The time is now for manufacturers to start planning for their future. Technological advances, rapidly shifting market conditions, and an industry remaking itself in response to macro global trends mean that manufacturers’ very survival depends on their ability to adapt, innovate and endure.
Beyond the push for increased efficiency, manufacturers must focus on becoming quicker, smarter and greener in order to keep pace with competitors and remain viable in a volatile market landscape. While change is never easy, manufacturers’ ability to develop their strengths in these areas will be directly related to their ability to build sustainable, profitable long-term relationships with customers.
Trends shaping the future of manufacturing
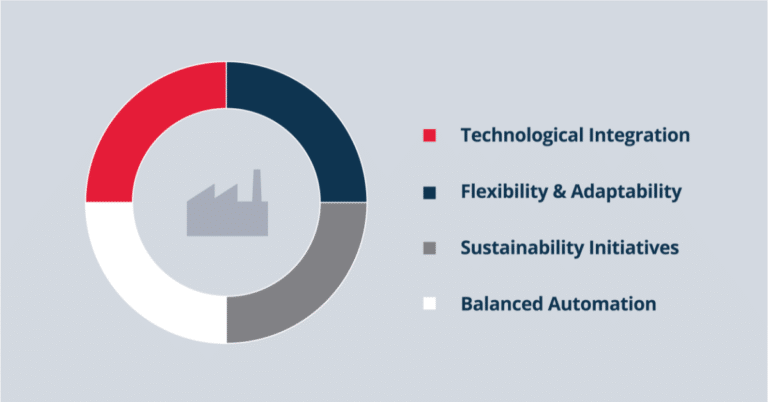
Four major trends are shaping the future of manufacturing — and they are already making an impact today. These trends are:
- Integrating digital technology with the production of physical products: While digital technology plays a major role in nearly every action we take and task that we fulfill, physical products remain the primary delivery system of this technology — a fact that is unlikely to change. The digital shift is an important concern for the future of the manufacturing industry, but manufacturers must continue to focus on excellence in physical production. They must also determine how best to integrate digital technology to support design, production, sales, fulfillment, service and more.’
- Supply chain and logistics adaptation due to the need for local, near and far manufacturing strategies: A purely offshore manufacturing strategy involves weeks-long lead times, thousands of miles of surface transportation, and — most importantly — wildly unpredictable scenarios in response to global sociopolitical trends, weather, material availability and more. This strategy is no longer viable or profitable. Trends and technologies such as microfactories, automation, on-demand production, and more are creating a new reality where local and onshore manufacturing can fit into the overall logistics puzzle along with offshore applications to maximize flexibility, resiliency and profitability.
- Increased focus on improved sustainability, decarbonization and electrification of production processes: Sustainability is an increasing concern for manufacturers, who are recognizing that changes can — and must — be made while continuing core processes and production capabilities. The shift to electric power has been gaining traction, and decarbonization technology is approaching the tipping point to more widespread adoption. Additional steps that manufacturers must take include supply chain analysis, further efficiency and material usage improvements, and an even greater focus on recycling, reuse and reclamation.
- Developing and maintaining an efficient “Automation Triangle”: The Automation Triangle consists of hardware, software and people — the key factors that remain necessary for manufacturing success. Hardware automation includes robots, cobots, autonomous vehicles and more, while software automation includes machine learning and artificial intelligence. Human workers remain a key component in the equation — even as manufacturing job requirements have changes, effective automation is impossible without skilled workers to program, monitor and analyze those processes.
Key factors powering the future of manufacturing
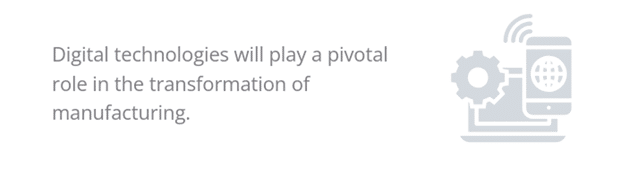
The future of the manufacturing industry is dependent on several factors being successfully adopted and implemented. These include:
- Integrating sensor technology: Industrial IoT sensor technology for manufacturing underlies many of the advances and processes described here. These sensors are the collection point for the data that drives advanced analytics, edge computing, automated decision-making and more. With costs continuing to drop for aftermarket sensors — and most new equipment arriving with integrated onboard sensors — this technology is quickly becoming the norm.
- Industrial robots & automation: Including cobots, drones, autonomous mobile robots (AMRs), automated guided vehicles and more, robot technology has reached new levels of collaboration as well as autonomy, enabling more precise and efficient automated work.
- Workforce satisfaction and safety: The skills gap remains a key concern for manufacturers, and the future of working in manufacturing must focus on talent retention as a foremost priority. With skilled workers more in demand than ever, employers must make a concerted effort to foster a supportive and safe workplace.
- Data processing, data distribution and data storage: Industrial sensors and other monitoring technology produce a massive amount of data that can be used to improve maintenance effectiveness and efficiency, thus reducing downtime and increasing productivity. The right tools must be in place to effectively collect, store, process, analyze and distribute this data.
- Using software/digital tools to control industrial workflows: Industrial processes must operate more efficiently than ever, and they can thanks to the data and analytics described above. The most effective way to put this data to use is to incorporate software, automation and digital controls into industrial workflows to enable real-time responsiveness and monitoring from anywhere.
- Advanced reporting methods that track progress and increase production data transparency and accountability: The large amounts of data that industrial sensors can collect enable reporting and analytics to reflect production efficiency and areas for improvement. It is critical to have the right tools and personnel on hand to make use of this data to drive accountability and continuous improvement.
- Utilizing AI/software to derive insights and make actionable decisions: Data scientists are just the first step in effective data usage. Massive gains are occurring by using AI and automation software to create actionable insights and automated decision-making.
What to expect in the future of manufacturing
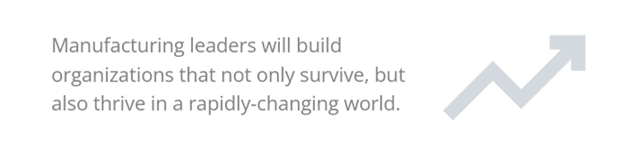
Among experts, the future of manufacturing is generally viewed in three major timeframes: short-term, medium-term and long-term. Concerns and expectations for each of these time periods include:
Short-term expectations & implementations (1-2 years)
- IoT investments, bringing all equipment and infrastructure up to date with sensors, edge computing capabilities and network communication
- Even greater use of 3D printing & additive manufacturing
- Focus on product recyclability and reclamation in connection with improved sustainability endeavors
- Extended reality, with real-and-virtual combined environments and human-machine interactions generated by computer technology
Medium-term strategies driven by data (5-10 years)
- As AI and ML technologies mature, responsible and practical usage standards will be codified
- A more flexible and adaptive supply chain in response to globalized issues, including geopolitical issues, climate and more
- Global emphasis on recyclable product manufacturing, led by Europe
- Improvement of digital twins and facilities
Long-term predictions (10+ years in the future)
- Robot technology and software will continue to advance; robots will complete tasks once reserved for humans, and fully automated “lights-out” factories will become more common
- Manufacturing — especially processes with the greatest environmental impact — could move off planet
- Off-planet resources for raw materials will be increasingly explored
With an understanding of these trends and technologies, you are ready to begin helping your facility and organization adapt to the future of manufacturing.