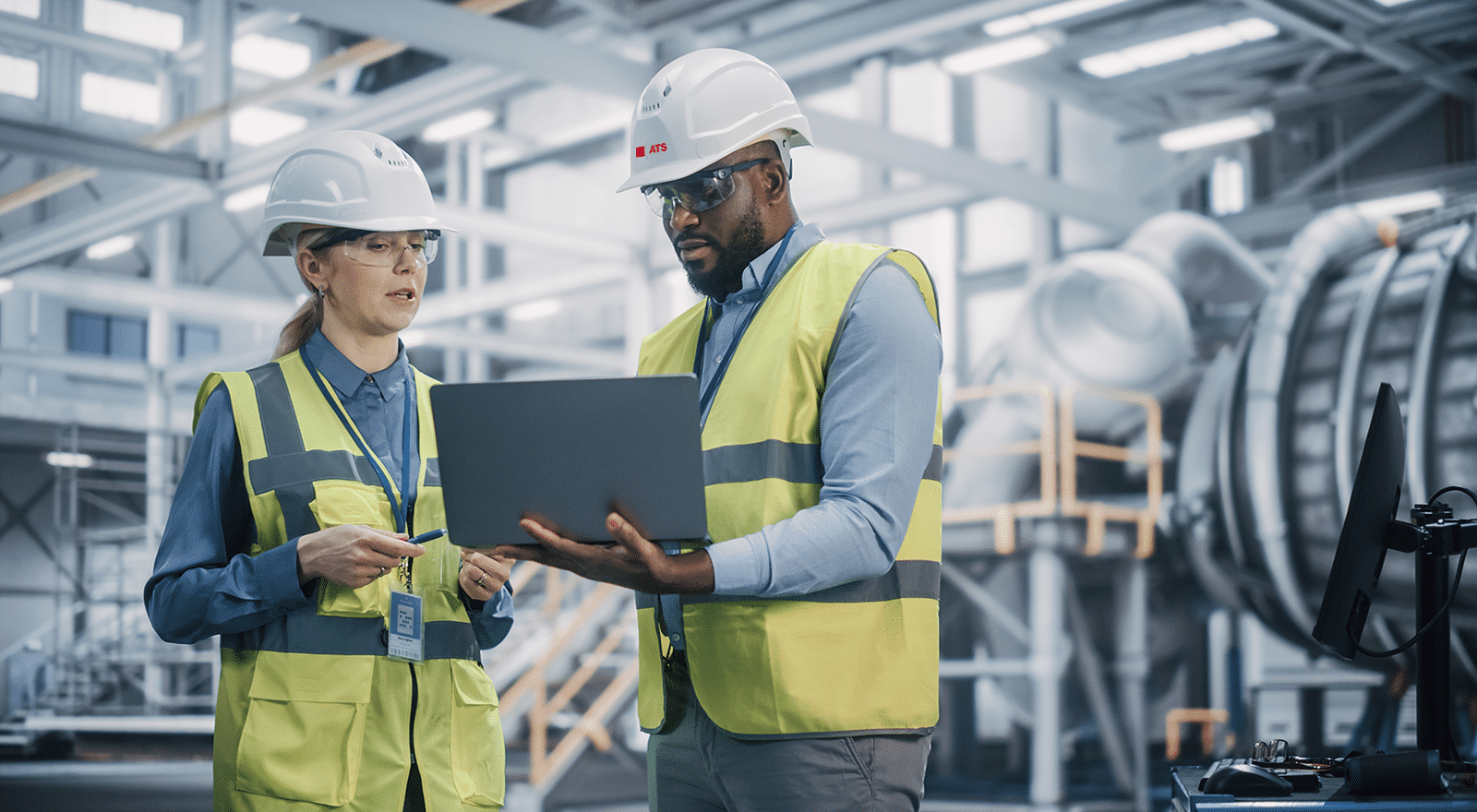
Should I monitor all my assets?
No, you shouldn’t monitor every asset on the factory floor. This can cause an influx of unnecessary data and divert focus from critical assets. Instead, place sensors on key equipment, as recommended by ATS technicians and solution engineers during the comprehensive facility walkthrough.
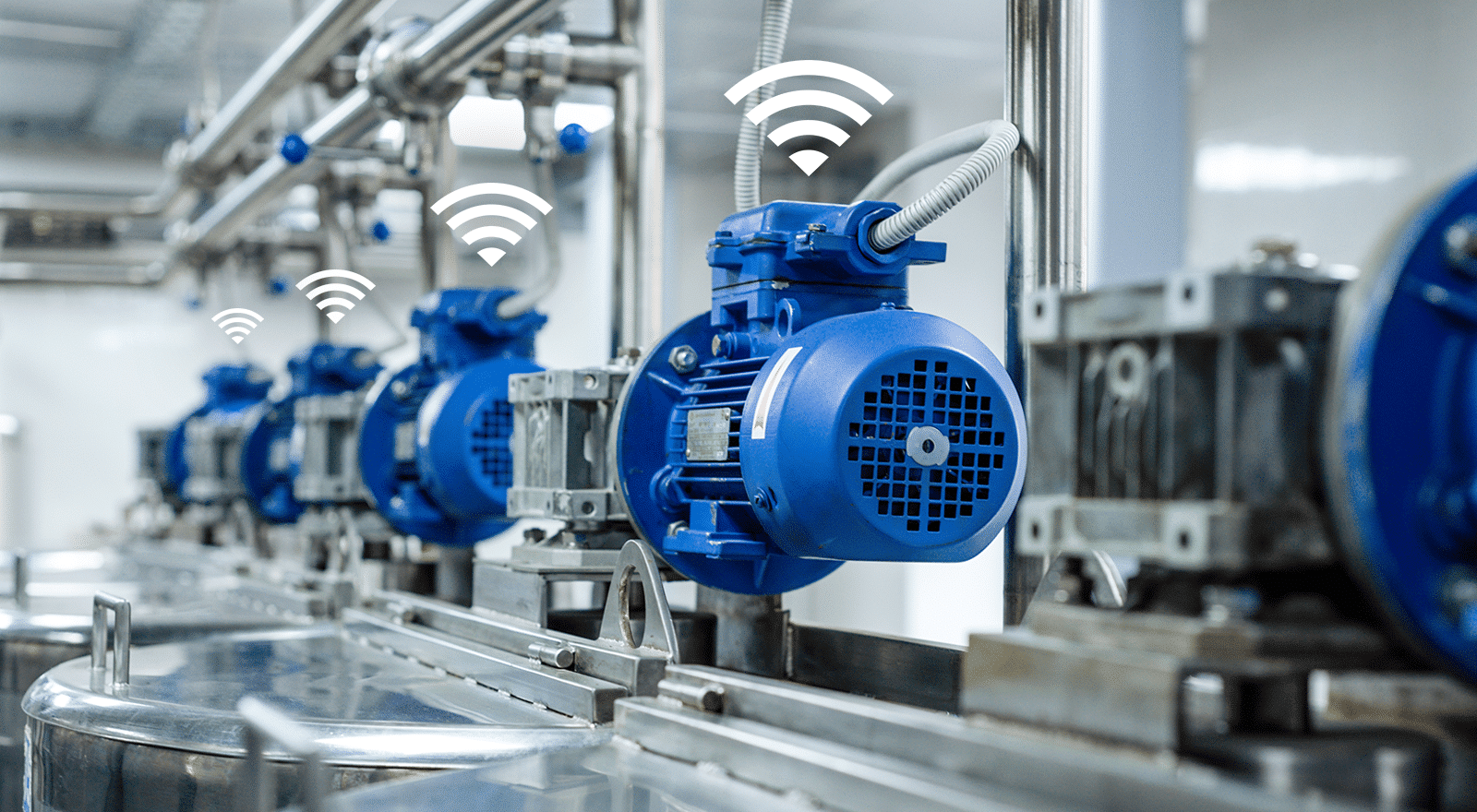
What do the sensors monitor?
Our sensors can monitor several key performance indicators. Our team helps you determine the type of sensor needed, the ideal sensor placement and the number of sensors to best detect fluctuations in machine health.
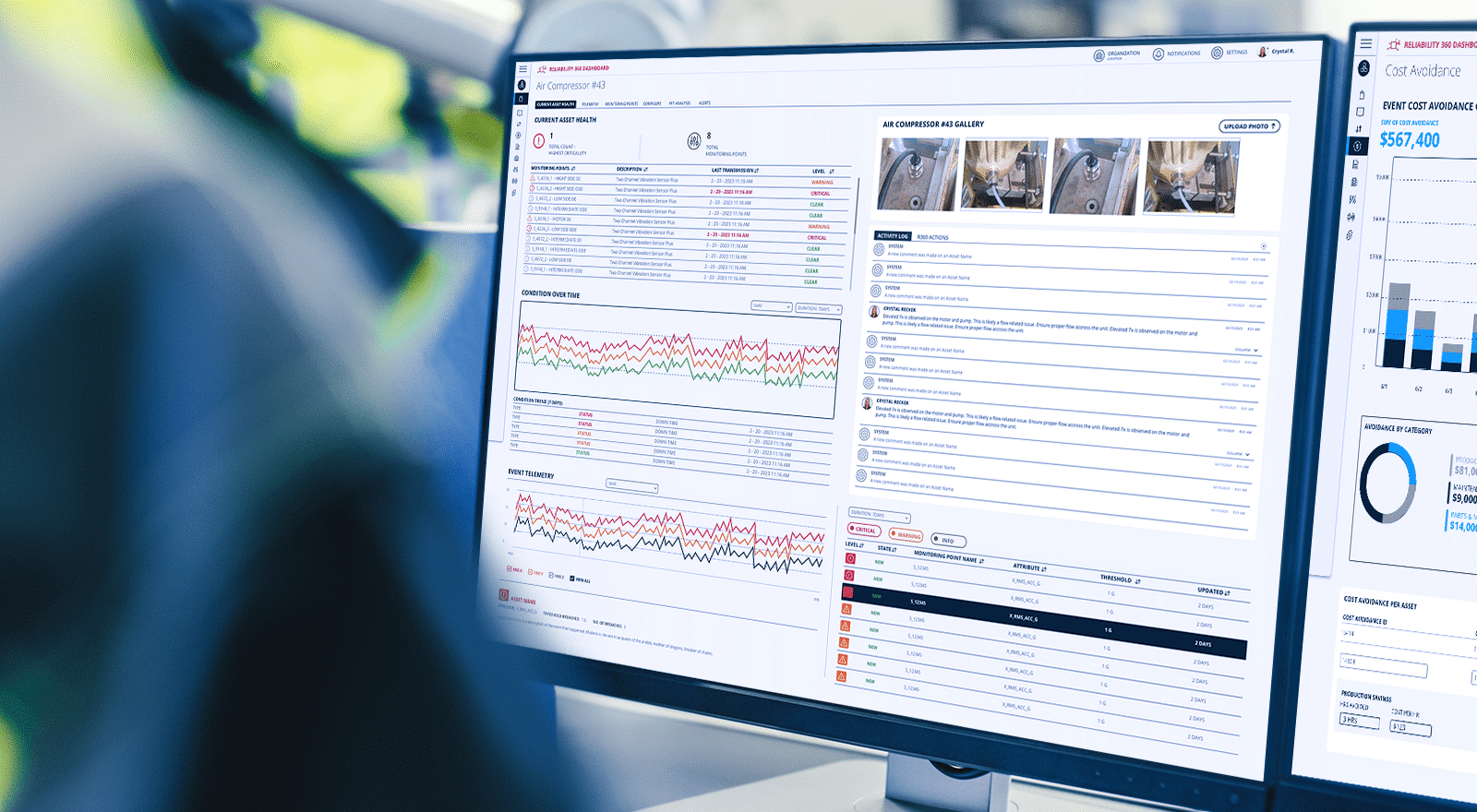
How will my plant be alerted of fluctuations in asset health?
Alerts can be customized to who, how and when you receive them. Delivery methods include email, text, dashboard notifications or a direct call from our team. When an alert is triggered, our team digs into the data at the monitoring point and asset level to pinpoint root cause.
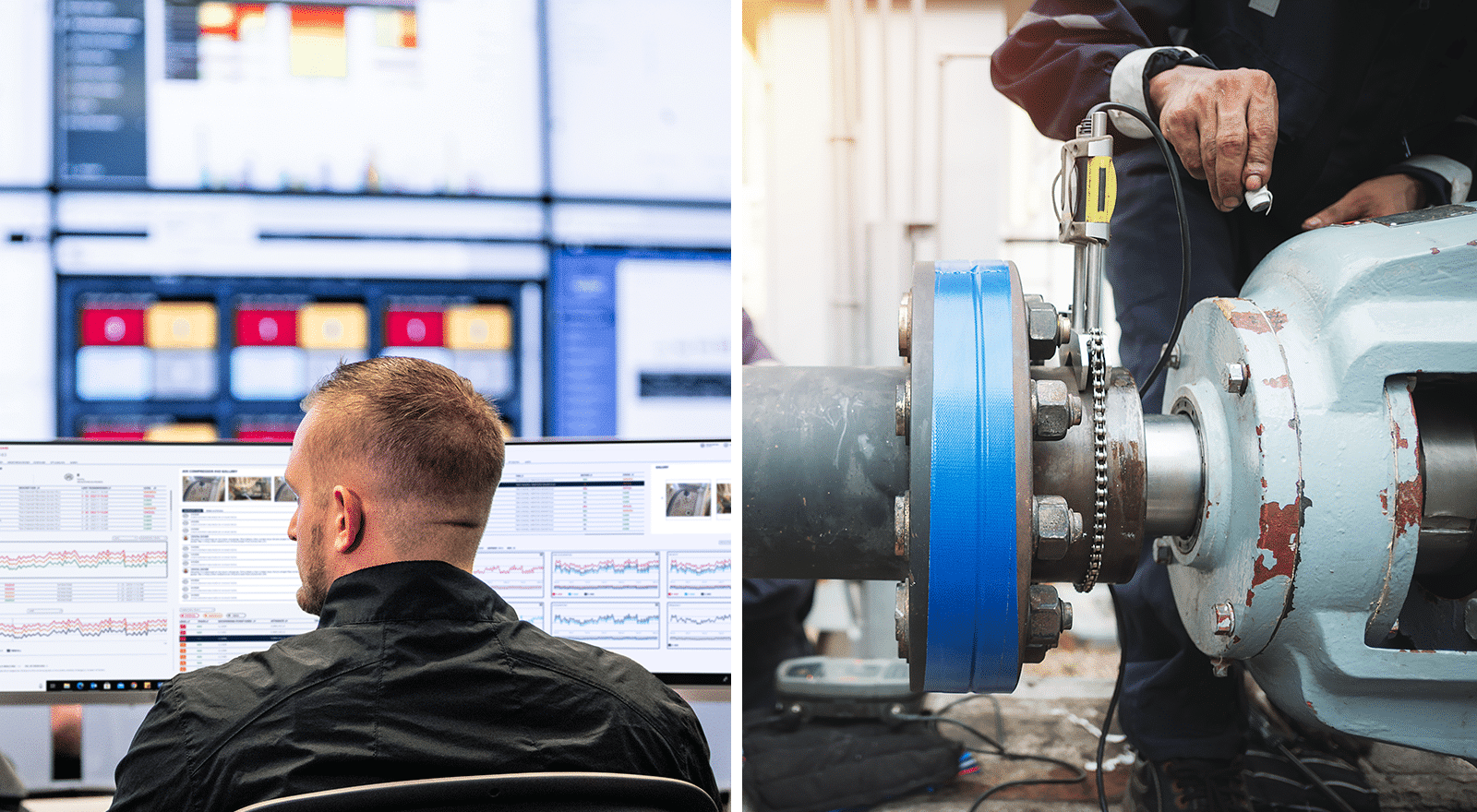
Who monitors my machine health data?
You can rely on our specialized team of condition monitoring experts, including CAT III Vibration Analysts, at our centralized Reliability 360® Technology Center to analyze machine data and provide the on-site maintenance team recommendations on how to address the issue. Using our API-integration, R360® recommendations can be sent directly to your CMMS and a work order will be generated.
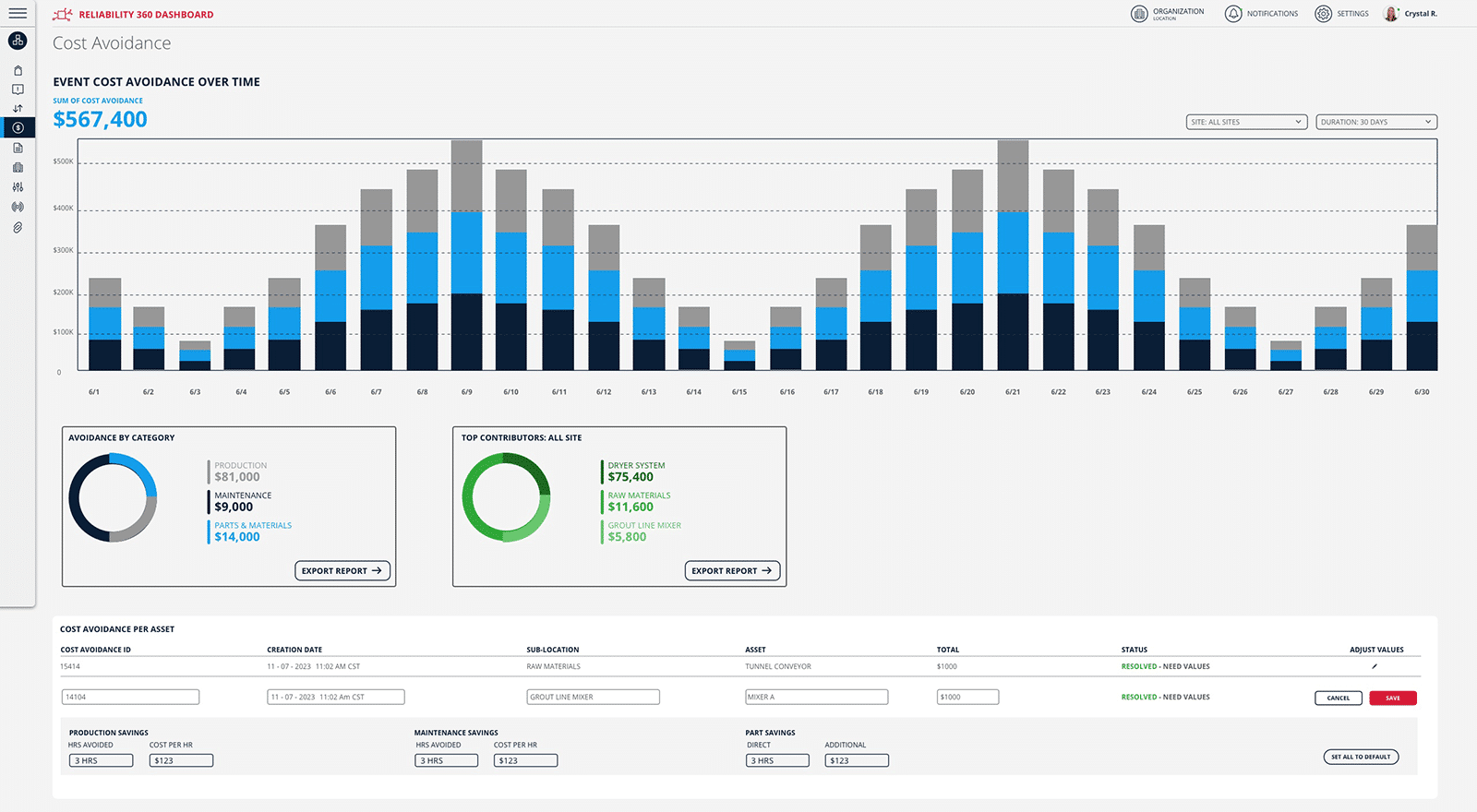
What ROI can be tracked by implementing Reliability 360® Machine Health Monitoring?
Our cost avoidance dashboard allows you to tailor cost avoidance calculations to fit your business. Drive uptime with machine health monitoring, ROI guaranteed.
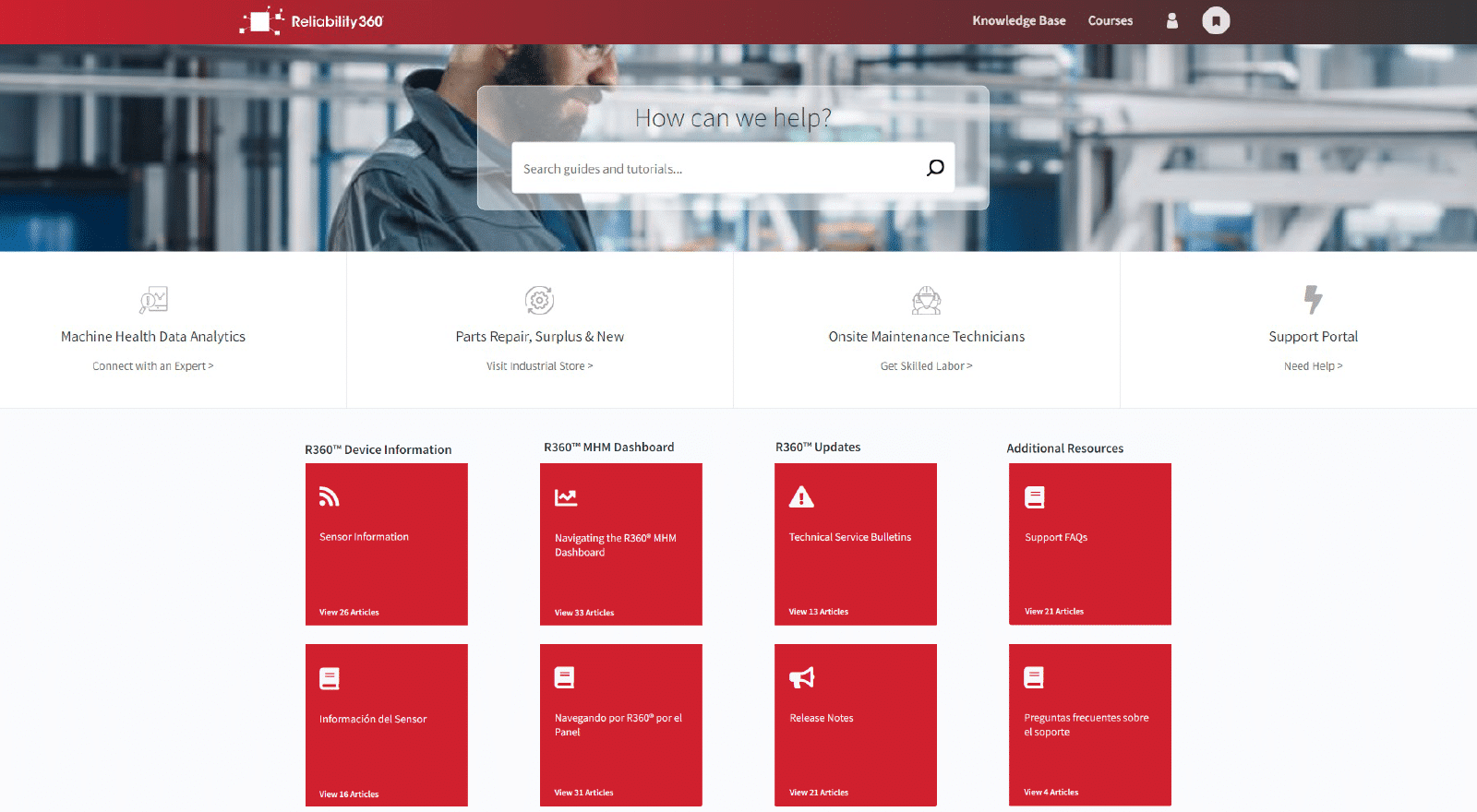
What is the Reliability 360® Knowledge Base?
Our Knowledge Base is an online hub for easy access to product information, new releases, training tutorials and expanded services and support for our Reliability 360® Machine Health Monitoring Solution.