For operators of warehouses and distribution centers, 2020 was perhaps their busiest year on record. Valuing the convenience and safety of online shopping, purchasers spent more than ever on a growing variety of goods. This boom is prompting distribution center operators to evaluate options for automating tasks that are currently performed manually. At the same time, it’s spurring more innovation. Here’s a look at the future of automation in the warehousing industry.
The need for automation in distribution
Expectations for customer service have risen along with the volume of e-commerce transactions. Consumer and business buyers expect rapid delivery of whatever they purchase online, and this puts distribution centers under pressure. They are storing a larger number of SKU’s and performing more picks per hour than ever. They can’t afford any downtime that would delay deliveries, and they need an expanding workforce. People are one of the weak links in the modern distribution system; maintenance is the other. Industrial robots can’t yet match the flexibility and dexterity of human pickers, meaning these huge operations need large and increasing numbers of people to clock in and out each day.
Order picking is hard work. Pickers walk long distances, often carrying heavy totes or pushing carts. Unsurprisingly, labor turnover is high, and recruitment and training are significant expenses. Just as unsurprising, however, is that new technology — particularly robotics — is offering some solutions. Distribution centers already use highly sophisticated equipment such as shuttle systems and automated racking, but many operators seem eager to adopt more robotic manufacturing technologies. Already challenged to ensure 24/7 performance, this could only place greater demands on an already stretched maintenance team.
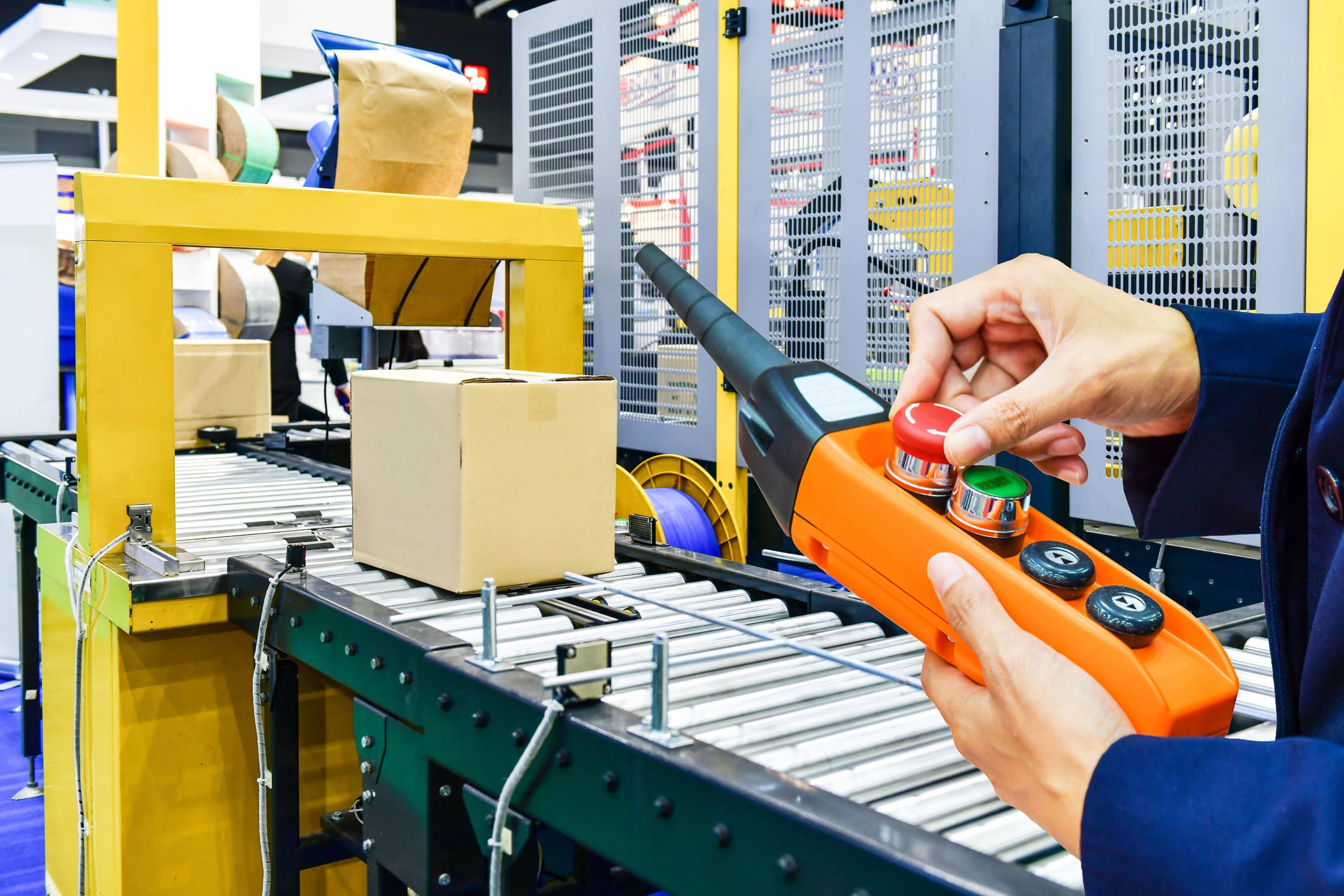
Harnessing innovations in industrial automation and robotics
- Order picking automation: Currently, there is no robot that is able to enter storage locations, retrieve the items needed and place them in a tote. Automation companies get closer to solving the robotic bin-picking challenge every year, but this remains largely beyond the limits of robots in factories. Will full robotic bin picking ever happen? One day, yes, but for distribution, it’s not quite there yet.
- Autonomous mobile robots (AMRs): AMRs are a step up from the well-proven autonomous guided vehicles (AGVs). Unlike AGVs, an AMR can navigate autonomously through a crowded and unpredictable environment. Expect to see armies of these deployed in support of the human pickers. One point to note: AMRs run on batteries. Future distribution centers will need to incorporate extensive recharging facilities!
- Augmented reality (AR): Order pickers are increasingly guided by pick-to-light and pick-to-voice systems. These tell the picker where to go and what to pick, in a sequence designed to minimize the time taken and distance walked. The next step may perhaps be AR, with smart goggles guiding the picker through the route and telling him or her what to pick.
Addressing the maintenance challenges
- Predictive maintenance: Parameters such as current draw, motor temperature and vibration are good indicators of machine condition. By monitoring these, it’s possible to spot trends that signal when servicing or repairs will be needed. Rather than take equipment out of service for overhaul on a time or usage basis — which may mean doing too much or too little maintenance — the predictive maintenance approach allows you to schedule work when it is most convenient for the distribution operation. Expect the future of warehouse automation to include huge numbers of machine health monitoring systems performing this role. They will feed data into an analytics system developed to optimize maintenance schedules in a way that minimizes operational disruptions.
- Skills shortages: As distribution centers adopt higher levels of automation and look to improve equipment availability, maintenance skills will come into sharper focus. AR has been proposed as one tool that may be useful for guiding technicians through complex repairs. Another approach might be to contract supplementary skills to fill workforce gaps as needed. In a similar vein, as increasing amounts of robotics technology find their way into distribution centers, maintenance stores will need to change to keep up. Again, many operators may find the most cost-effective approach is to contract both MRO storeroom management and MRO supply responsibilities.
Supporting demanding maintenance operations
It’s sometimes said that new technologies bring as many problems as they solve. For distribution center operators, the need to invest and upgrade their automation technology is evident; the difficulties of managing a human workforce may soon be insurmountable. However, automation — and robotics technology in particular — brings new maintenance challenges.
ATS offers an extensive range of maintenance solutions geared to the needs of modern factory and warehouse operators. These range from filling workforce skills gaps and handling storeroom management to implementing the advanced sensor and monitoring technologies needed for predictive maintenance. Learn more by contacting us today.