Industry 4.0 impacts all aspects of manufacturing — from production processes to customer service to product quality. One of the greatest impacts, however, is on the workforce. This change in manufacturing technology coincides with the ongoing wave of baby boomer manufacturing workers reaching retirement age, causing rapid and significant changes to the future of work in manufacturing.
The technology underlying Industry 4.0 — industrial sensors, Internet of Things connectivity, digitalization in manufacturing, smart equipment and big data — unlocks massive potential for the manufacturing industry. Though to realize this potential, manufacturing workers must adapt, just as manufacturing organizations will need to adjust to provide their employees with the resources to succeed. This need for a new generation of skilled workers, who are comfortable with technology to drive efficiency and uptime like predictive maintenance, is one of the primary factors shaping the future of manufacturing jobs. In this piece, we will explore the impact of Industry 4.0 on manufacturing in greater depth.
Industry 4.0: How and why manufacturing workers and organizations must adapt
Here, we will cover three key areas: current challenges facing individuals and organizations; ways that organizations are using digital manufacturing technologies to address the skills gap; and the projected impact of this technology on manufacturing jobs.
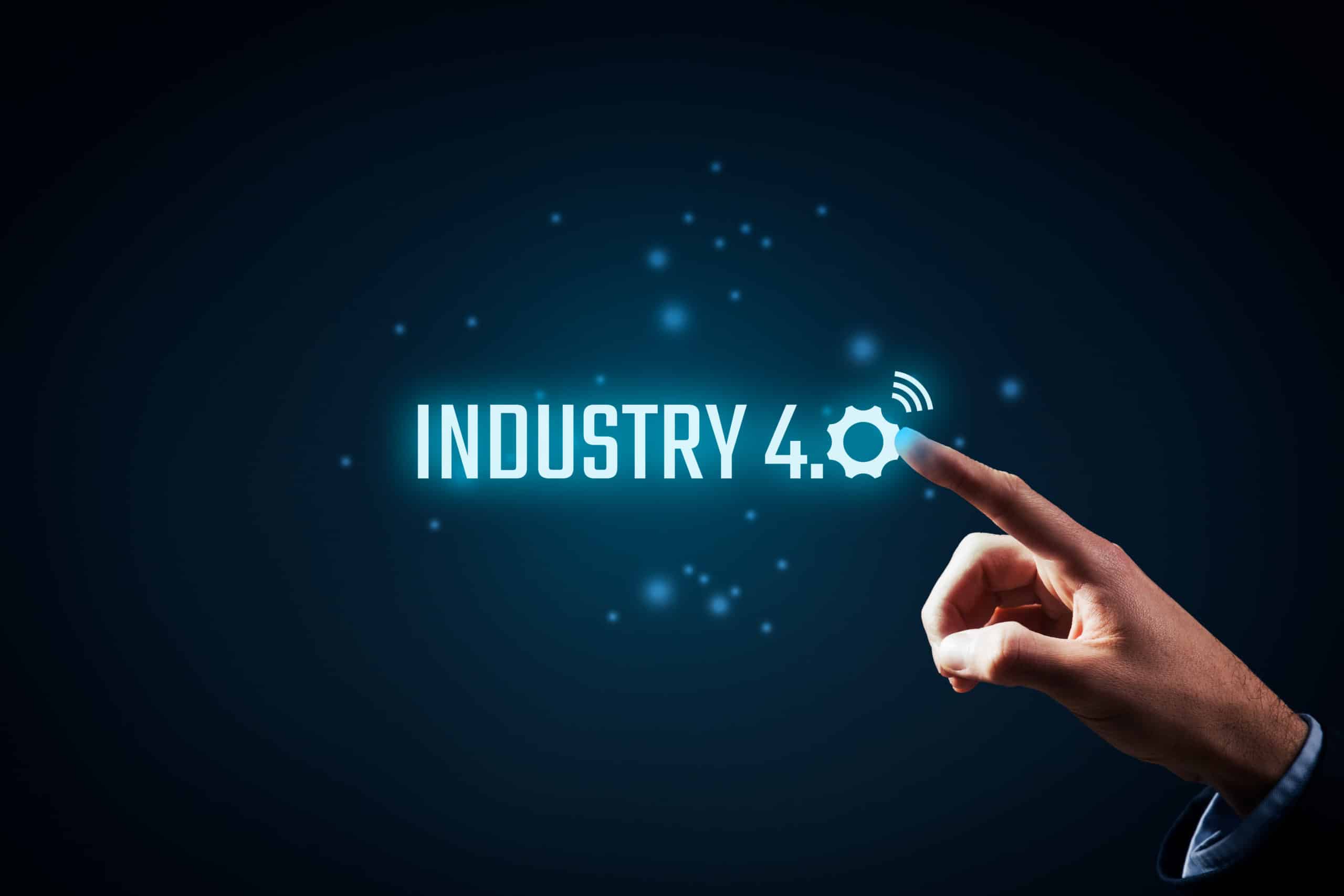
Skills gap in manufacturing
The skills gap remains a top challenge for manufacturing organizations, due to numerous reasons — new and old:
- Aging: Many of the baby boomers who filled manufacturing positions for decades — often at the same company — retired, with many more slated for retirement in the coming years. In fact, we can consider the current day to be almost the exact middle of the retirement wave for baby boomers, assuming retirement at age 65. As these key employees leave the manufacturing workforce, they take a wealth of accumulated knowledge and experience with them. It is difficult or impossible to directly replace this experience, so organizations must adjust.
- Negative misconceptions about manufacturing: Outdated and inaccurate assumptions about the manufacturing industry keep a foothold among many of those graduating high school and college — that manufacturing jobs are dirty, excessively dangerous, unfulfilling or low-paying. The industry must shed light on the inaccuracies of these assumptions to attract new talent.
- A shortage of qualified personnel for traditional positions: The above reasons mean that it remains incredibly difficult for manufacturers to fill open positions with qualified personnel. Those with the expertise required to fill positions are in high demand. It can be difficult for a company to retain personnel, even after investing in training and certification.
- A shortage of qualified personnel for technology-focused positions: A new wrinkle of the personnel shortage is that with digital technology becoming increasingly prevalent in the industry, legacy employees may not be willing to essentially change jobs and learn new technology, especially in the twilight of their career. Predictive maintenance technology and data analytics are the primary skills that these workers should hold – and manufacturers find it difficult to locate the right personnel. Combined with misconceptions among younger workers about a career in manufacturing, this means that the technology-intensive expertise necessary to facilitate Industry 4.0 technology is also difficult to fulfill.
Using digitalization to address the skills gap
Digitalization in manufacturing addresses the skills gap in several ways:
- Doing more with the same number of resources: As automation increases and evolves — and digital technology becomes more integrated with every aspect of manufacturing — personnel are able to monitor and control more processes. They won’t need to manually operate a machine, or even be in front of it. Digital technology enables personnel to massively boost productivity.
- Enabling remote work: Technology such as remote monitoring and control and digital twins enables more personnel to fulfill their job function remotely — which could be a mile from the facility, or across the country. Digitalization opens the talent pool from local personnel to anyone who will be able to log in, connect and do the job properly. As COVID normalized remote work for many younger workers, who now expect at least some flexibility to do their job from anywhere, this technology is one of the most promising ways to entice the next generation to upskill and pursue careers in manufacturing.
- Creating a more attractive career path: Digitalization is on the way to transforming the perception of manufacturing, shining a spotlight on the exciting and innovative engineering- and technology-focused aspects of today’s manufacturing career tracks.
What is the impact on manufacturing jobs?
All of the above factors mean that manufacturing jobs are changing. Just a few of the facets of this impact include:
- A need for cutting-edge technical ability: While expertise in traditional manufacturing processes remains important, manufacturing jobs will be increasingly technical. They will likely require — depending on the job — working knowledge or expertise in data analytics, programming and coding, systems architecture, database management, networking, and more.
- An expansion of worker (and job) availability: An expansion of worker (and job) availability: With more potential for remote work, personnel can broaden their potential job search to any connected manufacturer in the world. Likewise, the talent pool for companies grows massively.
- New definitions of productivity and innovation:
- New definitions of productivity and innovation: As technology assists with and enables more tasks to be fulfilled, workers will be increasingly relied upon to contribute in areas that machines can’t. Here are some examples:
- Identifying and developing ways of applying technology
- Improving operations
- Making the business more effective and successful
At ATS, we address workforce challenges through a variety of industrial maintenance solutions and technical training. Our services are based on decades of experience in reliability excellence — drawing on all of these areas to optimize operations and take businesses to the next level. Contact ATS for more information.