In the ongoing pursuit of increased efficiency and improved profit margins, lean manufacturing is one of the most impactful practices that organizations have adopted over the past several decades – and its influence remains significant to this day. Originally developed in post-World War II Japan as American thought leaders brought ideas about improving efficiency to Japanese manufacturing operations, today the principles of lean have been adopted around the world.
Lean manufacturing is defined as a set of methods focused on eliminating waste in production and all related processes. To further explain Kaizen lean manufacturing (as it is also known), we can define “waste” as any process or action that does not add value for the customer. Lean thinking is used to streamline production by rooting out these unnecessary actions and essentially stripping the production process down to only those elements that result in a successful product.
With this set of baseline definitions established, we can now take a more in-depth look at lean manufacturing uses, concepts, practices and principles. Implementing lean manufacturing principles can help your operations become more efficient and help drive continuous improvement efforts throughout your operations. Because lean thinking is always looking for new ways to reduce waste, it may be the best way to gain and maintain a competitive edge in the marketplace.
Lean manufacturing practices and techniques
The primary lean manufacturing benefits come from a well-defined set of tasks and actions, with the core tenet of waste elimination underpinning them. Lean manufacturing applications and methods include:
- Being proactive: Reactive practices, such as reactive maintenance, are among the most wasteful in a facility. In the reactive maintenance example, unplanned shutdowns mean that machines sit idle for an indeterminate amount of time and therefore not producing products – or value – for the customer. Lean manufacturing maintenance would define proactive processes like scheduled maintenance and predictive maintenance (achieved through R360® Machine Health Monitoring, including industrial sensors and internal network monitoring and communication devices) as the most efficient and least wasteful methods.
- Planning and scheduling: These practices are among the simplest and most effective ways to eliminate idle time and downtime, as well as to ensure that resources are being directed to the highest value areas possible. In lean manufacturing, underused resources are considered wasteful, so it is critical to ensure that personnel and equipment are being directed to the highest value tasks that they are capable of, at all times.
- Total productive maintenance: As a lean manufacturing maintenance process, total productive maintenance (TPM) focuses on the complete elimination of downtime, defects and workplace safety incidents – all of which create waste. TPM achieves this by placing responsibility and autonomy as close to equipment as possible, decentralizing decision-making and giving machine operators and maintenance personnel the latitude to carry out maintenance tasks as needed.
- Reliability-centered maintenance: Reliability-centered maintenance focuses on identifying and remedying failure modes for equipment and processes, using a rigorous process loop based on measured outcomes of maintenance decisions.
- 5S process: The 5S process is a core component of lean manufacturing, and we will explore 5S in greater depth later in this piece. 5S outlines five foundational principles of lean manufacturing.
- Kaizen events: Kaizen events are highly targeted procedures that focus on analyzing and improving a specific process in the facility. A Kaizen event occurs for a defined amount of time – typically several days, but sometimes as little as a few hours – and is an “all-hands” scenario that brings together everyone involved in a process to identify what works and what doesn’t, and to make decisions moving forward that maximize efficiency and value while reducing or eliminating waste.
5S: The five principles of lean manufacturing
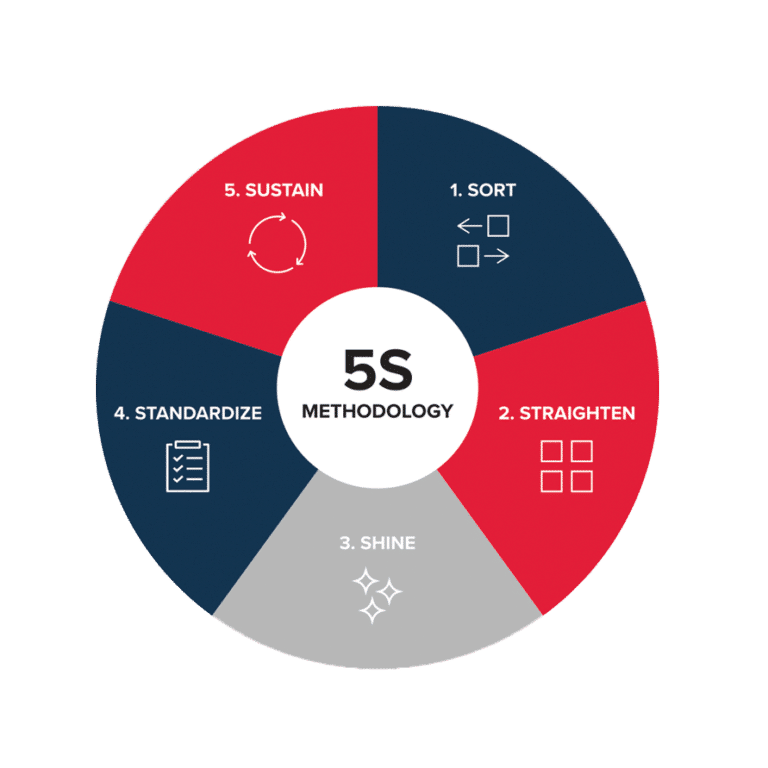
As mentioned above, these five principles of lean manufacturing provide the underpinning for the system and its related processes. With roots in Japan, both the original name and the English counterpart are listed below.
- Seiri: Sort: Sorting is an assessment of the items in a location, and the value that they provide. Any unnecessary items are reassigned to a value-producing location or are eliminated. Sorting makes operation, monitoring and inspection easier; makes it easier to locate required equipment and controls; eliminates safety hazards; and increases the amount of space available for value-added items or equipment.
- Seiton: Straighten: Straightening the workspace involves placing all equipment in an intuitive, orderly configuration to maximize efficiency and streamline processes. For example, seiton/straightening may involve moving machines so that the floor footprint reflects a logical process flow. It may also entail ensuring that the necessary supporting or secondary tooling is present at the workspace.
- Seiso: Shine & Scrub: As a maintenance baseline, the “shine and scrub” tenet focuses on workspace cleanliness as a method of supporting process efficiency and workplace safety. By carrying out daily cleaning tasks, machine operators and other personnel can help ensure that equipment does not encounter undue wear and tear, products are not damaged and personnel are not subject to safety hazards.
- Seiketsu: Standardize: By standardizing procedures and creating uniform processes, this step ensures that every worker knows exactly what to do and can be trained and supported in an efficient and uniform manner.
- Shitsuke: Systematize, Sustain: This step of the process calls for accountability and repeatability, entailing a system of monitoring and assessing the success of 5S and lean processes that have been implemented, and making decisions about how to modify or replace them as needed. This principle also includes training, education and audit of processes and procedures on a regular basis.
The role of continuous improvement in lean
Lean methodology has no predetermined endpoint. That is to say, the work is never done with regard to implementing lean throughout your organization. This is why a continuous improvement mindset is one of the most important elements of any lean manufacturing principle. Although typically considered a different philosophy, continuous improvement complements lean initiatives in such a way that many companies won’t use one without the other.
Because the continuous improvement philosophy involves always looking for new ways to improve, it can be the perfect framework for implementing lean tools. Continuous improvement thereby becomes the mechanism through which companies locate and identify areas that could be adjusted to lead to better results. Armed with that information, lean manufacturing practices then serves as a specific methodology for streamlining operations and delivering lasting process improvement.
Implementing Kaizen for ongoing enhancements
Kaizen is a Japanese business philosophy that shares a lot of commonalities with the idea of continuous improvement. One of the core elements of this approach is the idea that workers at all levels of the company share the responsibility for creating a culture that supports ongoing improvements. This makes Kaizen an important aspect of affecting lean transformation within any manufacturing operation.
Through Kaizen events, teams of employees across all levels of the company work together to isolate and resolve any issues that may exist within specific areas of the production process. Starting with a defined goal (i.e., increasing throughput on a specific machine by a predetermined percentage), the team uses tools like value stream mapping and histograms to identify inefficiencies or wasteful practices and develop solutions. These ideas are implemented immediately, ensuring that any process improvement takes effect as soon as possible to have the maximum impact on production.
Although Kaizen events can bring significant benefits including enhanced product quality and customer satisfaction, there are some hurdles that your organization may need to overcome in implementing them. In most cases, these challenges are culture-based, as many companies struggle to embrace Kaizen at all levels. This is why it is critical for leadership to commit to the lean manufacturing process. When dedication to the ideas starts at the top, there is a much greater chance of achieving buy-in at all levels.
Benefits of lean manufacturing
Implementing lean manufacturing practices throughout your production can be one of the best ways to ensure operational efficiency, which can have a cascading effect on quality and your company’s overall success. Among the many benefits of adopting a lean manufacturing system within your enterprise include:
- Higher product quality: The more complicated your processes are, the greater the chances that defects will occur. Adopting lean means you can streamline production and eliminate unnecessary steps, which ultimately means fewer defects and higher-quality products reaching the market.
- Lower operational costs: Every unneeded step in your production process costs you money. By using lean principles to root them out, you can cut down on your overhead and increase your profit margins.
- Less waste: From optimized inventory levels to lowered instances of downtime, a lean methodology can trim a significant number of wasteful practices from your operations and help you become more efficient. The less waste you have in your processes and procedures, the higher the return will be for you and your customers.
- Increased customer satisfaction: Streamlined production means higher-quality products. Less overhead means lower prices. Both add up to higher rates of customer satisfaction and greater levels of success for your business.
Challenges and misconceptions in lean manufacturing
Any lean principle must be implemented successfully if you want it to have the maximum impact on your operations. However, there are a number of challenges and misconceptions that can hinder your efforts. Among the many issues companies can have when adopting lean include:
- Incomplete implementation: Too many manufacturers see only the lean tools and try to use them without first building a culture of continuous improvement. This can lead to problems including less employee engagement and compromised results.
- Narrow focus: Looking at lean as a mechanism for achieving short-term gains means your efforts may be doomed to failure from the start. It’s important to keep in mind that lean is a journey that should be maintained over the long haul, rather than a quick fix.
- Lack of training: Your employees need to be onboarded successfully if you want to have success with any lean technique. Many manufacturers overlook the training and onboarding aspect of their lean transformation.
- Overlooking value for the customer: Lean can bring you significant cost savings by eliminating waste, but that shouldn’t be your only objective. Keep the customers in mind throughout your implementation and be mindful of how your decisions may impact them as well as you.
- Believing zero inventory is the goal: Although cutting down on excess inventory is one important goal of lean manufacturing, you shouldn’t be lulled into thinking you want to eliminate on-site inventory. As always, keep the customers in mind and make sure your decisions won’t lead to headaches for them.
- Overemphasizing cost-cutting: Lean is about more than increasing profit margins. It’s a holistic philosophy that should lead to improvements in all aspects of your business, including product quality and improved vendor relationships.
Lean manufacturing in the context of sustainability
As sustainability becomes a greater concern for many manufacturers, it’s easy to see how lean manufacturing practices can help them achieve their goals. Eliminating waste in all aspects of their production processes means fewer resources are consumed as well as fewer emissions being added to the environment. This has the dual-sided effect of reducing costs as well as enhancing the sustainability efforts for the manufacturer. From meeting ESG targets to enhancing company reputation among customers, the sustainable side of lean can be a true benefit for any manufacturer.
Easy to understand on its face but multi-faceted in its impact, lean manufacturing is one of the most critical philosophies for modern industry. Starting with the simple goal of reducing waste, lean expands in scope to encompass practically every aspect of manufacturing at all levels. Embracing lean may be the final step in helping your company unlock its true potential and gain the leadership position in the marketplace you’ve been striving to achieve.
With these core principles at your disposal, you now have the understanding necessary to start introducing lean manufacturing principles into your facility. At ATS, our lean maintenance helps improve facility efficiency, focusing on performance and value through reliability-centered maintenance and predictive maintenance. Our expertise in technology, systems, processes and personnel makes us the best choice for predictive analytics in manufacturing. To learn more, contact us today.