The introduction of computers in industrial plants was revolutionary back in the day. It marked the beginning of the digitization of manufacturing information – from written and typed words to computer-readable formats – and massively curtailed dependence on paper-based records.
We are now in the midst of Industry 4.0, the next exciting revolution in manufacturing, where computerized systems and processes are vastly more connected, intelligent, automated, and autonomous. The term “digital factory” was coined for plants that are currently or striving to become completely “digitalized.”
Leaders in the digital transformation of existing (brownfield) plants are optimizing the application of cutting-edge technologies and digital information to streamline crucial business processes and deliver improved outcomes. Some are also using the new capabilities to realign their overall business model. Many begin with a proof-of-concept pilot involving a critical asset, system, process, or production line, before investing in further deployments. In comparison, new (greenfield) plants can be built from the ground up as cutting-edge digital factories.
Five common denominators in digitalization
What is a digital factory? Whether fully digital or still making the transition, digital factories have the following characteristics in common:
- Connectivity: Cloud, network or hybrid connectivity exists between software applications, automation systems, machines, and edge devices – within the site or across the enterprise – and potentially among authorized equipment and service providers. Connectivity facilitates the standardization of technology and software platforms as well as work processes, data, performance metrics, reports, and dashboards. By design, it increases productivity and efficiency, improves cost-effectiveness, and allows organizations to better coordinate business goals and objectives.
- Advanced intelligence: Intelligent data processing, analytics, and a higher degree of automation are supported. Digital factories augment human intelligence with artificial intelligence (AI), machine learning (ML), pattern recognition, and smart analytics to make better and more timely maintenance decisions and fine-tune asset and operational performance. They can leverage digital models or “twins” of critical assets, systems, or complete factories to simulate process or equipment changes, complex maintenance tasks, or engineering improvements before applying them in the live environment.
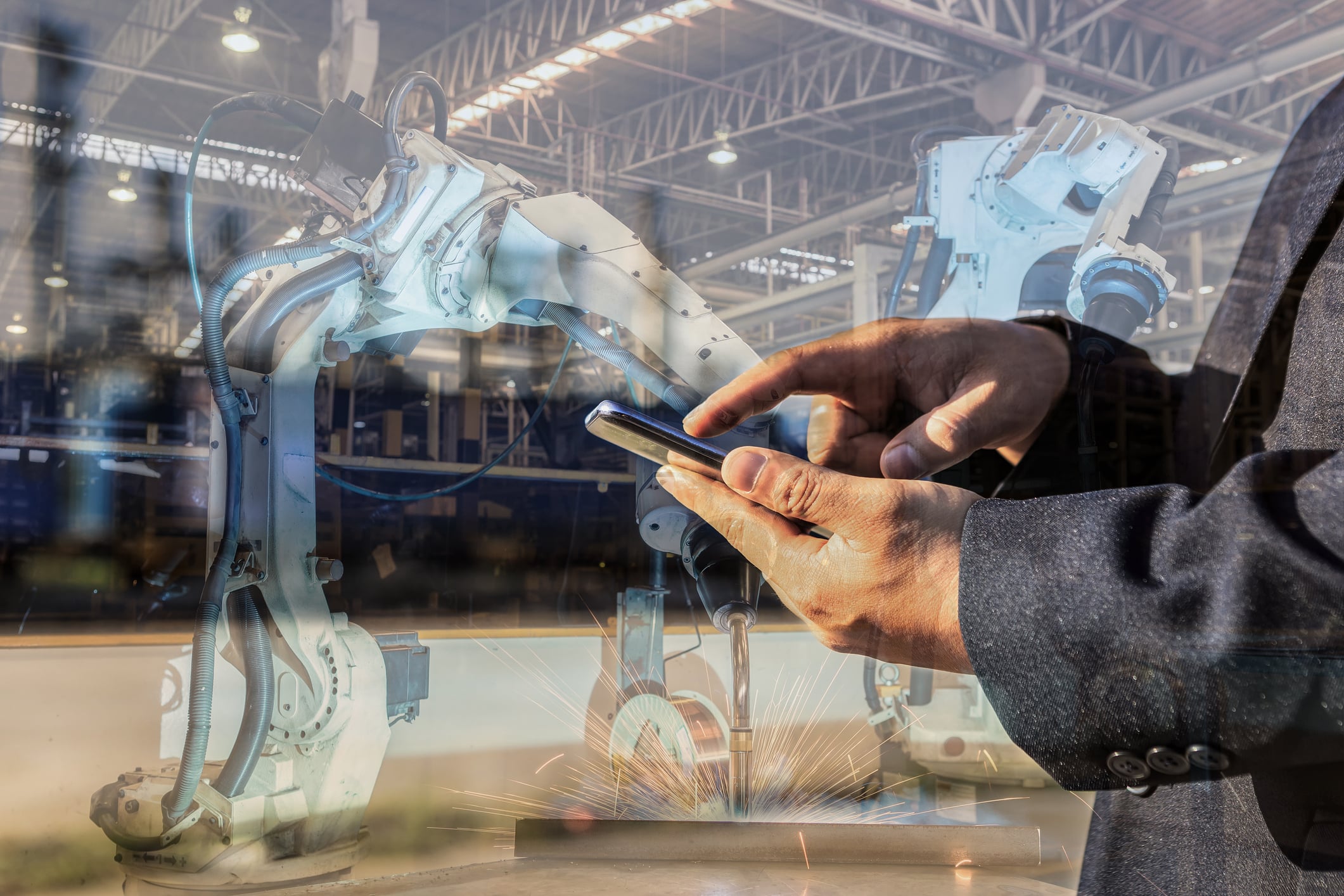
- IIoT enablement: Connected industrial internet of things (IIoT) devices may include smartphones, tablets, or rugged data collectors; wired or wireless machine sensors; robots or cobots (collaborative robots); autonomous vehicles; drones; security cameras; wearable safety technology; or portable condition monitoring (CM) devices such as infrared (IR) thermography cameras, vibration analyzers, or ultrasonic leak detectors. Using IIoT devices, companies can streamline or automate cumbersome tasks and aggregate and analyze insights from a broader collection of data.
- Extended reality: Augmented reality (AR), virtual reality (VR), and mixed reality (MR) technologies improve the employee experience. They enable remote inspections, real-time collaboration, expert diagnostics, guided assistance, immersive training, virtual demonstrations, and interactive design reviews.
- Maintenance optimization: Remote monitoring sensors on critical machines and systems stream condition and performance data for real-time ML and analytics. This allows reliability teams to restrict preventive maintenance (PM) and run-to-failure (RTF) strategies in favor of predictive maintenance (PdM), which provides early warning of degradation, and prescriptive maintenance (RxM), which is predictive but also recommends corrective actions. Some plants will incorporate digital twins to test maintenance plans and assess upgrade and replacement strategies, and extended reality to improve collaboration, decision making, and maintenance precision. With these solutions, plants can reduce maintenance costs and downtime and extend asset life. They also increase worker safety, regulatory compliance, and environmental sustainability.
Digitalization serves many purposes
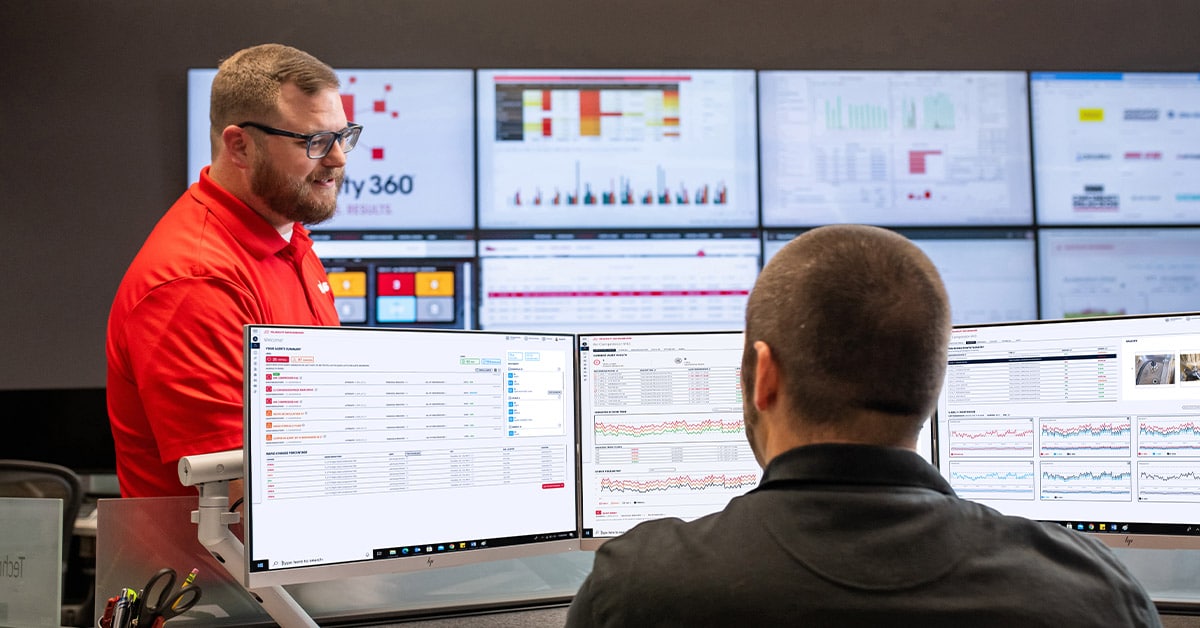
Digital factories inherently address challenges such as skills gaps, manpower shortages, remote and mobile workers, and the loss of tribal knowledge from retiring personnel. They automate repetitive, hazardous, distant, and unskilled tasks, allowing personnel to focus on more beneficial roles such as root cause failure analysis (RCFA), criticality analysis, standards enforcement, and platform optimization. Digitalization also enables new manufacturing business models such as mass customization, dark factories (lights-out manufacturing), servitization (delivery of aftermarket services), and regionalization. It promotes consistency in plants across the enterprise and improves uptime, productivity, quality, performance, and cost-effectiveness.
New opportunities for expert assistance
Besides improving visibility and collaboration internally, digital factories also enable expert maintenance partners to provide asset monitoring and management services. Because ATS partners with leading process and discrete manufacturers across a wide range of industries, they have amassed a robust knowledge base of equipment expertise from which to make asset maintenance and management recommendations through actionable insights.
From the installation of machine health monitoring sensors to the Reliability 360® Technology Center and skilled maintenance technicians, ATS’ team of reliability experts will support your digital transformation by collecting and analyzing machine data and recommending action plans to eliminate unplanned downtime and improve OEE. The Reliability 360® Technology Center, an extension of our industrial maintenance services, represents a technology-based approach to asset health and improved productivity powered by over three decades of maintenance, MRO and reliability expertise. To learn more, contact us today.