Predictive maintenance is a data- and technology-based method of carrying out proactive maintenance. A primary objective of predictive maintenance is to identify potential production issues well before they lead to machine shutdown. This is done through constant equipment performance monitoring enabled by sensors, data collection, and near-real-time communication between equipment and software. Predictive maintenance can offer numerous, unparalleled benefits in productivity and efficiency — benefits that we will explore in greater depth later in this piece. It is also important to understand predictive maintenance challenges exist, but are well worth the future ROI of a predictive maintenance program.
Benefits of predictive maintenance
The benefits of predictive maintenance in manufacturing are numerous and will almost always offer a positive return on investment over time. These advantages may include:
- Proactive machine health monitoring: Predictive maintenance technology can alert personnel to potential issues well before they result in equipment failure.
- A vast reduction in unplanned downtime: Early alerts of issues means that maintenance technicians can prepare to make the necessary repairs or adjustments with minimum downtime and no interruption to planned production runs.
- Control over scheduling: The ability to plan for equipment repairs means that maintenance scheduling can be done to maximize productivity and resources.
- Improved equipment safety: By verifying that equipment issues are addressed prior to failure, predictive maintenance creates an overall safer facility. Machinery will ideally never get to a point where it is operating far enough out of spec to pose a safety hazard.
- Enhanced product quality: By keeping equipment running as designed, a much higher percentage of production output will be produced to spec — reducing rework and discards and achieving customer satisfaction.
- More efficient maintenance spend: While predictive maintenance and preventive maintenance are components of a comprehensive maintenance strategy, predictive maintenance allows for a more focused use of resources on identified issues, as opposed to preventive maintenance that occurs whether or not it is required. Understanding the difference between preventive maintenance and predictive maintenance therefore is an important element of your strategy.
- Cost efficiency: Predictive maintenance can do more to improve your operations’ cost effectiveness than just preventing breakdowns. On top of that, predictive maintenance analytics techniques can provide greater energy efficiency by keeping equipment in optimal condition for as long as possible. Optimized inventory management is another way in which these strategies can help you keep your costs under control.
The above predictive maintenance benefits represent tangible, demonstratable advantages to the bottom line: increased production capacity and productivity, and a more efficient maintenance practice that vastly reduces downtime — one of the biggest wastes of productivity in the facility. Advanced Technology Services is a leading global services provider with over three decades of proven experience in delivering optimal productivity through decreased downtime and greater efficiency, resulting in higher customer profitability.
Challenges of predictive maintenance
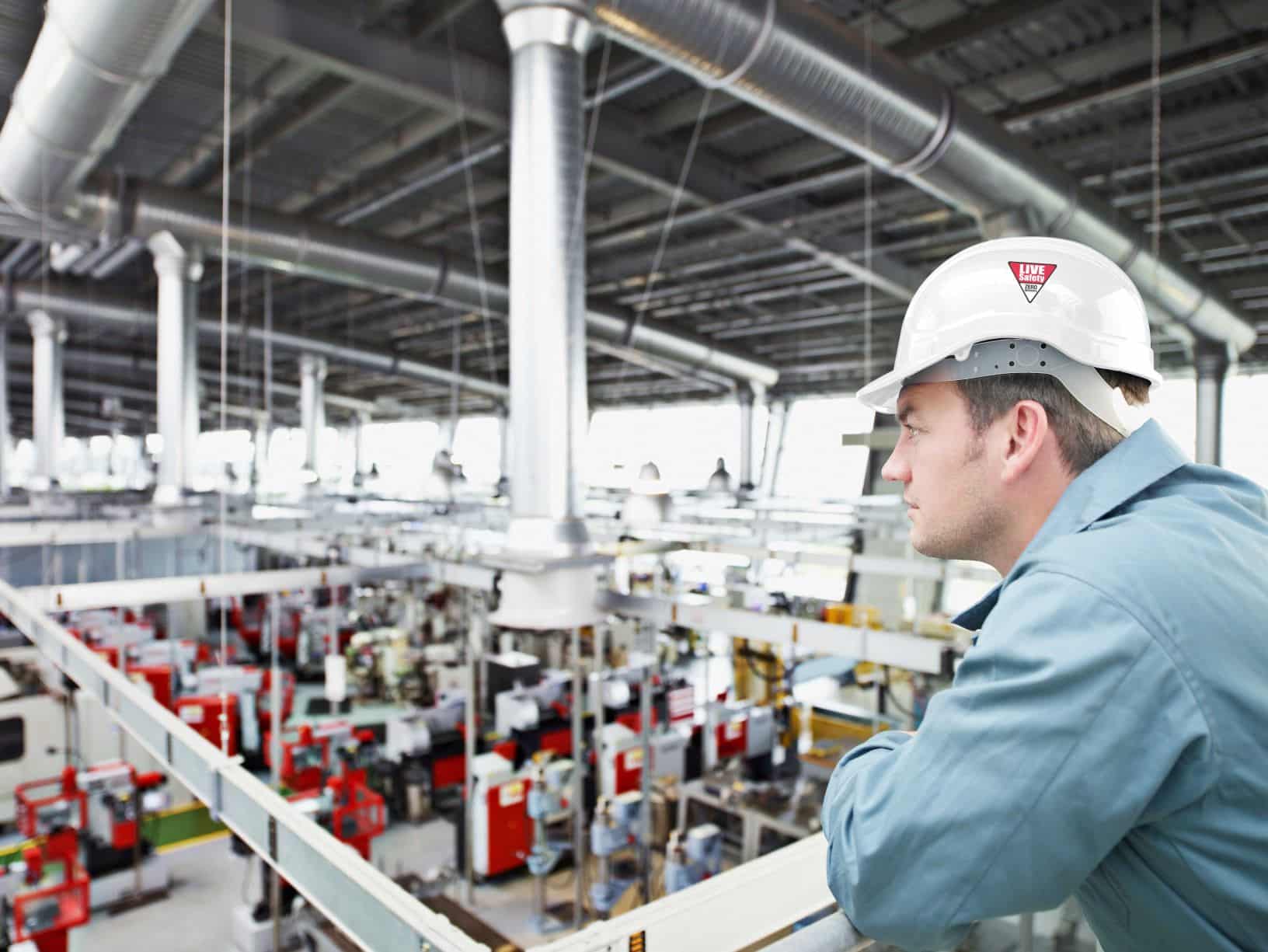
Implementing a modern predictive maintenance strategy is no small undertaking. After exploring the predictive maintenance benefits above, we will now take a look at the challenges this technology-based program can present:
- State-of-the-art connectivity via sensors or “smart” equipment: Connectivity and data communication are the backbone of predictive maintenance. By collecting and monitoring data about intricate aspects of equipment processes — small changes in vibration, temperature and equipment sounds — a system is able to determine that maintenance is required, well before the equipment fails. This data is collected via aftermarket sensors or sometimes, for newer equipment, from sensors built-in to the equipment. The data must also be transmitted to a central repository where it is monitored and analyzed for actionable insights.
- Data security: Information security should be a primary concern for any “connected” organization: meaning — in this day and age — any organization doing business featuring any digital aspect. In terms of predictive maintenance, it is critical to guarantee that equipment performance data is not subject to access by outside parties and that outside parties are not able to control predictive maintenance systems. At a more baseline level, it also remains important to protect information such as customer data.
- Integration: As mentioned above, data may be collected through aftermarket sensors or built-in, cutting-edge equipment. This data must then be communicated to a central system — often a CMMS (computerized maintenance management system), but sometimes an ERP (enterprise resource planning) system. In any scenario, it is crucial that all hardware, software and equipment can “talk” to one another effectively, and that communication is occurring as quickly as possible (in near real-time). Implementing predictive maintenance hardware and software is only a first step in the process. Integration is the step that assures everything works together as it should.
- Higher upfront costs and investment justification: It is no secret that predictive maintenance involves higher upfront investments than standard preventive maintenance. All of the sensors, equipment and software described above incur costs, as well as the personnel to make sense of the data and drive decisions based on that information. As you will see below, this higher investment yields major benefits short and long term.
Predictive maintenance analytics considerations
Understanding how to implement predictive maintenance includes knowing how to harness the power of analytics. Some of the most important considerations that factor into predictive analytics in manufacturing include:
- Data sources for predictive maintenance: The core of predictive maintenance is the wealth of data provided by your equipment. Through a network of sensors, controllers and gateways, you’re given a real-time resource of insights into your machinery’s condition. This serves to supplement the existing knowledge-based and user-based trove of information you already receive from your maintenance logs, technician expertise and other traditional resources.
- Types of predictive maintenance analytics: Manufacturers typically use descriptive and diagnostic analytics to understand past machine behavior and diagnose problems after they occur. Where predictive and prescriptive analytics differ is in how they leverage existing data to forecast potential machine failures and streamline the decision-making process to prevent these failures from occurring in the first place.
- Data requirements for predictive maintenance: To be at its most effective, predictive maintenance implementation needs to be built upon a solid foundation of relevant and sufficient data. Examples of datasets that are most useful include error history, machine operating conditions and sensor coverage.
- Model evaluation: Data models are evaluated based on ROC curves, AUC and confusion matrices to ensure the highest levels of accuracy when predicting machine failures. It is critical to have interpretability, error analysis and performance monitoring to improve the algorithms over time.
- Modeling strategy: The remaining useful life (RUL) metric is one of the most important elements used to predict when a machine may fail and when to schedule maintenance. In addition, various machine learning models are used for anomaly detection and survival analysis to predict failure windows.
- Modeling deployment: Deploying predictive models for machine health monitoring depends on factors such as data size, latency and decision time. Predictive maintenance systems can be deployed through cloud-based systems, industrial edge computing for real-time analysis or hybrid models that balance both approaches.
Although the challenges discussed in this piece require effort and investment to overcome, it is well worth it for the improved productivity, efficiency, reliability and ROI. ATS offers a technology-driven approach to maintenance including predictive maintenance, remote monitoring and analytics and sensors to help modernize your facility, enable data-based decision-making, and provide all of the benefits discussed here. We also can help you incorporate advanced technologies such as the Industrial Internet of Things (IIoT) to enhance your predictive maintenance strategies. For more information, contact us today.