Of the numerous types of industrial sensors in use by manufacturers today, industrial pressure sensors are among the most common — and the most useful. Industrial pressure sensors are a key component of the real-time equipment condition and performance monitoring processes that enable predictive maintenance, one of the most effective ways to increase cost efficiency in the facility.
Whether used to detect hydraulic leaks, optimize flow rates in high-speed lines or another purpose, pressure sensors are essential in modern manufacturing environments. This is especially true in light of emerging smart factory and Industrial Internet of Things technologies that can integrate with these sensors to enable faster and more accurate decision-making. In this post, we will examine the seven different types of pressure sensors, applications in which they are used and the benefits that they can provide.
What is a pressure sensor?
Pressure sensors operate by taking a physical or mechanical measurement of pressure differentials in a vessel, conveyance or other piece of hardware or infrastructure. The main operating principle of an industrial pressure sensor is an apparatus that can expand or contract based on the pressure applied to it, whether by a liquid or a gas.
As pressure changes expand or contract the apparatus, it generates an electrical signal, which is then converted to an output and used for real-time readings, data analysis and other applications to facilitate more effective and efficient equipment maintenance and monitoring. Pressure sensors work with transducers and transmitters to create actionable information for technicians, managers and analysts to use. They can be used to measure absolute pressure as well as gauge pressure and differential pressure. Absolute pressure is the total force exerted by a fluid in addition to atmospheric pressure, while gauge pressure is measured relative to atmospheric pressure. Differential pressure is an expression of the difference between pressures at two different points in a system.
The difference between pressure sensors, transducers and transmitters
Pressure sensors, pressure transducers and industrial pressure transmitters are each able to take pressure measurements and produce data and output, but they are not identical or interchangeable devices or terms. Each plays a unique role in acquiring and communicating data for use, recording and analysis. These roles are:
- Pressure sensors: A pressure sensor operates in a straightforward manner, generating an electrical output based on the action of the mechanical measurement apparatus. The signal from a pressure sensor is in the form of voltage.
- Pressure transducers: Pressure transducers operate in a similar manner to pressure sensors, producing a voltage output signal based on pressure changes affecting a mechanical apparatus. Pressure transducers are able to transmit signals further because they contain built-in signal conditioning.
- Pressure transmitters: Instead of a voltage output, pressure differential transmitters generate electrical current to produce their signal. The means of measurement is the same, via a physical apparatus reacting to pressure differentials.
Types of pressure sensors
There are seven primary pressure sensors used in industries. These sensor types are:
- Vacuum pressure sensors: Vacuum pressure sensors typically refer to Pirani sensors, which generate a signal based on the resistance of an integral sensor filament. As ambient pressure is introduced to the sensor filament, it experiences a temperature differential through contact with airborne molecules — at lower temperatures, less heat is transferred from the filament, while at higher pressures, more heat is transferred. This differential generates a signal which is converted to a pressure measurement.
- Piezoelectric pressure sensors: Piezoelectric sensors operate based on the strength of an electric charge, which fluctuates based on the pressure applied. This type of sensor generates a signal that is directly proportional to the amount of pressure present, meaning that it has an almost immediate response time. A further benefit of this type of sensor is its small size.
- Aneroid barometer pressure sensors: Aneroid barometer pressure sensors use mechanical operation to directly generate a pressure reading based on changes to a flexible capsule apparatus. As the capsule expands or contracts due to applied pressure, it generates a pressure reading through a dial directly connected to it.
- Manometer pressure sensors: Another mechanical sensor type is the manometer, which uses a liquid-filled, U-shaped tube through which the liquid is displaced as a result of applied pressure. This displacement provides a direct pressure reading, a highly accurate method of measurement.
- Bourdon tube pressure sensors: Similar to aneroid barometer sensors, bourdon tube sensors measure the changes in a sensing element to provide a pressure reading. Unlike the capsule apparatus of the aneroid type, the bourdon tube uses its namesake apparatus, a helical or C-shaped tube that straightens as pressure is applied to it. As the tube changes shape on account of pressure applied, it moves a dial, which provides a pressure reading.
- Sealed pressure sensors: Sealed pressure sensors are typically used in unique atmospheric pressure situations, such as submersibles. These types of sensors contain a standardized atmospheric pressure, which is used as the benchmark against which the ambient pressure present is compared. This differential generates a pressure reading.
- Strain gauge pressure sensors: This type of sensor uses a spring to react to pressure application. Changes in the form of the spring generate an electrical signal which is converted to a pressure readout.
Industrial pressure sensor applications
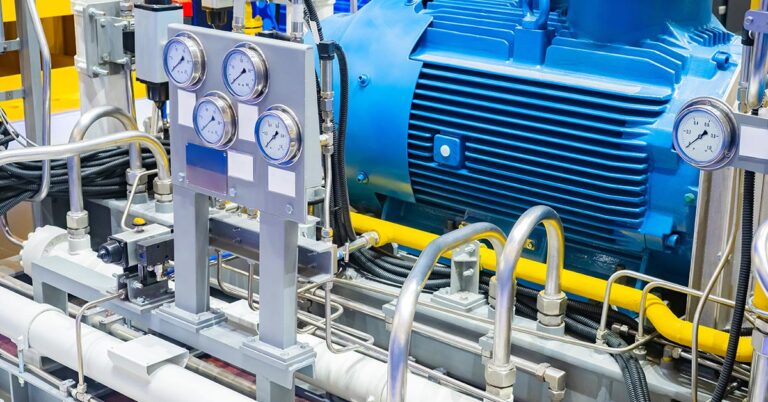
There are numerous valuable pressure sensor industrial applications available, with the broad range of sensor types further expanding the scope of potential uses. Just a few of these applications include:
- Monitoring process flow in equipment: Because pressure sensors are suitable for liquid or gas pressure monitoring, they are useful for a vast array of industrial and manufacturing equipment monitoring. If pressure drops, increases or fluctuations are detected in the flow of any type of liquid or gas in manufacturing equipment, it can be an indication that processes are not occurring to spec, and further maintenance may be required.
- Hydraulic and pneumatic systems: Hydraulic and pneumatic systems are a key component of numerous pieces of manufacturing equipment and processes. When pressure sensors are used to detect aberrant increases or decreases in fluid or air transmission, they can identify potential leaks, blockages and other scenarios that will create inefficient operation, potential equipment damage and eventual unplanned shutdown.
- Vacuum technology: Frequently used in composite molding production, flight instrument manufacturing and other industrial processes, vacuum technology is a key process in manufacturing. Pressure sensors can help to ensure that a true vacuum is maintained in these scenarios and can help to identify potential issues early enough to reduce potential part discards or rework.
- Monitoring tank liquid levels: Reliable fluid and gas storage are critical to ensure uninterrupted manufacturing processes, and pressure sensors are often used to detect potential leaks or other changes to tank storage environments. Early leak detection can reduce material loss, prevent equipment damage, and attenuate health and safety risks.
- Environmental applications: Pressure sensors are often used to measure facility emissions and can alert technicians if these levels exceed acceptable standards, helping to prevent potential violations and fines while keeping the facility in compliance with environmental regulations.
Benefits of industrial pressure sensors
Industrial pressure sensors provide a number of direct benefits, including:
- Data monitoring/diagnostics: Ongoing collection of pressure data through industrial sensors enables real-time monitoring and diagnostics, helping to identify potential issues early on and address them before they cause a machine failure producing lost time and money.
- Predictive maintenance: A proactive, continuous maintenance monitoring approach enables predictive maintenance, which identifies the beginnings of potential failure conditions and enables maintenance personnel to more effectively schedule downtime for inspection and any required repairs. In practice, this means that unplanned downtime can be nearly eliminated, and equipment can run more efficiently, leading to ROI increases, cost reductions, improved output and throughput, and more.
- Reduced energy consumption/improved sustainability: Pressure drops are among the most significant detriments to efficiency in a manufacturing facility, requiring more energy to produce the same result. By identifying potential pressure drop scenarios, these sensors can improve energy efficiency and create a more sustainable operation.
Selecting the right pressure sensor
Manufacturers should take care when selecting a pressure sensor for their operations. If you don’t take the time to carefully consider your existing equipment and potential needs, there’s a chance the instrumentation you choose will not provide you with the most useful results. When considering your options, you should bear in mind factors including:
- Operating pressure range
- Media compatibility (gas, liquid, corrosive substances)
- Temperature range
- Signal output type (voltage vs. current)
- Environmental sealing (IP rating)
- Integration with IIoT systems
Pressure sensors have a broad range of uses that can provide benefits in numerous areas. ATS offers expertise in machine health monitoring with maintenance and reliability support to improve uptime. To learn how our industrial technologies and services fit into an overall predictive maintenance program, contact us today.