As the manufacturing industry begins to look toward the future, it is clear that many of the changes that have occurred since the onset of the pandemic will stay. Along with the safety measures and limited production that will be required as people return to work, it is safe to say that the face of manufacturing has been permanently altered. While change can be difficult for an organization, there are several silver linings to this scenario. One is that adversity often sparks innovation and growth. The second is that manufacturing is accustomed to change.
Even before COVID-19, the industry had been experiencing some of the biggest advances in decades with the advent of IoT in manufacturing, or the Internet of Things. For many companies, the need to embrace industrial automation and other technology such as the IoT has been recognized. The coronavirus may have accelerated the pace of adoption, but even if businesses had not yet implemented these changes, many were likely to be thinking of doing so. IoT and manufacturing are poised to usher in the next phase of the industry, with a focus on safety, innovation and growth in the wake of COVID-19.
How IoT can be used in manufacturing
IoT in manufacturing can take many forms. Before examining applications for the Internet of Things in more detail, we’ll quickly define and examine the term.
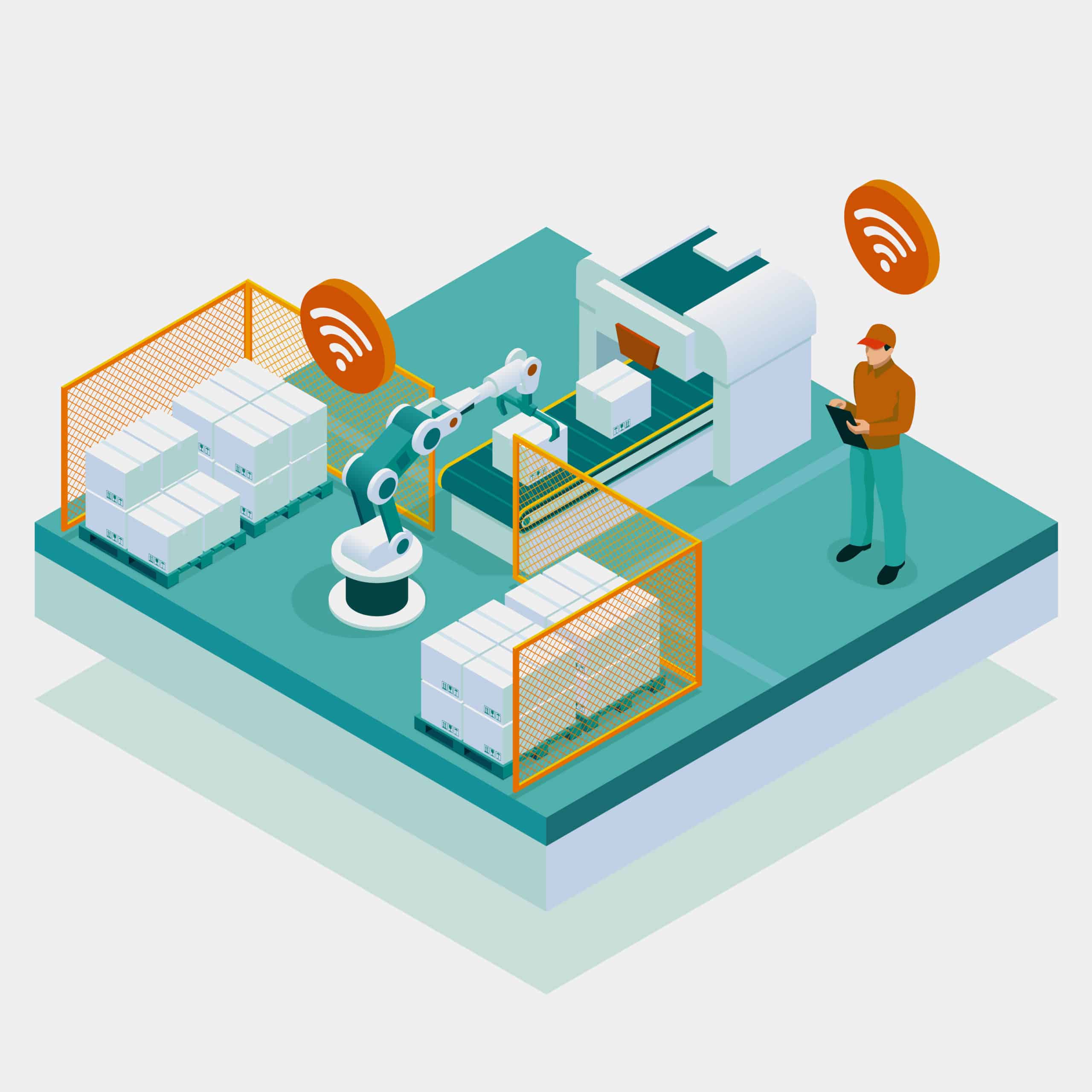
In short, the Internet of Things refers to the expansion of “smart” devices that are able to communicate with other gadgets, record data and respond more effectively to user needs. In consumer applications, one example is the smart car. Connected cars can accomplish simple tasks such as recording mileage or sending a notification when an oil change is due. However, this technology can also complete a job as complex as using an app to “tell” the vehicle to pick you up in front of a store. IoT in manufacturing can be used in several ways, all with the common themes of connectivity, data analysis and ease of access. IoT in manufacturing is increasingly important not only to remain competitive, but also to simplify operations while facility occupancy limits are in place.
Some applications include:
- Sensors and smart machines that monitor performance: The Internet of Things relies in part on bandwidth to track and record intricate aspects of equipment performance, typically through aftermarket sensors. By measuring factors such as vibration, temperature, ultrasonics and more, this equipment can detect potential issues in real-time, long before they affect production. This foresight affords plant leadership and maintenance personnel the power to schedule and plan for upkeep that would otherwise have been reactive.
- Remote monitoring: In the aftermath of the pandemic, manufacturers may have to adhere to capacity guidelines and operate with a possible restriction of allowed personnel in a facility at any given time, forcing organizations to assess who is truly essential to have on-site. Fortunately, the IoT facilitates remote monitoring, diagnostics and communication, so machine operators can be on-site while maintenance personnel can be on call. The insights that IoT technology provides also allow technicians to identify and address issues as if they were there.
- Increased automation: Automation is critical to keeping prices competitive and reshoring operations that otherwise might have been carried out overseas. IoT functions allow facilities to reap the cost benefits of industrial automation while continuing to offer jobs based on the implementation, programming, monitoring and optimization of these processes.
- Improved maintenance: IoT technology in manufacturing promotes predictive maintenance, creating more streamlined and effective support practices throughout an organization. The data and real-time control afforded through IoT technology are the keys to unlocking efficient, predictive maintenance.
ATS, IoT and industrial maintenance
At ATS, our comprehensive plant maintenance solutions are focused on delivering the best results, with IoT at the core. With decades of experience, we have developed expertise in implementing the right predictive maintenance solution for virtually any application. For more information about our industrial maintenance services, contact a rep today.