Reactive maintenance is one of three primary maintenance approaches typically employed in a manufacturing facility (the other two being preventive maintenance and predictive maintenance). Here, we will examine the types of reactive maintenance, when they may be appropriate to use and how other types of maintenance can provide more effective and efficient results.
What is reactive maintenance?
Reactive maintenance is maintenance that occurs in direct response to equipment failure or breakdown or in response to observation of an issue leading to impending failure. Due to the nature of how a reactive maintenance strategy is carried out, it often occurs on an “emergency” basis, with immediate or near-term action required in order to bring equipment back online and continue production.
Advantages of reactive maintenance
In the scheme of maintenance strategies, there are very few, if any, true “advantages” to a pure reactive maintenance strategy. The most direct benefits — and the reasons that a facility might rely on reactive maintenance over other approaches — are that reactive maintenance has lower short-term costs, namely lower up-front investment and fewer personnel required to carry out maintenance.
The disadvantages of reactive maintenance, however, are many, and are especially clear cut because they are in direct opposition to the so-called advantages described above. For example, the short-term cost “benefits” of reactive maintenance only refer to the immediate staffing and capital investment needs. Those benefits quickly dissipate when confronted with the costs of lost production time, emergency parts ordering, long-term equipment damage from operating to failure and more.
Preventive and predictive maintenance are better able to prevent and reduce equipment breakdowns, resulting in lower long-term, overall costs — the true bottom line that manufacturers should be looking at. With predictive maintenance in particular, manufacturers are better able to target and schedule maintenance exactly when it is needed.
Disadvantages of reactive maintenance
As described above, there are numerous disadvantages to relying on reactive maintenance as the primary strategy for a manufacturer. These disadvantages include:
- Safety issues: When equipment is allowed to run to failure, it is often operating in a dangerous manner in the time before the full breakdown occurs. In addition, major maintenance events require more risky repairs than the relatively smaller maintenance jobs that are typically enacted because of predictive maintenance.
- Increased costs: The short-term cost “savings” of reactive maintenance are no match for the long-term costs of frequent major maintenance events. Increased equipment wear and tear, and the need to order emergency parts and call in emergency personnel to resolve equipment failures quickly add up.
- Reduced asset lifecycle: As manufacturing machinery approaches a full failure state, it begins to operate far out of spec, increasing the risk of catastrophic damage to parts and components and accelerating the rate of wear and tear far beyond that considered normal. All of this adds up to a shorter equipment lifespan and more frequent major investments in replacement machines.
- Process inefficiencies: Reactive maintenance is the most inefficient approach out of all the maintenance strategies available to a manufacturer. Beyond the lost productivity once equipment breaks down, equipment that is allowed to run to failure will produce a higher rate of discards and will likely require more frequent maintenance even after repairs occur.
- Unexpected downtime: Downtime is one of the biggest resource drains for a manufacturer, resulting in lost production time and additional personnel requirements. In short, any time a machine is not actively producing value for the facility (and the customer), it is instead costing money. Downtime, especially unplanned downtime, is the most egregious example of this tenet, with every minute of lost production representing a tangible loss of value.
- Increased energy consumption: Equipment that is operating out of spec — leading to failure — is equipment that is operating inefficiently in terms of energy usage. Manufacturing equipment is closely calibrated to produce maximum output with the minimum possible energy use since this component of overhead is often a significant expense. The longer that equipment is allowed to approach a failure stage, the less efficiently it will run.
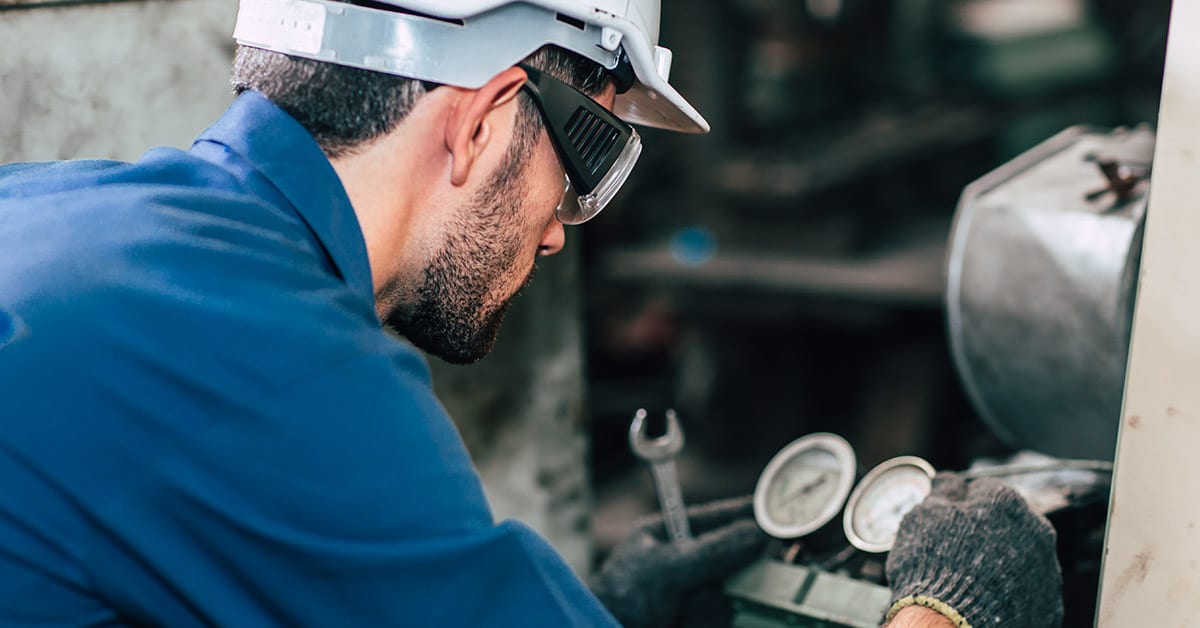
Types of reactive maintenance
With all of the above disadvantages in mind, it remains true that almost no facility will never require reactive maintenance. The purpose of outlining these downsides is to illuminate the need for other, more efficient forms of maintenance to take hold as the primary strategy for a facility. Types of reactive maintenance that may occur include:
Corrective Maintenance: Corrective maintenance occurs when an operator, technician or other personnel notices an impending failure scenario (either through inspection, observation or other maintenance). Corrective maintenance occurs before equipment failure, but given that it is initiated by a detectable problem with equipment operation, it is still likely to result in unplanned downtime.
Emergency Maintenance: Emergency maintenance occurs when equipment breaks down as a result of a maintenance need such as a failed component. Emergency maintenance not only leads to extensive unplanned downtime, but also may require the use of emergency technicians.
Reactive maintenance vs. proactive maintenance
The biggest difference between proactive and reactive maintenance is that the latter waits for downtime due to equipment failure. Reactive strategies leave manufacturers scrambling to handle emergencies before they take a serious bite out of productivity. On the other hand, the proactive approach watches out for early warning signs of trouble and takes care of them before they have an opportunity to cause breakdowns. This means equipment remains online for as long as possible, preventing interruptions in workflow. For reactive maintenance, the focus is on reacting to equipment issues as they occur, while proactive maintenance focuses on preventing such problems from happening in the first place.
Examples of reactive maintenance
There are plenty of real-world examples of reactive maintenance being put into practice. For instance, any time utility crews work to restore power after a storm damages power lines can be considered a form of reactive maintenance. Fixing a leaky faucet or other plumbing fixture is another example you can find around the home. Replacing a dead battery in a car that won’t start also is a reactive approach to automotive care. In many cases, these problems could have been avoided in the first place as long as the owner or operator took the time to inspect their equipment and correct any flaws they might have found. For issues that require relatively minor intervention, however, a reactive approach can be sufficient.
With this understanding of reactive maintenance, it should now be clear that more proactive approaches like preventive maintenance and predictive maintenance are the superior strategies for cost savings and productivity improvements. Contact ATS to help you on your journey of technology-driven industrial maintenance.