In the course of changing nearly everything about the way we live and work, the COVID-19 pandemic has had an especially interesting effects on manufacturing. While the pandemic is certain to make a lasting impact, the short-term effects on manufacturers have been unpredictable and varied.
For example, some manufacturers experienced significant slowdowns in orders as workers and consumers remained at home to flatten the pandemic curve. Facilities that were forced to shut down completely were, of course, unable to engage in any production at all. Other manufacturers experienced major short-term demand increases in critical-needs areas such as ventilators, testing equipment, masks and medical devices. Sectors like paper goods that saw increases while already operating at near-100% capacity were able to respond by temporarily diverting resources from lower-demand areas to those with higher demand. Over the longer term, many of the safety precautions that have become part of everyday life during the pandemic – social distancing, a renewed focus on handwashing, masks, reduced capacity – will gain footholds as either permanent or “for the foreseeable future” safety best practices in manufacturing. Below, we’ll take a closer look at those practices and more.
Precautions to prevent the spread of COVID-19
Precautions that manufacturers will need to take – both in the short term and, in many cases, the long term, include:
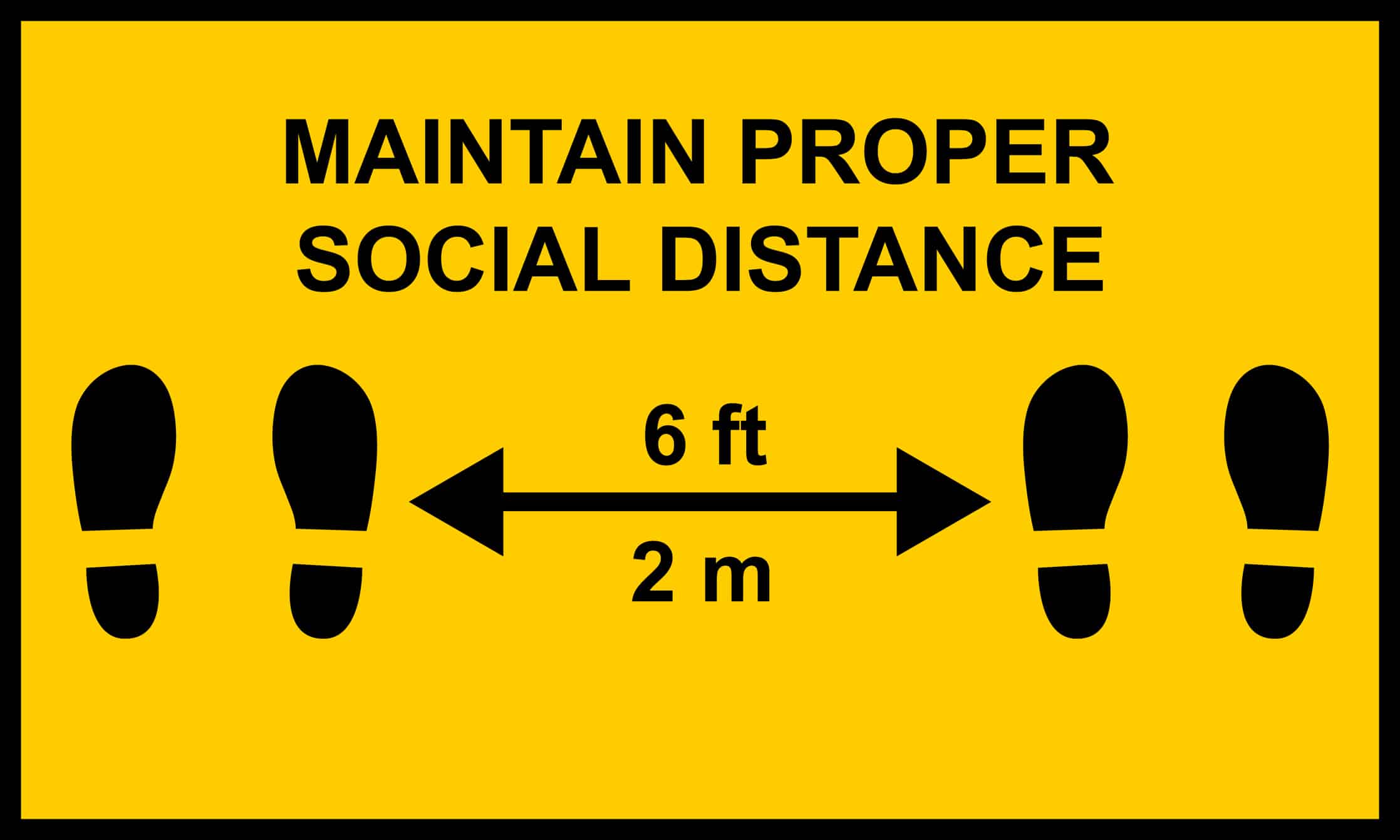
Social distancing: When encouraging employees to practice social distancing in manufacturing, consider ways to segregate/isolate certain portions of your facility so that issues arising in one area do not impact other areas. To promote social distancing, consider implementing the following:
- Add visual indicators at locations where many people are present, including the production floor and the break room, to illustrate how far apart to remain
- Limit face-to-face contact by using e-mail, web meetings, teleconferences, etc.
- Cancel or reschedule large meetings and gatherings or host via teleconference or webcast
- Stagger start/stop times for employee break and lunch periods to reduce the number of employees in an area at one time
- Designate seating locations for lunch, breaks, and meetings so that individuals are at least 6 feet (2 meters) apart
- Prohibit, restrict or control visitors and contractors from entering your facility
- Add temporary barriers between workstations that cannot be physically moved
- Enable contactless hand-off of paperwork, such as drop boxes or trays
- Adjust shift times to reduce congestion at time clock stations
- Limit the number of people who can be in the facility or any one space at a given time
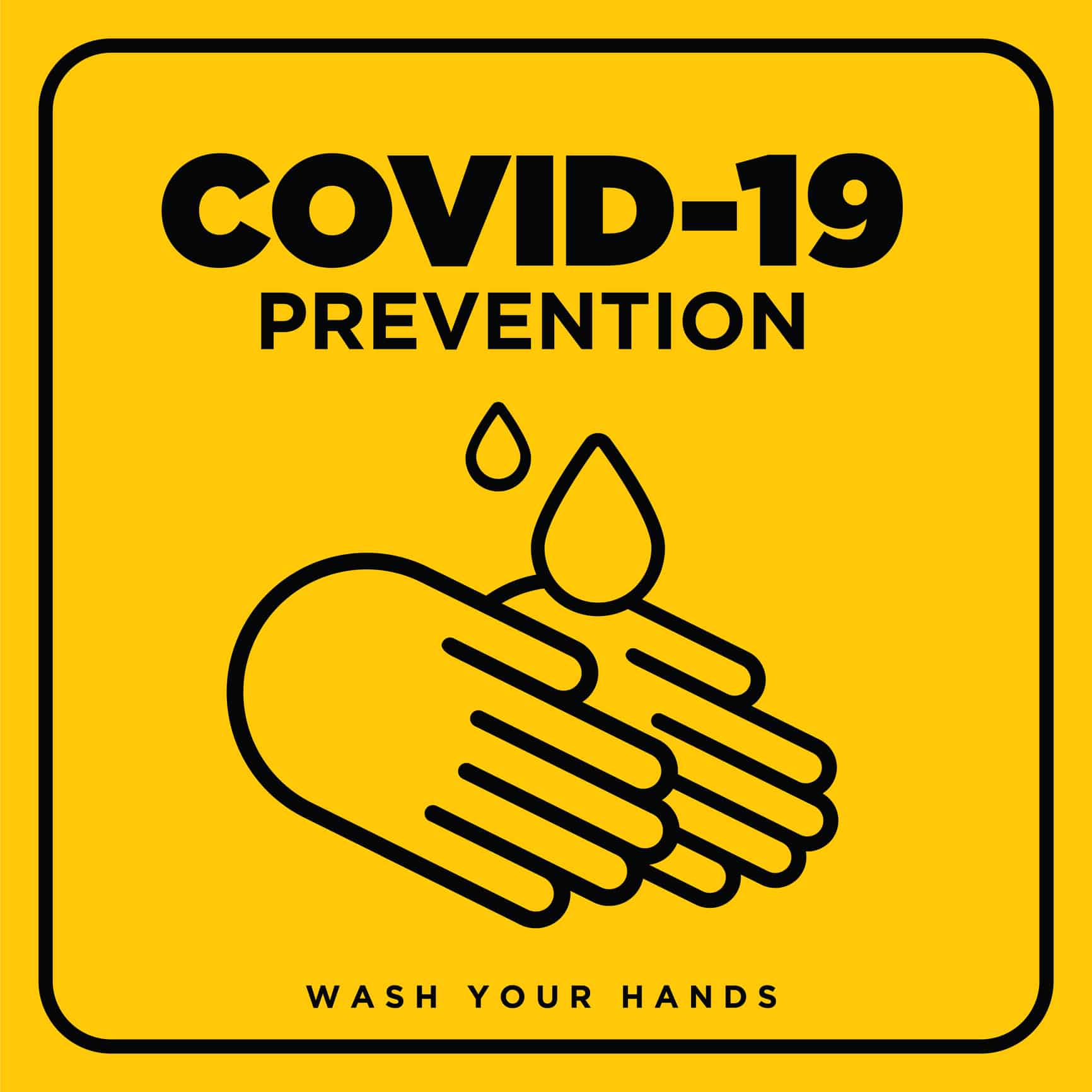
Cleaning and disinfection: Ensure you, your team, and your facility’s maintenance staff is properly disinfecting commonly touched surfaces such as doorknobs, tables, shared workstations, etc. with an EPA-approved disinfectant.
Hand-washing etiquette: Encourage frequent hand washing. Provide hand sanitizer to use when hand washing stations are not available to use between hand washing.
Symptom Screening: Pre-screen all contractors and visitors before entry into the facility. Employees should be screened before returning to work from leaves, vacations or holidays. Anyone that may have COVID-19 symptoms, potentially exposed to a person who currently is infected, or has been in an area of concern should not be allowed in the facility until they produce a negative test.
- Consider temperature monitoring before entry into the facility. Be sure that the method used to measure temperature is contactless
- Employees who develop symptoms or test positive for COVID-19 should not be allowed in the facility until they have quarantined as required by the CDC
- When you are notified an employee has tested positive for COVID-19, make a conscious effort to conduct “contact tracing” and identify co-workers who have had close contact with the infected individual
Proper PPE: Many states and communities have made it mandatory to wear masks in public. the Centers for Disease Control states that masks may help prevent the spread of COVID-19. Whether you decide to make it mandatory at your plant or not, providing your employees with masks and other sources of PPE and sanitation supplies is a simple way to ensure they’re protected throughout the workday.
For more information on manufacturing safety best practices and how ATS can help support your plant during these unpredictable times, contact us today.