Debt. It’s something that most people try to avoid as much as possible. The long-term consequences are usually not worth the perceived immediate, short-term benefits. In the industrial sector, the practice of deferred maintenance can be thought of as incurring maintenance “debt.” Yet all too many facility owners and managers fall into the deferred maintenance trap, whether out of necessity or design.
What is deferred maintenance?
Deferred maintenance refers to the practice of putting maintenance issues into a backlog rather than addressing them in a timely manner.
A facility might choose this route for several reasons, all of which are resource-based:
- Lack of personnel: Manufacturers are all too familiar with the difficulties of maintaining a full maintenance staff. When short-handed, there are simply not enough technicians to address every issue as it arises. Thus, issues are placed into the backlog.
- Not enough parts or equipment: Whether through inventory management inefficiencies, storeroom mismanagement or inventory errors, it may be too difficult or impossible to locate the correct components or tools to complete a repair. When this is the case, issues are often placed into a backlog to be addressed at a later time, when the right equipment is on hand.
- Insufficient time: When under pressure to fulfill an order, any issue that does not directly cause a shutdown may erroneously be viewed as non-critical, and thus not worth the time to fix right away.
- Scarce budget: Maintenance budgets are almost always kept as low so facilities can focus on investments that are seen as more direct contributions to production. These budgets can be stretched thin prior to the end of the planning year. This leads to perceived non-critical repairs being backlogged in favor of anticipated critical repairs.
These are valid issues, and they often present a compelling argument for managers and owners to engage in deferred maintenance practices. As we will explore below, however, there are significant negative consequences to deferred maintenance. We’ll break down the consequences, and how you can avoid them.
The negative consequences of deferring maintenance
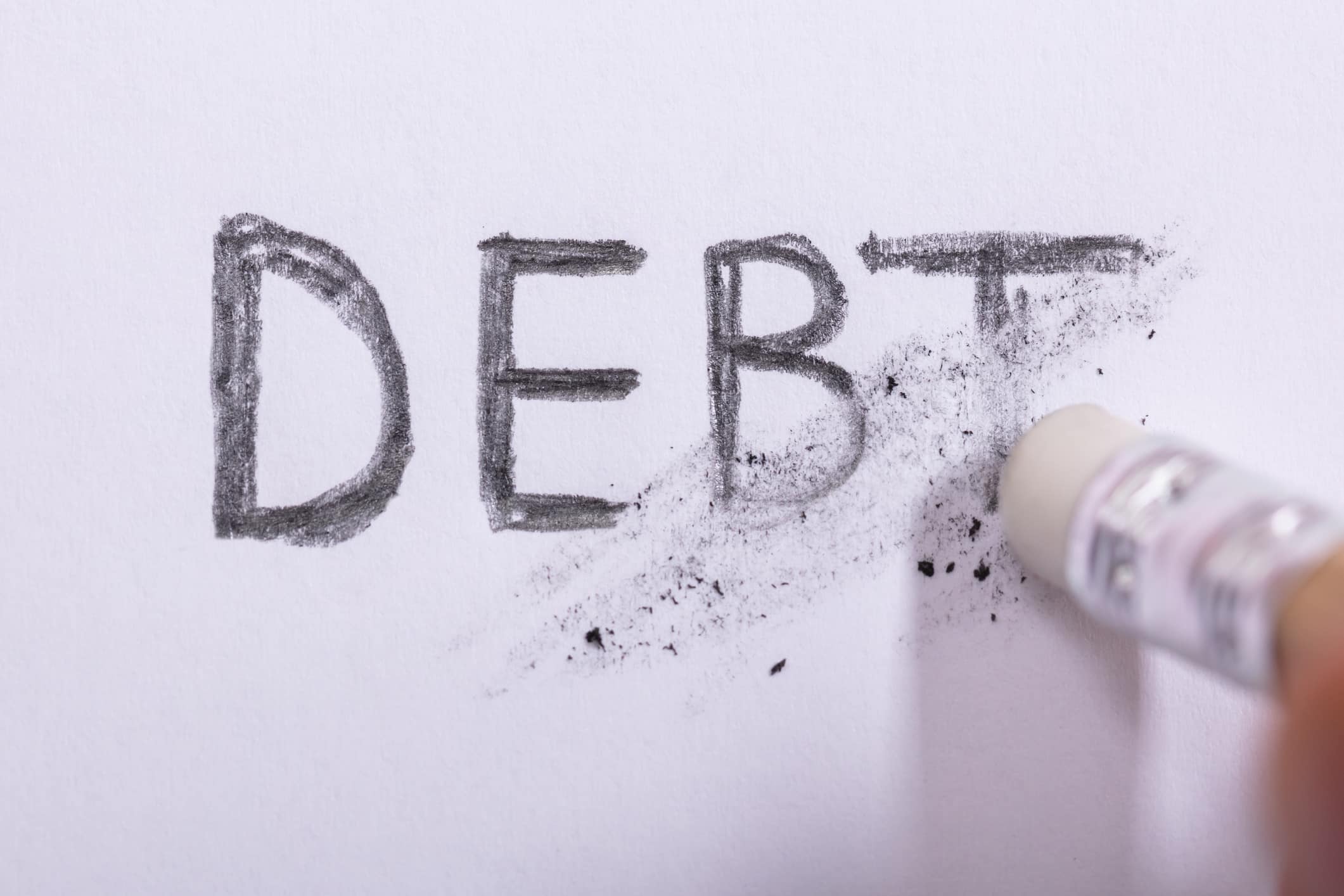
To best understand the overall effect of deferring maintenance, let’s revisit the initial “debt” analogy. Just like any other debt, you are delaying a current payment until the future with deferred maintenance, meaning that there must be some type of “premium” involved. In the case of deferred maintenance, this premium will not only have a financial impact, but can also affect many other aspects of operations.
The negative effects of deferring maintenance, or incurring “maintenance debt,” include:
- Potential damage to equipment and infrastructure: Whether it is planned or reactive maintenance that is deferred, equipment that is not running in optimal form is at risk of internal damage and accelerated wear and tear. If unmaintained equipment begins to leak or expel fumes, it can also damage other equipment as well as the facility infrastructure.
- Personnel safety risks: When machinery is not maintained as needed, it becomes dangerous to the operator as well as other staff in the area. Unmaintained equipment poses physical risks in the form of debris pile up, leaking fumes or fluids, and explosions.
- Inefficient operation: Equipment can only run at its rated capacity when it is properly maintained. Scheduled preventive maintenance is one way of keeping equipment running optimally. It comes as no surprise that equipment beginning to fail in one area must compensate in other areas to remain operational. This results in increased operating costs and slower output.
- Product defects: If equipment is not maintained for optimal operation, it will not be able to produce products as designed. Accuracy, tolerance and other key metrics could suffer, resulting in more part defects, increased rework or finishing work, and higher costs.
- Reduced equipment life: Equipment service life ratings are based on proper maintenance. When equipment is running sub-optimally, parts and components will likely fatigue more quickly, reducing the effective life of the machine.
- A recurring poor maintenance cycle: Much as debt accumulates interest, unaddressed maintenance issues will only lead to more serious problems. Especially in cases where resources are more limited, this can quickly create an insurmountable maintenance backlog.
- A never-ending backlog: While it can be easy to add a maintenance issue to the backlog and feel confident that it will eventually be addressed, this practice can quickly spiral out of control. The existence of a backlog indicates resourcing and efficiency issues, which are difficult to overcome once they are in place.
Avoiding and overcoming deferred maintenance issues
Fortunately, there are ways to address and avoid the practice of deferring maintenance, even in scenarios where resources are limited.
These methods include:
- Automation and sensors: Proactive monitoring via sensors can automate many maintenance practices and help identify issues well before they become critical. This will allow you to direct resources in the most efficient way possible, reduce downtime, and prevent unexpected delays and expenditures.
- Inventory monitoring and management: Sensors can also play a role in more efficient inventory management, reducing or eliminating the confusion and delays that come as a result of missing parts and inaccurate inventory tracking. In cases where an inventory backlog is necessary, there are ways to make it a more effective practice. For example, rigorous backlog prioritization may help keep issues from becoming critical and can ensure that equipment operates optimally under the circumstances.
ATS offers a multitude of plant maintenance solutions designed to help you avoid the pitfalls of deferred maintenance. Our staff of engineers, subject matter experts and experienced maintenance technicians are ready to help train your team; assist with short- or long-term maintenance issues in cost-effective ways; implement and manage more effective inventory practices; and more. Whether you are interested in one-off services or a comprehensive plan, we are ready to partner with you to implement what will work best. For more information, contact us today.