IT and OT convergence (information technology and operational technology convergence) is a topic that you may hear discussed more and more frequently, and for good reason. It goes hand in hand with the other major shifts occurring in manufacturing, such as connectivity, IIoT (Industrial Internet of Things) and
Industry 4.0. IT/OT convergence describes the narrowing gap between technologies that have, until recently, existed in two silos, IT and OT:
- IT (information technology) describing, broadly, the core data and network infrastructure of the facility
- OT (operational technology) describing, broadly, the systems on the “front lines” of the facility — those that enable the control and execution of machine processes
In the next sections, we will examine IT and OT in more detail, before concluding with a look at IT/OT convergence benefits.
OT (operational technology) in manufacturing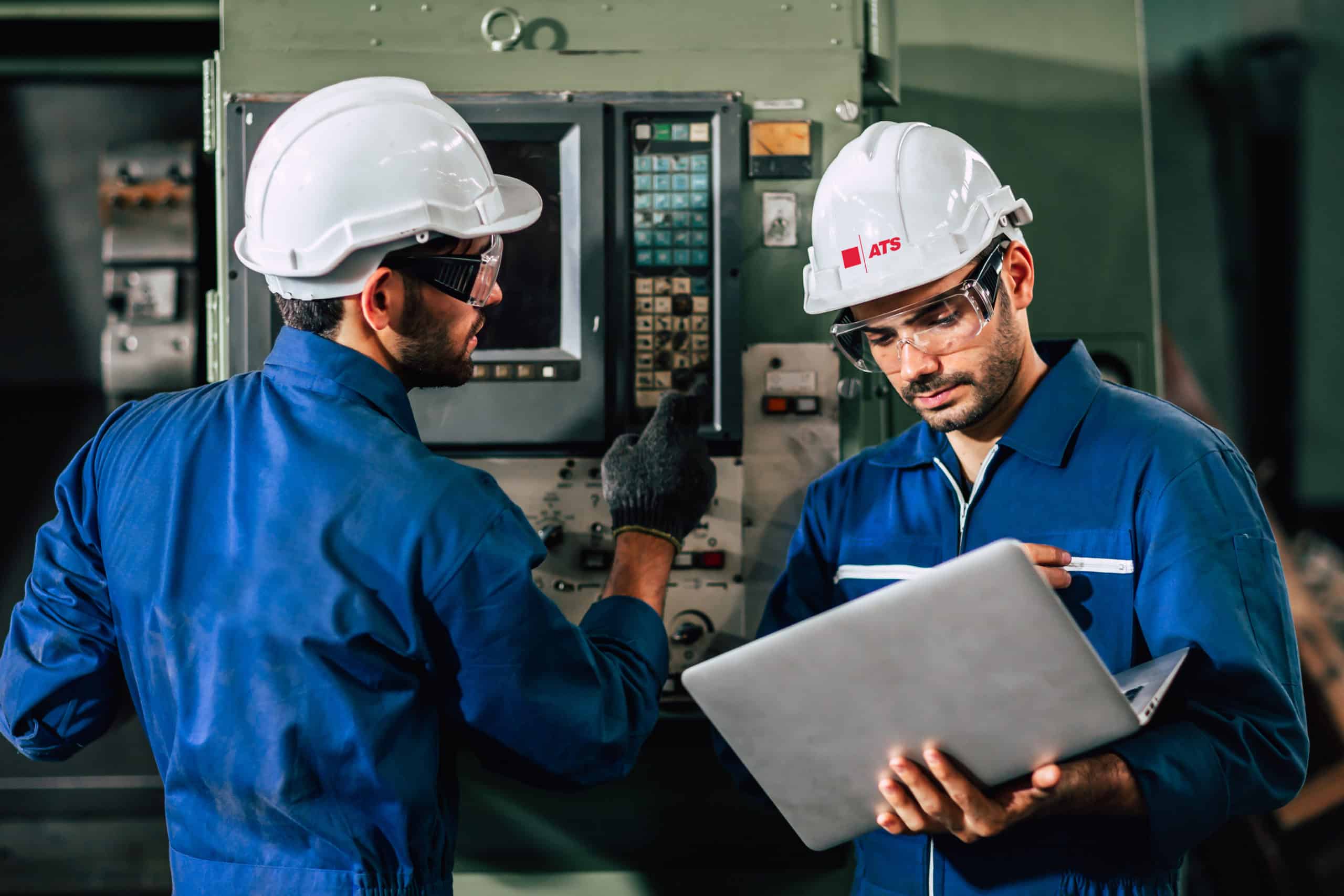
In the IT/OT discussion, OT can be viewed as the technology that makes processes happen (and enables them to be programmed, managed and controlled). Examples of OT include:
- SCADA for systems monitoring and control
- MES (manufacturing execution systems) for performance monitoring
- Direct interface and control technology such as PLCs and CNCs
Historically, OT functions and operations were not networked (beyond local networking necessary to their functions). For example, PLCs and CNCs are designed to control a particular piece of equipment, but have not previously “talked” to other equipment or to data centers. Systems such as SCADA and MES are designed for larger-scale control and monitoring of disparate machine systems, but still existed primarily as a contained network. The convergence of OT and IT has changed this scenario: creating more integrated connectivity and between the equipment and rethinking the profile of OT functions — previously seen as separate from network and data systems — as connected nodes with real-time data capture capabilities.
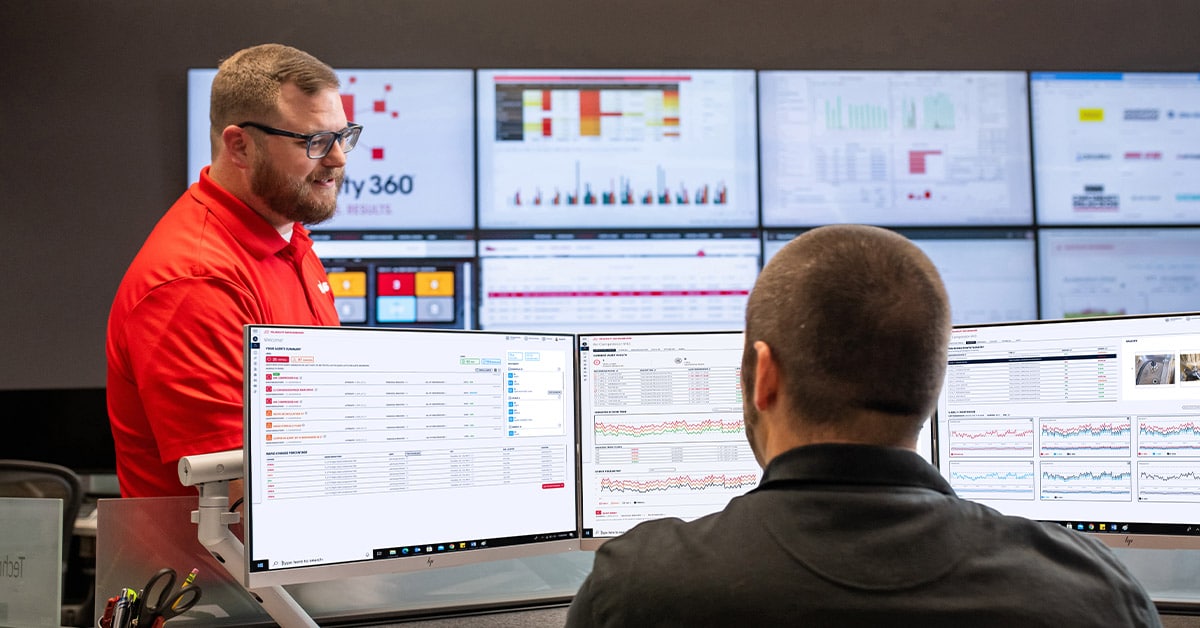
IT (information technology) in manufacturing
In contrast to OT — which historically exists on the shop floor at the machine level — IT is the information and data infrastructure of a facility or organization. IT includes:
- Servers and storage — beyond individual PC hard drives, organizational IT requires enterprise-scale network servers and data storage to support all required functions, especially given the convergence of OT and IT.
- Networking and connectivity, covering Internet access as well as internal connectivity for sensors and other equipment to communicate with servers and one another.
- Software such as ERP and inventory management.
- The laptops, desktops, tablets and other interfaces enable individual access to organizational systems and software.
Benefits of IT and OT convergence
With an understanding of IT and OT, and how they operate individually, we can now look at the benefits that the ongoing IT/OT convergence offers:
- Easier implementation and management: IT and OT have generally been separated practices, but that is no longer the case. With the advent of commonplace Wi-Fi — and the impending availability of 5G speed networking — equipment such as sensors and “smart” machines are essentially ready for communication out of the box. This is all without complex, bespoke networking setups and management systems.
- Integrated, simplified controls: Similar to the above point, the IT/OT convergence makes it easier to set up and training on one unified system that is designed to be intuitive to operate. The convergence means that connectivity, control and data access are no longer the exclusive realm of the one or two people who know how to program equipment and set up the network. All personnel should be able to manage and use control systems.
- Increased data access in real-time: By extending the data collection and storage function of IT to the OT components of a facility, managers and operators have greater transparency than ever into the performance of equipment and production systems — in real-time as well as historically. This data enables more informed, effective decision-making.
- More innovation and potential for improvement: By removing the complexities and silos of disparate IT and OT systems, workers throughout the facility are freed to use readily available data and intuitive control systems to explore further ways of innovating with technology. This paves the way for additional efficiency, productivity and quality improvements.
At ATS, we provide predictive maintenance services and IIoT solutions — including Reliability 360® and sensor technology — that take maximum advantage of the convergence of IT and OT. With our help, you are positioned to reap the benefits of this era of digital transformation. Contact ATS to learn more about our range of industrial maintenance solutions.