In the aerospace and defense industry, the need to embrace digital transformation is more important than ever. Why?
- Automation has taken new and innovative forms, driven by advanced technology
- Speed and efficiency, always a critical need for these industries, are in increased demand
- Supply chain uncertainty is a growing concern across industries
- In a global manufacturing landscape, cutting-edge digital capabilities are becoming the norm
In this post, we will look at practical applications of digital transformation in aerospace and defense companies, and will take a closer look at the benefits that digital technology can provide.
Applications of digital transformation for aerospace/defense manufacturers
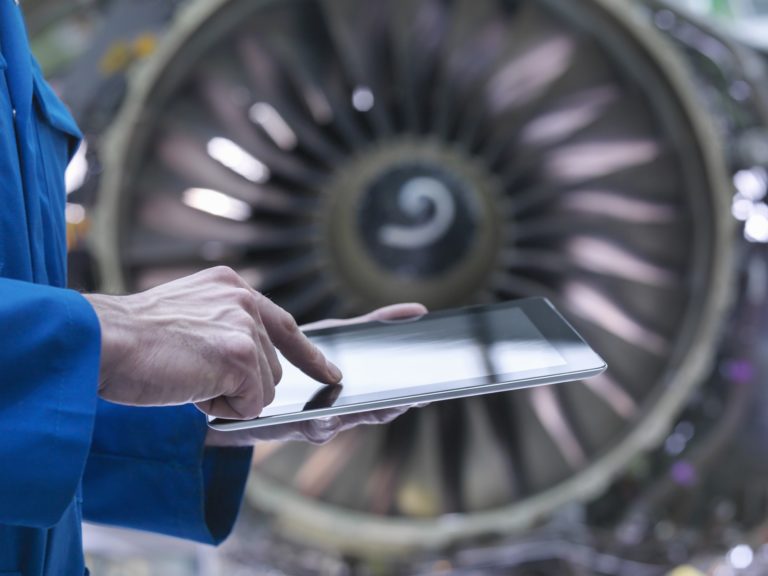
When we talk about digital transformation, we are covering many potential use cases — for example, Department of Defense (DOD) digital transformation as well as digital transformation at suppliers and contractors. Types of technology may include:
- Industrial sensors that track machine performance and potential quality issues
- Digital twin technology
- Digital threads
- Advanced automation technology
- Inventory monitors
- AI and machine learning technology
Each type of technology is a component of Industry 4.0, and Industry 4.0 in aerospace manufacturing and defense manufacturing goes hand in hand with digital transformation. The impact of Industry 4.0 on manufacturing cannot be overstated.
With the above technology implemented to create an aerospace smart factory or a defense smart factory, manufacturers can begin to explore potential use cases. These include:
- Improved maintenance through monitoring: Industrial sensors provide unprecedented insight into the performance and status of manufacturing equipment. With sensors installed, maintenance personnel can turn to methods like vibration monitoring and ultrasonic monitoring to detect the earliest signs of potential equipment malfunction. They can then schedule diagnostics and troubleshooting at a convenient time in the production schedule, rather than risking unplanned downtime as a result of equipment failure. Sensor technology facilitates predictive maintenance, the most efficient maintenance practice and a key factor in improving efficiency and reducing downtime.
- Global collaboration: Agencies like the DOD are increasingly expecting suppliers and contractors to be able to collaborate digitally from anywhere, a practice that is enabled thorough digital twin and digital thread technology. When a manufacturer is able to offer a digital twin, it not only enables them to work more effectively with other suppliers, but also it gives the agency a hands-on look at concepts and works in progress — a key way to drive innovation and speed in development.
- Supply chain efficiency and improvement: The supply chain remains a source of uncertainty and risk across the industrial sector. Digital transformation such as Air Force digital transformation helps manufacturers to account for and work around this uncertainty, in areas from improved inventory management to optimized supplier assessment. In addition, digital transformation in the form of tracking, as well as AI and machine learning technology, allows for more accurate forecasting, both in terms of inventory needs and in assessing macro global factors that have the potential to impact the supply chain. In a time where efficiency development and production are critical, there is very little latitude for supply chain delays and production overruns, making digital transformation a key concern in fulfilling contracts and meeting deadlines.
Benefits of digital transformation for aerospace/defense manufacturers
With the above applications and others in mind, we can now take a look at the direct benefits of digital transformation. They include:
- More efficient maintenance: With more efficient and effective maintenance, manufacturers can reduce downtime, maximize the value of every machine and ensure that maintenance is being carried out when and where it is needed — before unplanned shutdowns occur. While scheduled and preventive maintenance remain important, predictive, technology-driven maintenance provides the highest value per technician and machine.
- Improved adherence to production schedules: By maximizing equipment uptime and optimizing inventory management and supply chain, manufacturers exponentially increase their ability to provide accurate production timelines and to adhere to them. Unplanned events such as downtime or parts shortages are the primary reasons behind production delays, and digital transformation is a key method in overcoming these issues.
- More effective testing and collaboration: Digital twin and digital thread technology not only improves collaboration between facilities and suppliers — it also allows customers to test concepts and designs in real-time, from anywhere, in the most true-to-life format possible. This helps to improve communication while also driving innovation and helping to ensure that expectations are met.
- More cost-effective inventory and supply chain management: With improved forecasting and inventory management through sensors and AI, manufacturers are better able to control costs and offer favorable pricing or bids to potential customers.
ATS is a leading provider of technology-driven maintenance solutions for aerospace and defense manufacturers. We create value for our customers by optimizing reliability, processes and performance through data and technology. We are ready to help you enjoy the benefits that digital transformation offers, covering methods and practices including building a smart factory. To learn more, contact ATS today.