As manufacturing continues to evolve and adapt, microfactories are one of the most promising concepts among the smart manufacturing trends driving the industry forward. Drawing on advanced technology and automation while catering to the needs of today’s manufacturing customers, the microfactory, also known as micromanufacturing, is poised to help manufacturers improve margins and increase customer responsiveness — all at comparatively low overhead compared to conventional factory builds. This article will explore micromanufacturing processes, benefits and optimal use cases.
A microfactory is a highly automated facility, built to provide a focused, vertically integrated set of start-to-finish manufacturing services. The microfactory is based on a cellular configuration, where pieces can move from one station to another in any order, not necessarily in a linear fashion, and can even return to the same station more than once in a production process. Microfactories use advanced technology and automation to offer exceptional efficiency in customized designs. The rise of Industry 4.0, with its emphasis on connectivity and automation, has been a major driver of this concept throughout the manufacturing sector over conventional factories.
The origin of the microfactory
The concept of the microfactory was first introduced in 1990, with the Mechanical Engineer Laboratory (MEL) of Japan working to reduce the size and footprint of traditional manufacturing equipment to improve efficiency. This system eventually led to the cellular, modular format of today’s microfactories. With early success in prototyping and custom, low-volume work, the potential of the microfactory system quickly became apparent.
As technology caught up, circumstances provided the perfect opportunity for the microfactory to experience a resurgence. One of the primary benefits of microfactories is that they can be installed almost anywhere, including in existing warehouses or vacant facilities, without the need for major retrofitting. Microfactories are also designed to operate in proximity to the customer base.
With the global supply chain disruptions brought on by the COVID-19 pandemic, the microfactory concept became an optimal solution to reduce supply chain risk, improve operating margins for manufacturers and allow customers to order nearly any quantity, that is, without minimum volume requirements.
A global network of smaller, more agile manufacturing facilities became a very real advantage in a time of uncertainty where larger facilities experienced issues adapting and keeping up with demand. The advantages of microfactories are continuing today.
Understanding the micromanufacturing process
What sets the micromanufacturing process apart? Several factors:
- High levels of automation: Microfactories are designed for most processes to be accomplished through automated production.
- Cellular configuration: Rather than the traditional linear production line, where a piece is moving forward through a series of processes, microfactories are designed in a cellular or modular fashion, allowing pieces to move among different stations in any order needed, supporting increased customization.
- More design flexibility: Microfactories incorporate technology and configurations that support high levels of customization, enabling much greater design flexibility than higher-volume facilities with rigid design requirements.
- Hyperlocal production: Microfactories are a key part of building a smart factory and can be installed in nearly any type of facility, without the need for brand-new buildouts or extensive retrofitting. This means that they can usually be stationed much closer to customers than a traditional factory, which stabilizes the supply chain, increases reliability and reduces costs.
Some of the most important technologies enabling the emergence of microfactories include:
- Advanced robotics
- IIoT sensors
- Digital twins
- On-demand 3D printing
- Edge computing
Pros & cons of a microfactory
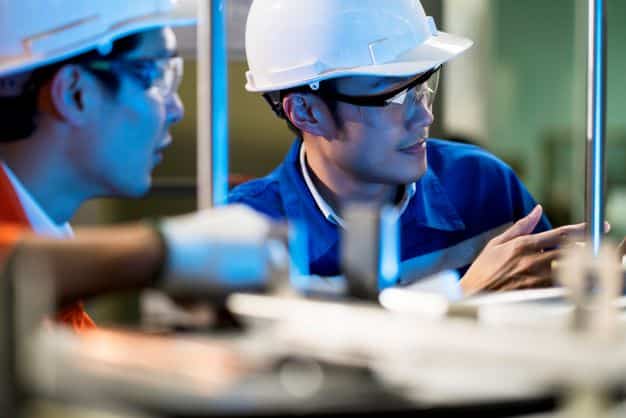
The modular microfactory offers a number of benefits, while also incorporating several scenarios where traditional manufacturing may still be the right choice. Here, we will look at the pros and cons:
Benefits:
- Improved efficiency through automation
- High levels of customization
- Proximity to customers
- Global, connected network of manufacturing facilities
- Smaller footprint — can be deployed in nearly any type of existing facility
Drawbacks:
- May not be the most cost-effective option for high-volume, low-mix manufacturing
- Limited material or design options owing to the nature of microfactory equipment
- Difficulty with inbound logistics because of a broadly distributed network of facilities (though this may be offset by outbound efficiencies)
- Challenges related to integrating with existing systems
- Staffing the small, dedicated teams that are required to keep microfactories operational and efficient
Real-world applications of microfactories
Numerous sectors already are reaping the benefits the microfactory concept can provide. Some of the industries that have adopted this idea to great success so far include aerospace prototyping, medical device manufacturing, electric vehicle components and consumer electronics. Examples of products made using these facilities include custom brackets, rapid prototypes and limited-run consumer products.
With these concepts in mind, you now understand the purpose, design and benefits of the microfactory. While a microfactory implementation may or may not be the right choice for every business, the ideas of automation, technology and efficiency are universal and are in higher demand than ever. If you’re interested in adapting these ideas in your operations, ATS can help you achieve it. Our expertise in predictive maintenance and implementing smart factory technology makes us the ideal partner for your digital transformation journey. Reach out and speak with a member of our team today to learn more about what we can do for you.