Golf Cart Manufacturer Saves $7M+
With Reliability 360® Machine Health Monitoring
Moving maintenance from reactive to predictive
Many manufacturers recognize the value of predictive maintenance, but turning that vision into reality can be challenging without the right expertise and support. By partnering with ATS, a leading golf cart manufacturer overcame these challenges and achieved measurable results, including:
Partnering for long-term success
At ATS, we don’t just deliver services, we embed reliability directly into your operations. When a leading golf cart manufacturer needed to protect their production equipment, they didn’t just need sensors, they needed a strategic partner. Our team worked hands-on at the customer’s plant, aligning our solutions with their unique operational goals and challenges.
From the initial consultation to ongoing support, we collaborated closely with their team to deliver clarity, confidence, and measurable results. Here’s how we work side-by-side with our customers to ensure success:
-
Tailored consultation
Our experts evaluate your operations and install the right sensor mix at the right monitoring points for maximum insights and ROI.
-
Expert analysis, not just alerts
Our experts cut through the noise, filtering alerts, analyzing anomalies and identifying potential failures that need addressed.
-
Clear, actionable guidance
When a potential failure is detected, we don’t just flag it, but deliver clear, actionable steps to fix it to keep your equipment running.
-
Ongoing support & learning hub
Access tutorials, resources and support anytime through our digital Knowledge Base, built to empower your team.
Preventing asset failure with condition monitoring
Using ATS Reliability 360® Machine Health Monitoring, critical vibration anomalies were detected in a dry-off oven bearing and a pump, well before failure. The data irregularity triggered an alert, which prompted the ATS condition monitoring experts (CME) to analyze the data. After analysis, the CME sent a recommendation to the maintenance team, enabling them to schedule repairs during planned downtime.
Through ATS sourcing and parts expertise, the on-site team was able to get the parts needed to repair the oven fan’s bearing and shaft, along with the pump and motor, without disrupting production. Post-repair diagnostics confirmed normalized vibration levels, validating the effectiveness of predictive maintenance in avoiding unplanned downtime.

Driving results with predictive maintenance
Combining remote condition monitoring with on-site expertise led to significant savings, surpassing $7 million in avoided production costs, while mitigating 240+ hours of potential downtime were successfully prevented, achieving zero production loss.
Oven savings
Pump savings
Hours in avoided downtime
Discover the power of Reliability 360® Machine Health Monitoring
Not all condition monitoring solutions are created equal. Learn more about the value Reliability 360® Machine Health Monitoring can bring to your operations below. Ready to get started? Contact us today.
What's included? | Reliability 360® Machine Health Monitoring | Alternatives |
Custom Installation & Plant Assessment | ||
Real-Time Continuous Equipment Monitoring | ||
Onboarding Program & Knowledge Base | ||
Analytics Dashboards & KPIs | ||
Customizable CMMS/ERP Integration | ||
US-Made Hardware & US Managed | ||
20+ Sensor Types | ||
Optional Maintenance & Parts Services | ||
Guaranteed ROI | ||
Explore resources
Get the latest insights, industry trends and manufacturing best practices from ATS experts.
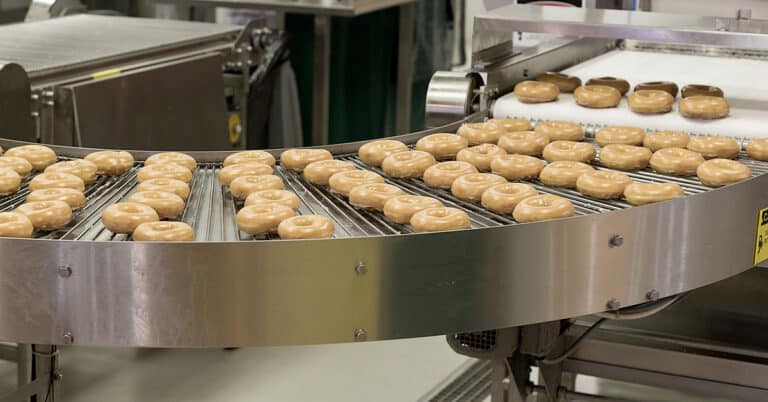
Case Study Infographic