Often discussed as a major part of the future of predictive maintenance and manufacturing technology, machine learning is one of the most valuable tools at manufacturers’ disposal today — and yet, remains misunderstood and underutilized. As machine learning becomes more commonplace, however — and more familiar — manufacturers can gain ever-increasing benefits, especially in predictive maintenance.
What is machine learning? It is a form of artificial intelligence in which existing data and conditions are used by a computer algorithm to “learn” and, thus, make predictions about future events, based on previous ones. Machine learning is unique in that the algorithm uses the data that is fed into it to model increasingly sophisticated predictions, without the programming of the algorithm changing. With the vast amount of data that can be collected by the technology used to enable predictive maintenance, machine learning holds great potential to offer massive benefits in this area.
What is machine learning?
Machine learning (ML) is an advanced form of artificial intelligence that relies on complex computer programming. At its core, however, ML relies on two primary factors to work:
1. Data
2. An algorithm
Data for machine learning comes in two main forms: historical data and continuous data collection (almost always collected by industrial sensors). Historical data is used to essentially get the algorithm up and running, and to begin its “training” to generate predictive models and increase accuracy. Continuous data improves the accuracy of the model in the form of more information. The algorithm is created to collect, process, and analyze data — essentially, to make sense of the massive amount of information available and to separate “signals” (salient data points) from “noise” (data points that are irrelevant to a predictive model). For data to be useful and for the algorithm to operate effectively, data must be “clean.” It must be organized, and it must be properly “described” for the algorithm to know what to do with it.
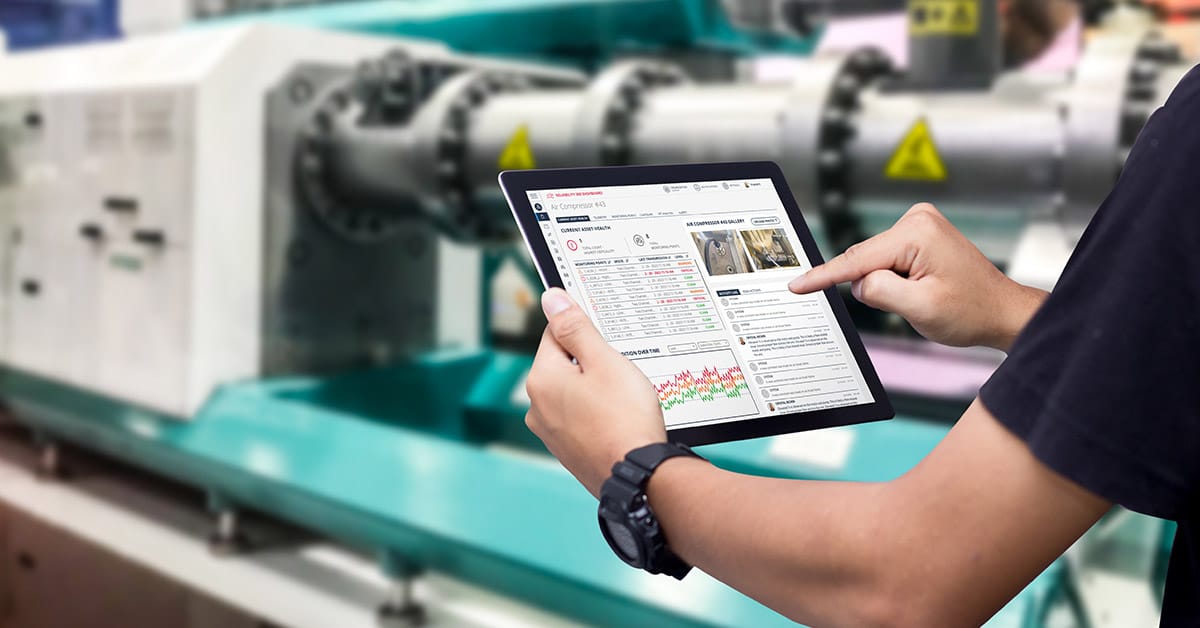
For example, a collection of machine temperature condition data points by itself is not that useful — even if the data covers a period of time including standard operation along with breakdowns. The data must be associated with the events in question, so that the algorithm “knows” that a certain data point means “operating as expected” or “breakdown imminent” (or “breakdown in progress,” etc.). With data and an algorithm, various types of modeling for machine predictive maintenance are possible. The main model types are:
- Classification modeling: Providing a Boolean (“yes” or “no”) answer, classification modeling is useful because it can generate a result with less data. In general, classification modeling is used to predict whether a machine will break down or remain operational during a given period. In predictive maintenance scenarios, this period will generally be short — perhaps a few hours from the present, or a day or two. This allows maintenance personnel to know whether they should plan repairs soon.
- Regression modeling: Regression modeling is more complex and is used to predict “remaining useful life” (RUL) — the time remaining until the next failure. Regression modeling typically requires a larger data set with more failure events included (and properly identified) — but once this data is available, the ability to predict RUL is incredibly useful, allowing for more accurate maintenance planning and other benefits as well (described in greater detail in the following section).
Types of machine learning
In general, there are four types of machine learning: supervised, unsupervised, semi-supervised, and reinforcement. All four have pros and cons.
Supervised
With supervised machine learning, there is a direct connection between the machine and the “proctor”. This is done by feeding the algorithm a number of input and output pairings or by showing the machine the type of connection you’re trying to make.
If you were building a model that predicted major machine malfunctions, you might feed in thermal data right before an event, followed by the event. This shows the algorithm how to connect the dots on its own, after enough supervision.
Unsupervised
Unsupervised machine learning is a great option if you’re looking for subtle patterns, such as grouping your inventory based on the runtime and yield of your machines. The data is fed into the algorithm with no sorting or filtering. Then the algorithm takes over and starts finding connections based on some rough parameters that you set.
Semi-supervised
Semi-supervised machine learning is somewhere in between supervised and unsupervised. You might show the algorithm what sorts of patterns you’re looking for, but you will still feed unfiltered data into the machine and allow it to create its own connections.
Reinforcement
With reinforcement learning, the machine learns similarly to a human. As the algorithm is creating connections and predicting outcomes, it is either punished for an incorrect prediction or rewarded for a correct one. Over time, the algorithm will fine-tune its ability to predict and understand the output of a given input.
Creating a machine learning model for predictive maintenance
Knowing how machine learning works is great, but how are you supposed to implement an ML program into your operation? Here are some distinct ways to create and introduce a machine learning predictive maintenance model.
Conceptualize and build the ML model
With any ML predictive maintenance, it begins with building and conceptualizing the actual model. This involves brainstorming what type of machine learning you’d like, what metrics you want to prioritize, and what type of data you’d like to provide the model.
As far as creation, most companies will outsource this work to a predictive maintenance services company. Trying to build an algorithm on your own could take years of trial and error, and it’s a massive undertaking.
Integrate existing and continued data collection
If your company already performs some level of data collection, you can leverage that. Plugging into existing workflows is a great way to optimize your machine learning for predictive maintenance, since there is a smaller upfront cost and time requirement.
Remember: The more meaningful data you can provide the machine learning model, the better your resulting predictive maintenance will be.
Identify the most critical data points
When you’re focusing on predictive maintenance using machine learning, a big part of your success revolves around knowing what to look for. Identifying the critical data points can give your algorithm better context for what pairings it should be making.
For instance, providing data from industrial monitoring sensors on your machines can give real-time insight into the health of your equipment. The algorithm can look at the data from these sensors, compare it to its database of provided data, and make more accurate predictions.
Execute and deploy the ML system
The final step is to officially deploy your ML system. It often takes some time for the ML algorithm to get up to speed and start making accurate predictions, so make sure you budget this time buffer in your timeline.
Applications of machine learning in predictive maintenance
Machine learning can be used in countless applications in an effort to predict maintenance requirements. Predictive maintenance machine learning is often used in industrial settings, checking for machine health and using real-time data to predict an upcoming failure.
Generally, machine learning can be used to spot a potential problem before you do. The data might suggest an upcoming failure event on the machine, so your maintenance team can service and repair the machine before an event that forces downtime.
How does an ML program make these predictions? Largely through industrial sensors installed on your machines. Simply looking at thermal or vibration data, for example, can give great insight into when you should maintain your machine to optimize production and minimize maintenance costs.
Benefits of machine learning and predictive maintenance
Predictive maintenance with machine learning offers a wealth of benefits, such as:
- Reduction in failures, downtime, and repair time: With predictive maintenance and machine learning, maintenance operations personnel gain unprecedented insight into equipment performance and expected future states, with a great degree of accuracy. This allows for maintenance planning to address issues before they lead to unexpected equipment failure, unplanned downtime, and inefficient emergency repairs. By preparing for maintenance and planning it for less disruptive times, numerous operational efficiencies are gained.
- Lower maintenance costs: Predictive maintenance with machine learning can reduce maintenance costs across the board, in several areas. Planning for maintenance means that parts can be located or procured as needed, without expensive emergency ordering. The right personnel can be scheduled, so that extra costs need not be incurred. Further, less downtime means increased productivity — reducing or eliminating one of the biggest resource wastes in manufacturing.
- Less spare parts inventory needed: Machine learning enables much more accurate inventory forecasting — especially with regression modeling involved. This allows for the inventory operation to keep fewer parts on hand at any given time since its need is now being predicted with much greater confidence. This enables a reduced inventory footprint and a more streamlined operation.
- More accuracy in maintenance planning: Overall, machine learning helps facilities accurately plan their maintenance needs in personnel, equipment operations, inventory, scheduling and more — resulting in more efficient use of all resources.
Predictive maintenance solutions with ATS
With over three decades of experience in industrial maintenance, ATS offers predictive maintenance solutions that rely on advanced manufacturing technology including sensors for machine health monitoring, and plant maintenance services. For more information, contact ATS today.