Industry 4.0 is the fourth industrial revolution, which, for manufacturers, means a “smart,” connected facility. With advanced automation, real-time communications and remote monitoring — and a massive amount of data with which to drive decision-making — the impact of Industry 4.0 on manufacturing drives unprecedented advances in quality, reliability and agility.
Industry 4.0 takes existing tools, such as automation robots and CMMS software, and applies the benefits of the connected facility to make them more powerful than ever. This creates benefits such as process control optimization, more effective and proactive maintenance, and the flexibility for personnel to fulfill their tasks from anywhere. Numerous types of technology make these benefits of Industry 4.0 possible, including equipment sensors, 4G and 5G network communication, and the aforementioned automation and software tools that many manufacturers use today. Throughout the rest of this piece, we will explore specific Industry 4.0 benefits in manufacturing in greater depth, as well as the new practices that Industry 4.0 enables.
Impact of industrial revolution 4.0 on manufacturing: What will change?
Countless manufacturing plants are already taking advantage of at least some Industry 4.0 principles and technology, and you may be one of them. Here, we will take a more expansive look at what exactly Industry 4.0 can entail, to help you envision the full possibilities of this factory of the near future:
- Data monitoring and collection through sensors: Sensor technology is, in many ways, the backbone of Industry 4.0, enabling the near-real-time monitoring and data collection that drives data analysis and more informed, effective decision-making for maintenance, process control, inventory, personnel management and more. To be most effective, every piece of equipment in the facility — new or old — should be equipped with monitoring sensors. While these sensors are standard on most new equipment, older machinery can be retrofitted to take advantage of the benefits as well.
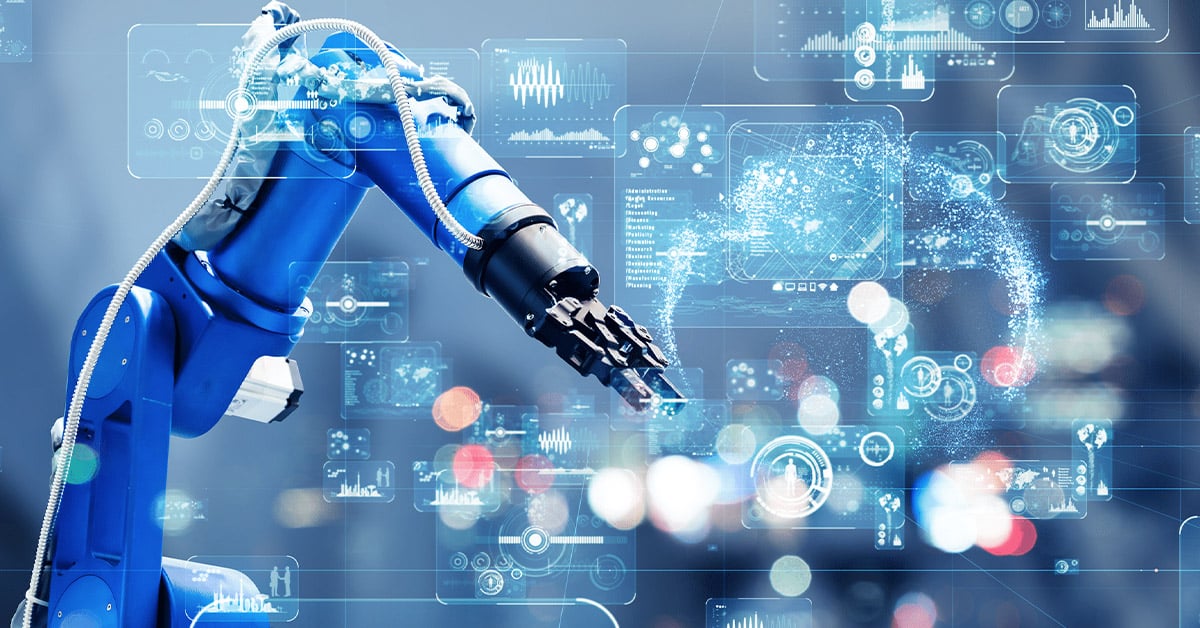
- Expanded communication between equipment and systems: In addition to sensors, networking technology — especially on the eve of widespread 5G access — plays a major role in the effects of Industry 4.0. While siloed — discrete communication between equipment and systems such as CMMS has been present for quite some time — Industry 4.0 represents a huge leap. This momentum has resulted in a fully interconnected facility where all equipment feeds data into software systems that allow for nimble, effective decision-making at macro- and micro-levels.
- More advanced automation: Automation is, of course, nothing new in manufacturing. Industry 4.0, however, advances automation technology even further. This technology enables more informed programming; more innovative ways of people and robots working together; and an overall increase in efficiency, safety and productivity.
- Data analytics and action: With the massive amount of data being collected in real-time, areas such as process control become more effective with the ability to fine-tune and adjust more effectively. Though one of the main advantages of Industry 4.0 data analytics is more reliability-centered maintenance — including predictive maintenance that reduces downtime, increases productivity and keeps the facility operating at peak performance.
How does industry 4.0 impact — and benefit — key manufacturing areas?
The processes described above can make major impacts throughout a manufacturing operation. Key areas to look for benefits include the following:
- Productivity: With more data, more connectivity and communication, more efficient maintenance, and more effective process control and automation, the facility is on track to see unprecedented productivity increases. These gains yield improved throughput, optimized product quality, more efficient use of resources, and enhancements in uptime and inventory management — two areas that we will discuss below.
- Uptime: Performance monitoring, data collection and fully connected CMMS software all enable more effective maintenance, ensuring that preventive maintenance is completed as scheduled, and facilitating predictive maintenance — detecting the beginnings of equipment malfunctions before they cause production interruptions. This allows you to schedule corrective maintenance at less disruptive times while better ensuring that the right equipment and personnel are on hand — all of which reduce downtime, speed repairs and keep equipment running as expected, when expected.
- Inventory: Sensors and other Industry 4.0 technology aid in more effective inventory management by guaranteeing that counts are accurate and parts are where they are expected to be. Industry 4.0 principles can also be applied to analyze procurement and supply chain partners and provide more flexibility in sourcing.
- Competitive edge: On the customer side, Industry 4.0 helps you keep clients happy on two major fronts: quality and timeliness. With more uptime, far fewer unexpected breakdowns, and optimized processes and operations, the connected facility can become a differentiator in the crowded, competitive manufacturing landscape.
- Profit margins: Every minute of equipment downtime cuts into your profit margins — exponentially more so when that downtime is unexpected. By reducing downtime and introducing more advanced, innovative automation possibilities, Industry 4.0 can improve the bottom line and repay the equipment and infrastructure investments that you’ve made.
- Documentation and record-keeping: By connecting processes such as preventive maintenance and predictive maintenance with systems such as CMMS, Industry 4.0 enables more efficient and accurate record keeping. As a result, necessary tasks and functions are carried out as needed — reducing redundant work as well as missed responsibilities.
ATS services are built to take advantage of Industry 4.0, with offerings including predictive maintenance, Reliability 360® remote monitoring and analytics, and sensor technology. These capabilities are all part of our Comprehensive Maintenance Solution — a technology-based approach to maintenance that will address your challenges, exceed your expectations and deliver the ROI results your business needs. To learn more, contact ATS today.