As industrial automation has advanced and expanded, the promise of true “lights-out” manufacturing has been one of the most consistent objectives that manufacturers cite in the benefits of this technology. Lights-out manufacturing — sometimes also called the dark factory, or dark manufacturing — refers to the idea of fully automated production that doesn’t necessarily require the on-site presence or intervention of human workers, with the name derived from the assumption that automated equipment does not need the lights on in order to operate. Although some of these facilities are truly 100% free from human workers, many use only partial automation and run shifts with people present.
Some of the factors that have contributed to the rise of so-called dark factories are labor shortages around the world, the rising cost of human resources and the acceleration of automation in the post-COVID landscape. Here, we will look at how the dark factory is coming to fruition, and what the potential benefits of unattended manufacturing can be.
What is a dark factory?
A dark factory or “lights out” manufacturing plant is one that is automated and requires little or no human intervention. It relies entirely or almost entirely on advanced technologies like robotics, artificial intelligence and Internet of Things systems. Ideally, these automated production lines can run without human presence, which can lead to maximized efficiency, lower overhead costs and minimal errors.
Requirements for dark manufacturing
The lights-out facility — or even lights-out areas of the facility, or lights-out shifts — requires a number of technical and process elements in place, the implementation of which often requires a dedicated digital transformation strategy by the manufacturer. These requirements draw from a range of automation technology, Industry 4.0 in manufacturing, Industrial Internet of Things technology and more, including:
- 5G/High-Speed Connectivity: Wireless connectivity enables real-time communication between machines, cloud service and predictive maintenance systems.
- Industrial Sensors: These capture data from equipment, enabling live monitoring and supporting preventive maintenance.
- Collaborative and Autonomous Robots: Known as “cobots,” these machines work in tandem with people or independently across numerous repetitive practices.
- Artificial Intelligence/Machine Learning Systems: These algorithms drive autonomous decision-making, predictive maintenance and adaptive optimization.
- Digital Twins: This technology allows for testing of manufacturing systems and making equipment changes virtually before real-world deployment.
- QC Automation Tools: With machine vision systems and metrology devices, dark factories can verify production accuracy without human intervention.
- Standardization of Processes: This is essential for repeatability and programming automation rules.
- Cybersecurity and Physical Security: Protecting sensitive automated systems from cyber threats and unauthorized physical access is critical for ensuring uninterrupted and safe operations.
Lights-out manufacturing examples
Lights-out manufacturing is seeing use across a broad range of industries and applications. In some cases, such as pharmaceutical manufacturing and semiconductor manufacturing, lights-out manufacturing is not just an efficiency benefit but is essentially a requirement in order to properly carry out the processes at hand. This is because these processes require strict contaminant control and high-precision processes with extremely slim margins for error or variance — all of which cater to the strengths of fully automated processes where human workers are not directly involved.
Other examples of dark manufacturing strategies and facilities that are already occurring include:
- FANUC: Robotics company FANUC operates at least one plant, located in Japan, on a completely lights-out basis. At this facility, automation robots make more robots, and the facility is reportedly capable of operating without human intervention for 30 days at a time.
- Philips: Philips operates a razor-manufacturing facility with minimal human oversight — nine staff members oversee quality assurance, while all production processes are automated.
- Amazon: While not a manufacturer, Amazon is at the cutting edge of extensive industrial robot use for inventory and fulfillment, with a particular focus on collaborative robots (cobots) working with staff to increase efficiency and throughput.
- Tesla: The automaker uses heavily automated “gigafactories” with robotic arms for battery production.
- GE Additive: GE has been on the leading edge of advanced lights-out metal additive manufacturing with comprehensive machine monitoring.
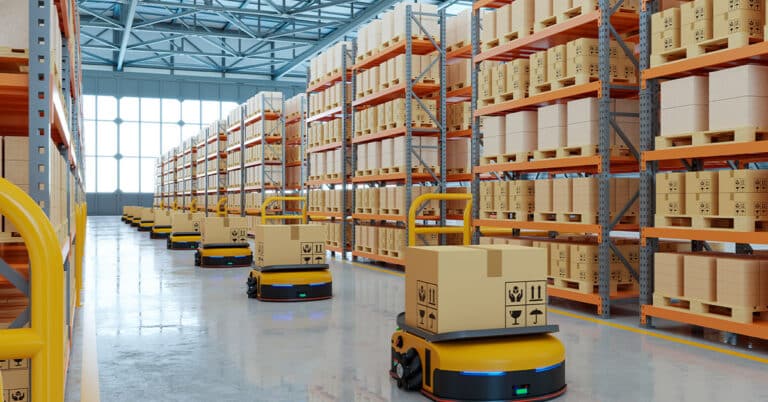
Dark manufacturing and similar processes are also increasingly used in micro factory applications built specifically for high levels of automation. In addition, hybrid factories exist that feature cobots working alongside humans during the day, transitioning to fully autonomous production runs during overnight shifts.
Benefits of lights-out manufacturing
- Improved accuracy: Fully automated manufacturing processes eliminate the chance of human error, which is one of the leading root causes of production errors and rework. Once programmed correctly, robots and automation equipment carry out the same process, at the same time, over and over.
- Scheduling and uptime benefits: Automation equipment does not take lunch breaks, holidays or sick time, meaning that it is theoretically able to operate 24/7/365. Shifts do not need to be covered or canceled with fully automated processes.
- Lower costs: Automation can reduce labor costs while also creating production efficiencies that further reduce costs by increasing production speed and reducing or eliminating the need for rework or part discards due to quality errors.
- Higher-value tasks for workers: By shifting the most monotonous tasks to industrial robots, facilities can better leverage the knowledge and expertise of their staff to higher-value areas: troubleshooting, strategy, innovation/R&D and more.
- Energy savings: Running a factory with minimal lighting and HVAC use contributes to energy efficiency and helps reduce utility costs.
Common challenges in lights-out manufacturing
Manufacturers who want to incorporate lights-out manufacturing into their operations need to overcome some obstacles before they can realize the full benefits. For example, there’s the high initial investments involved. Staff also needs to be retrained to ensure they understand how to work alongside cobots and maintain automation systems.
Overcoming these challenges can be achieved with a variety of approaches, including:
- Pilot programs: Starting with a single area or process for lights-out, such as a QA lab or fulfillment cell, can help you get the ball rolling without a much larger expenditure.
- Predictive maintenance: Adopting preventive maintenance principles if you haven’t already can prevent critical failures and keep your systems running as smoothly as possible.
- Modular robotics: A modular automation suite gives you the flexibility and scalability to phase in your lights-out program over time, helping you save money and troubleshoot the systems in a gradual manner.
At ATS, we offer expertise in Industry 4.0 implementation and technology focused on condition monitoring and predictive maintenance for improving your overall operational efficiency. From reliability expertise to analytics support, we work with you to help eliminate unplanned downtime. To learn more, contact us today.