Whether your business is in a mature stage, is scaling up or is in the process of finding an industry foothold, one of your primary goals should always be on improving performance and productivity levels: week over week, month over month and year over year.
With a focus on ways to improve manufacturing productivity and efficiency, making a positive impact on your overall bottom line, the below practices can help your operations reach the next level in your journey of success.
1. Assess the current state of your operations
If your goal is to improve, it’s best to first know where you stand. Baseline data points for the current state of your operations will allow you to assess areas where you can improve the most, gain definitive insights into your progress, and get an accurate measure of ROI for the steps you take.
Some examples of metrics to assess include:
- Uptime
- Unplanned downtime
- Maintenance time
- Capacity efficiency
- Quality efficiency
- And anything else that’s important to you.
2. Review standard operating procedures with staff and update as needed
Having educated, well-trained employees is a key component of successful production processes. Even if your staff has been previously trained, re-training can help bring good practices back to the forefront and re-establish the importance of proper operation for safety, efficiency and quality purposes. In addition, be sure that your existing SOPs and training material are up to date with current operation best practices and safety measures. If they aren’t, be sure to make the necessary updates so your training and education materials are as useful as possible.
3. Focus on OEE
OEE (overall equipment effectiveness) is one of the most useful measures of operational performance. OEE comprises three factors:
- Machine uptime (calculated as actual operational time as a percentage of total available operational time)
- Performance efficiency (defined as actual output as a percentage of rated output — i.e., for parts per minute)
- Quality (defined as accepted parts as a percentage of all produced parts)
Multiply these three factors to arrive at a composite percentage that provides accurate insight into the overall efficiency and effectiveness of your equipment and operations.
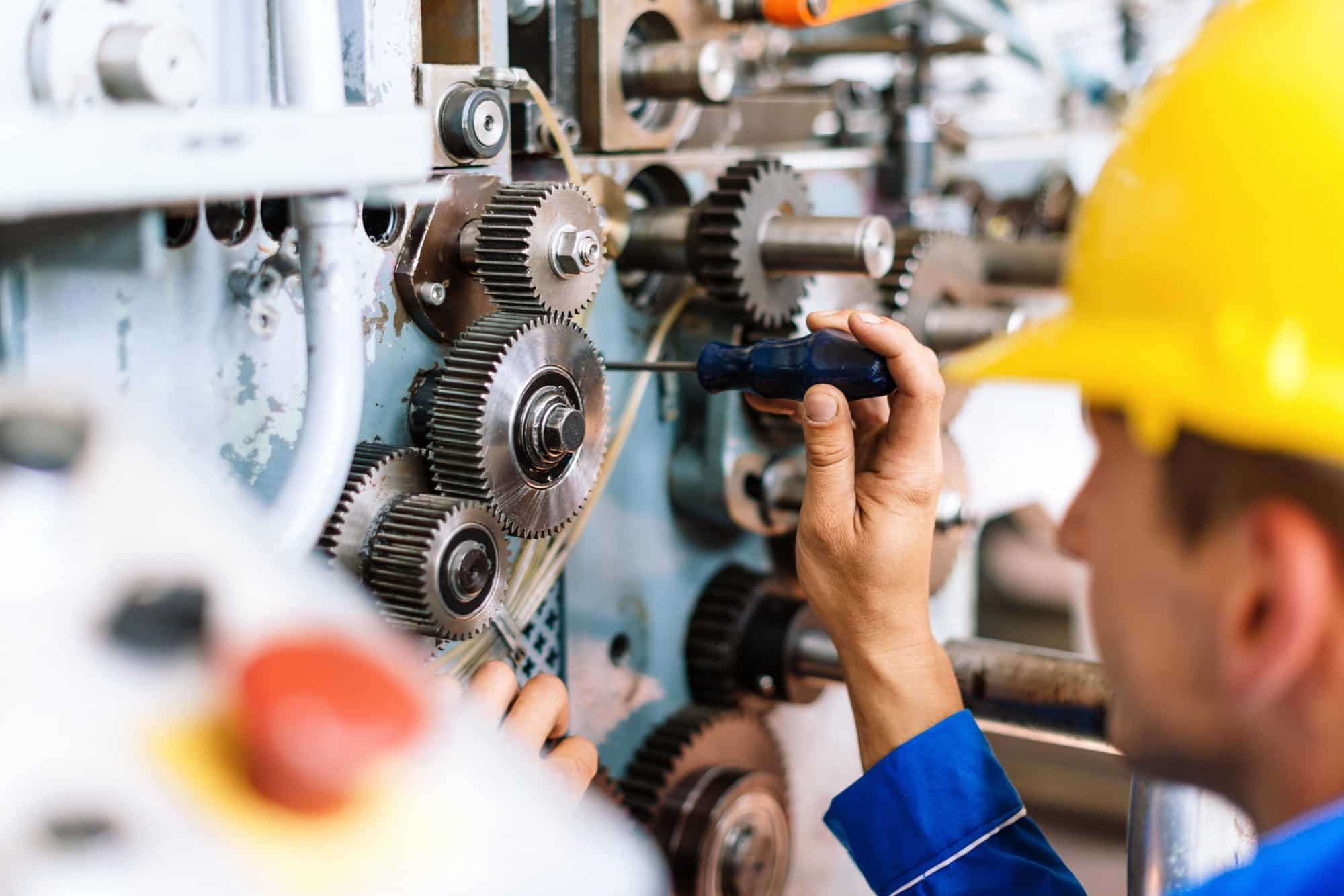
4. Recommit to maintenance
Equipment maintenance plays a vital role in every component of overall equipment effectiveness. Better maintenance means more uptime, improved machine performance, and a higher rate of part quality. In fact, one of the most effective steps you can take toward improving your OEE metrics is to focus on implementing a total productive maintenance (TPM) strategy.
Here are some maintenance points on which to focus your efforts:
- Rededicate efforts to preventive maintenance, confirming that all planned maintenance occurs on schedule.
- Ensure that maintenance staff is highly trained and educated to ensure they can complete tasks as efficiently as possible.
- Invest in other forms of maintenance, such as predictive maintenance, which uses data to identify potential maintenance issues before they cause unplanned downtime.
5. Investigate and invest in data
Data is a key driver of predictive maintenance. This maintenance practice is facilitated by a constant stream of real-time data from machine performance. However, in order to get this data, predictive maintenance does require an investment of updated equipment or aftermarket components. Fortunately, the investment in this updated technology repays itself quickly through vast improvements in maintenance efficiency and equipment operations.
Industrial sensors will typically be your primary method of data collection and monitoring. In most new equipment, sensors and communication technology are built in, while aftermarket sensors can be easily and relatively inexpensively purchased and installed on older equipment to gain the same benefits. These sensors drive improvement of manufacturing productivity and efficiency by shedding light on the underlying performance factors of equipment, which is the earliest indicator of potential issues that are likely to lead to maintenance needs in the near future.
6. Build around motivated talent — and provide the training to get there
Motivated equipment operators and maintenance personnel will almost always be your most successful and effective staff members. Be sure to support them by providing the training and education necessary to keep employees engaged and effective.
7. Consider outsourcing maintenance
Maintenance outsourcing is one of the most direct ways to supply your facility with highly trained maintenance professionals who are experts in the equipment and processes in use, as well as in the most up-to-date best practices to keep equipment operating at maximum effectiveness. An outsourced maintenance solution can help fill personnel vacancies or revitalize lacking maintenance processes, providing you with the confidence that your equipment is receiving the most advanced maintenance available — which in turn, allows you to focus on your core competencies.
8. Know the difference between manufacturing productivity vs. efficiency
As you focus on how to improve manufacturing productivity, it is important to understand the difference between productivity and efficiency – with each measure being important. Productivity is a measure of output quantity – how much your facility produces in a given time period. When you improve manufacturing productivity, you enable your business to deliver more to customers in the same amount of time.
Efficiency is a measure of production quality – in other words, how effectively resources are being used, and whether production potential is being maximized. When you improve manufacturing efficiency, your processes are operating exactly as they should be, and output is at or near the peak potential.
Advanced Technology Services offers outsourced maintenance and technical talent solutions that can help you make this year your most productive one yet. For more information about our services and how we can help you see productivity improvement in manufacturing industry applications, visit our website or contact an ATS maintenance specialist today.