What is a contingency plan?
Not everything in the world of manufacturing goes as smoothly as it should. When breakdowns or interruptions in production occur, a rapid and coordinated response is crucial for getting things back on track. This is where having a contingency plan is essential. When manufacturers have a clearly defined course of action they can follow when they encounter an issue, they can resolve it as quickly and efficiently as possible.
The COVID-19 pandemic has shown that in manufacturing, as in all business, a contingency plan is a key to facing and working through such disruptive events. In manufacturing especially, maintenance contingency planning should be a major consideration since machinery and assets are critical components of all manufacturing operations. Below, we break down the importance of contingency planning in risk management, and provide the steps needed to create a successful maintenance contingency plan.
The benefits of maintenance contingency planning
A contingency plan gives manufacturers a proactive plan of action that can be immediately implemented once a crisis or disruption occurs. As opposed to a crisis management plan, which is more reactive, contingency planning is meant to trigger events, policies and processes that prevent disruption to the business as much as possible, even as external factors are disrupted. With a comprehensive contingency plan in place, manufacturers can realize several benefits:
- Proactive steps to get ahead of disruptions as much as possible
- Favorable pricing with the advantage of foresight against supply and demand fluctuations
- Access to alternative supply chain sources to keep raw material inventory stocked
- Uninterrupted maintenance, ensuring asset investments remain protected and functional
A contingency plan that enables a facility to continue operating core processes will see the benefits of remaining functional, but will also be able to handle order increases in times of increased demand – which may not be the case for those that did not prepare. Without a contingency plan that includes maintenance as a core piece, a manufacturing facility may encounter numerous issues, even if other pieces of the plan are in place. These may include:
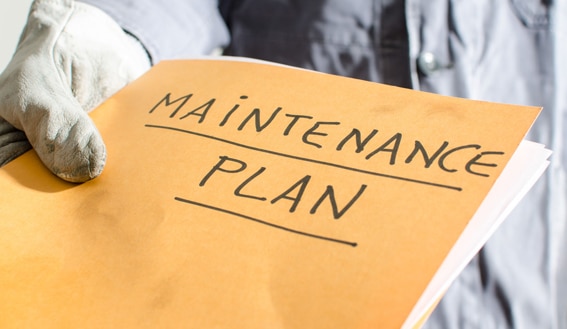
- Increased downtime and repair time if regularly scheduled maintenance is neglected
- Damage to machinery
- Defective or damaged parts
- Excessive lost production
- Increased maintenance costs for emergency repairs
- Loss of confidence and potential lost orders if production deadlines are missed
How to make a contingency plan
While every contingency plan should be tailored to the specifics of a facility’s operations, there are several general steps that can help get a contingency plan off the ground. These are:
- 1. List your key resources: Resources include equipment, people and inventory. Resources may also include tools, software, teams, proprietary processes and more. As you identify these resources, prioritize them so that you understand which resources are the most crucial to your operations.
- 2. Identify risk factors: What are the key risks that might impact your resources, and their ability to complete their functions as required? Some of these may not always be obvious, and some may seem far-fetched (much in the way that COVID-19 disruptions may have seemed unlikely at this time last year). Consider external consultants and maintenance experts to help you identify risks of which you may not be aware.
- 3. Analyze risks based on severity and likelihood: One of the most important elements of the contingency planning process is breaking down the risks and prioritizing them. Those that have the most potential to impact your productivity severely should be at the highest level. Additionally, those that are deemed the most likely to happen at any given time also should be a prominent part of your plans. This will ensure the greatest odds of success in the event of an incident.
- 4. Consider risk mitigation strategies: Setting contingency plans in an organization means choosing the most effective means of resolving any problems you might encounter. Once you’ve identified the most common and impactful issues you might face, it’s time to decide the most appropriate course of action for each.
- 5. Draft the plan: Using your top risk factors as a basis, create a contingency plan to address each risk. Remember that a contingency plan should be proactive, including tangible steps that can be initiated once a disruption or threat to your operations is identified.
- 6. Review and finalize your plan: Circulate the plan to those who would be impacted by risk factors and who would implement the plan. Solicit feedback to ensure that you have addressed their concerns and to learn whether the plan seems sound to them. Once the plan is satisfactory to all relevant personnel, finalize the plan, document it, and make sure it is known and available throughout your organization.
- 7. Test and monitor your plan: It isn’t enough to simply draft a plan — you need to make sure it will work when you need it to and keep it up to date. Any changes to your processes need to be taken into account and your plan adjusted as merited.
Maintenance contingency with ATS
Are you considering drafting a maintenance contingency plan for your manufacturing operations? As experts with over three decades of experience in the industrial maintenance field, ATS has a broad base of knowledge in the risk factors that can affect maintenance processes and manufacturing operations as a whole. Our short-term maintenance capabilities can effectively support your contingency plan while limiting downtime, reducing emergency repair costs, and filling gaps in maintenance personnel. For more information on how we can help with your maintenance contingency planning, contact us today.