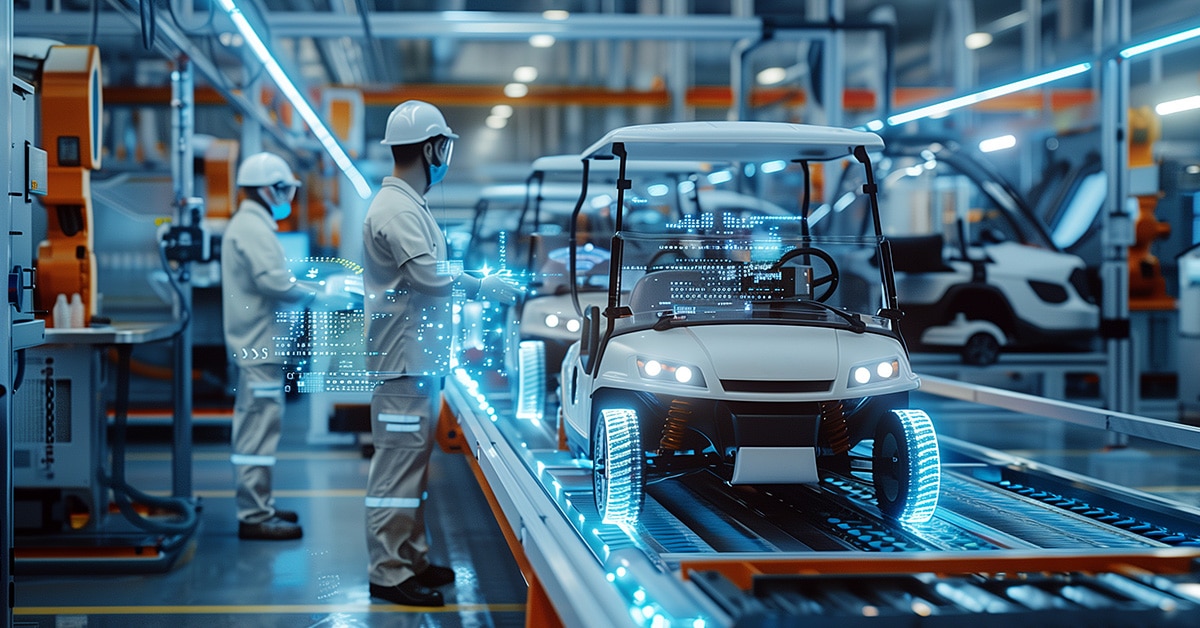
$7M+ saved with predictive maintenance
Confronted with critical oven and pump vibration levels, a golf cart manufacturer needed more than just monitoring, they needed a strategic partner. They turned to ATS not only for advanced sensor technology but for a collaborative, on-site approach tailored to their unique operational goals. By aligning ATS’s solutions with their goals and challenges, the manufacturer achieved:
- $7M+ in oven savings
- $60K+ in pump savings
- 240+ hours in avoided downtime
“I’ve never experienced a maintenance team like this. It feels like ATS is as invested in our success as a company as we are.”– Leading Heavy Equipment Manufacturer
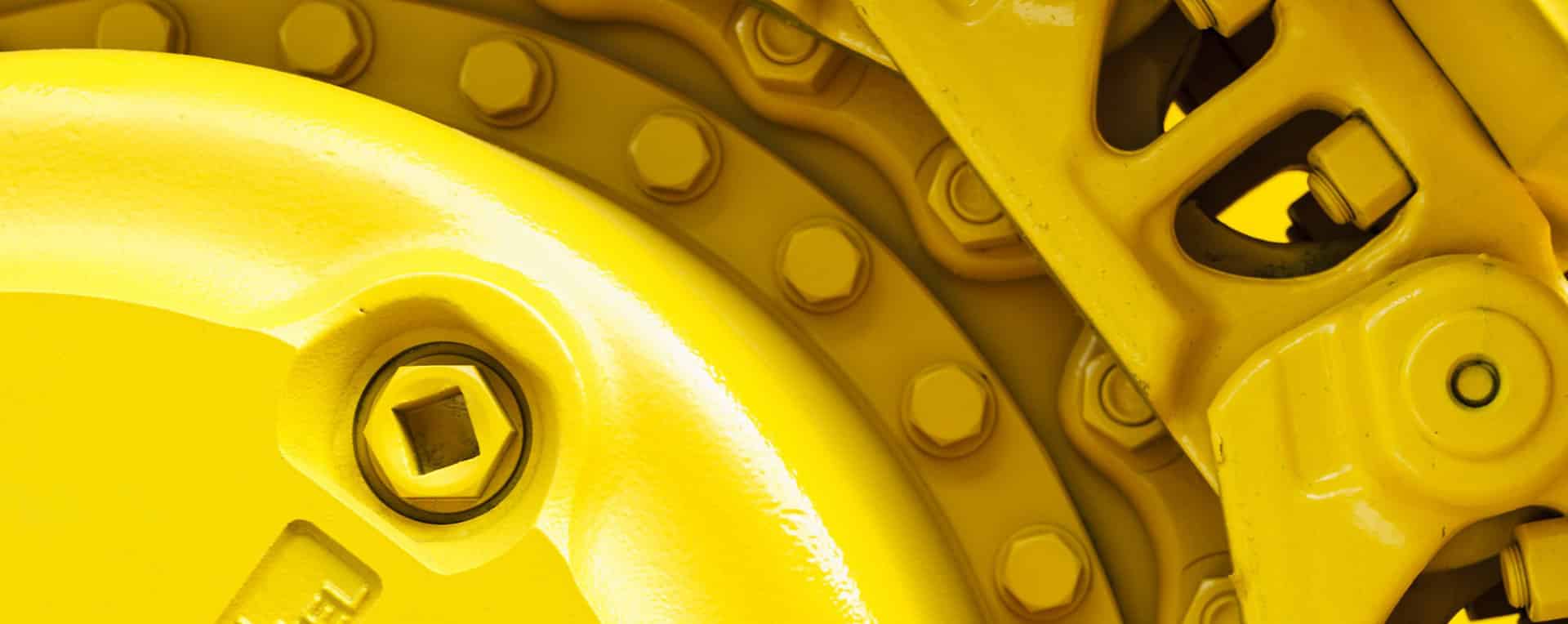
Heavy equipment maintenance solutions
To help manufacturers achieve reliable production and meet their goals, we offer heavy equipment services that range from comprehensive maintenance to the provision of skilled technicians to supplement and support your maintenance and reliability goals. We stand apart from other heavy equipment maintenance companies, thanks in part to our advanced technologies such as sensors to anticipate equipment failures. We also leverage software and advanced data analytics for better monitoring, control and optimization of maintenance processes and equipment.
Lead with a safety mindset
A safe workplace starts with a commitment to safety culture. ATS technicians bring best-in-class safety procedures to your site, helping you prioritize employee well-being while reducing recordable incidents.
-
World-class safety
Our Beyond Zero safety culture prioritizes compliance and employee well-being
-
Low incident rates
ATS has a 50% lower recordable incident rate than industry average
-
Exceed OSHA standards
ATS has an industry-leading OSHA incident rate and regulatory compliance

Meet your asset reliability challenges
Cost pressures drive heavy equipment manufacturers to extend the useful life of their large, specialized machines. We provide machine health monitoring, predictive and preventive maintenance, and even production operators to keep your machines running optimally for as long as possible.
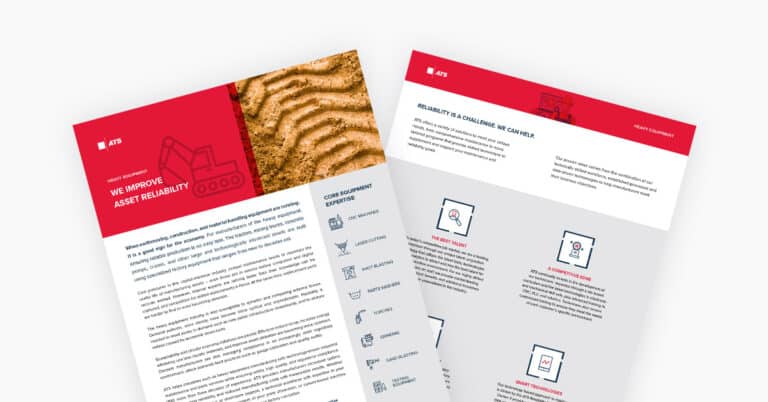
Info Sheet