Machine vision in manufacturing protects customers from defective products, enables automation and reduces costs. Machine vision systems need a limited amount of maintenance but can also be used to support maintenance. This blog explores the role of machine vision in manufacturing and considers its relationship to industrial maintenance.
What is machine vision?
Machine vision is the use of cameras and software to gather data, make decisions and control operations within a manufacturing environment. It’s the industrial application of computer vision, which is used in many everyday activities, from security systems to computer games and autonomous navigation.
Manufacturing vision systems comprise a camera, lighting and software for image acquisition and analysis. These components may be separate or combined into a single piece of hardware. Vision systems are almost always integrated with other production equipment such as PLCs. These take actions determined by the result of the image analysis, such as opening a reject gate on a conveyor or moving a robot.
How do machine vision systems work?
Until recently, industrial machine vision systems all followed the same principles, obeying a set of rules created by a programmer. The typical operating sequence for such a system is:
- Image capture: In response to a trigger signal from a part presence sensor or PLC, the camera captures a picture (usually referred to as an image). Consistent lighting eliminates any differences between images that would be hard for software to deal with.
- Image pre-processing: Software removes distortion and/or applies filters to improve contrast.
- Image analysis: A sequence of rules established by the programmer looks for features of interest like edges, 1 or 2-dimensional bar codes, characters or regions of uniform contrast. Additional rules may make measurements (which requires periodic calibration of the vision system).
- Result output: The computer program interprets the results of the analysis. This might be a dimension or position, a character string or a good/no good decision. The result is then sent to a PLC, robot or other computer.
A recent innovation in machine vision is the use of artificial intelligence (AI) to replace rules-based programs. These can remove the need for a programmer and, depending on how they are configured, can be taught to learn from their mistakes. However, they require an initial training period which sometimes needs hundreds, if not thousands, of pictures.
Types of machine vision
Vision systems in manufacturing operations take many different forms. Camera types comprise:
- Area scan: These cameras capture familiar square or rectangular pictures. They are the most widely used type. The pictures may be color, although monochrome images are more commonly used.
- Linescan: This is a camera that captures a single line. Multiple lines are then combined to create a typical rectangular picture. Like a photocopier, a linescan camera either scans over the surface being imaged or the surface moves. Linescan cameras are often used on continuous web processes like printing packaging material, rolling coil or weaving.
- Infrared: These work in the longer wavelength region of the spectrum that human eyes can’t see. This can be useful for avoiding glare, seeing through some packaging materials or eliminating the effect of color variation.
- Thermal imaging: These use sensors sensitive to the long wavelengths of electromagnetic radiation emitted by hot surfaces. In other words, they “see” heat. Thermal images are often colored to make hot regions appear red and cool areas blue.
Vision systems are also identified by their packaging or number of components. Definitions vary, but the generally agreed upon classifications are:
- Code readers: Handheld or fixed-mount devices, typically with integrated lighting, these decode 1 and 2D codes like Datamatrix and QR codes.
- Vision sensors: Often incorporating lighting, these are used for simple tasks such as verifying the presence or absence of a particular feature or component. Only slightly more complex than photoeyes, and with integrated processing capabilities, they are often embedded into industrial equipment.
- Smart cameras: Adding a processor and software to a camera makes it “smart” in that it takes a picture and outputs a result. Some smart cameras use an integrated light but it’s common to provide dedicated lighting. Smart cameras can make measurements and look for flaws. They can be complicated to program although most use graphical tools and menus. Some AI programs can be deployed via high-end smart cameras.
- Vision systems: Here, one or more cameras is connected to a dedicated processing box, often, but not necessarily, a PC. The processor has extensive computing capabilities and runs at high speed. These are used when images are large and/or are captured at high speed and need extensive processing. Unless running AI, they need a programmer comfortable working with advanced languages such as .NET and Python.
Machine vision applications
Unlike computer vision in manufacturing, which is used for tasks like autonomous robot navigation and augmented reality (AR), machine vision is used mainly for quality control and, to a lesser extent, for robot guidance. The main applications are:
- Reading characters and codes: Used for traceability
- Part or feature location: Instructs a robot where to go to pick up or place a part
- Part inspection: Making measurements, checking for missing components or looking for flaws such as dents and scratches
Benefits of machine vision in manufacturing & maintenance
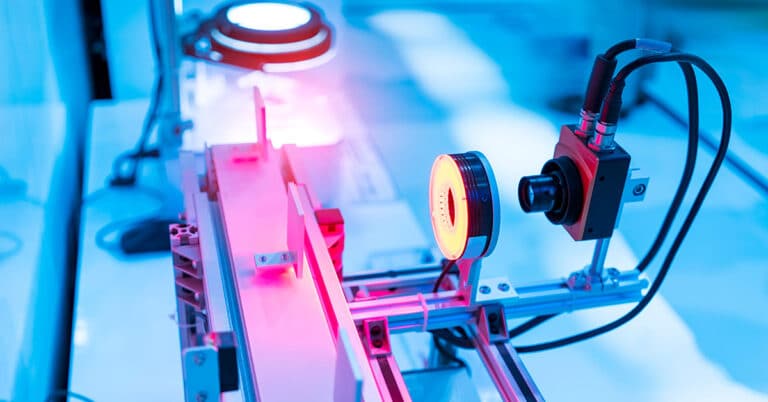
Unlike humans, machine vision systems don’t get bored or distracted, and they apply consistent standards. More specifically, they:
- Support automated equipment like robots
- Detect nonconforming product promptly — so the problem can be addressed before any more time and material is wasted and before it gets shipped to the customer — which avoids costly human inspection
- Gather data that can be used for traceability, quality improvement and process optimization
Up to now, while machine vision systems need some maintenance, (mainly cleaning of lights and lenses), they have not been used for maintenance. However, that appears to be changing. Current and proposed maintenance applications include:
- Thermal monitoring: Observe the temperature of electrical or mechanical devices such as transformers, control cabinets and bearings.
- Detecting machine condition problems: Analyze measurement and inspection data and raise a flag when a threshold is crossed.
- Measuring movement: Complex mechanical systems such as pumps and valves often have natural oscillations. This motion can be continuously measured and an alarm sounded when a threshold is exceeded.
In addition, AR headsets for maintenance technicians are an example of computer vision at work in servicing and repair.
Increasingly important for quality and maintenance
Machine vision is an increasingly important sensor technology in manufacturing. It’s used to reduce costs by detecting quality problems promptly and to support automation that further lowers costs and improves quality.
A developing aspect of machine vision is its potential to capture information about both the products being manufactured and the manufacturing processes. It’s in this regard that it will doubtless find many more uses as a maintenance tool, especially with its ability to generate data for predictive maintenance.