By any measure of today’s automotive landscape, demand for electric vehicles is on the rise — an increase that is poised to continue as the technology underlying EVs becomes more accessible, accepted and affordable. Consider:
- In the decade from 2011 to 2021, the number of electric vehicles on the road increased by nearly 100-fold, from 22,000 in 2011 to over 2,000,000 in 2021.
- In just one year – from 2020 to 2021 – new sales of hybrids and fully electric vehicles nearly doubled, increasing from 308,000 to 608,000.
Electric vehicle demand is driven by real metrics. Automotive buyers are generally led to consider purchasing an electric vehicle for the environmental benefits, as well as the promise of long-term savings by visiting the gas pump less (or, for fully electric vehicles, not at all). In addition to these savings, research now shows maintenance savings of up to $12,000 over the life of the vehicle. Moreover, EV purchasers can see a tax benefit of up to $7,500.
Additionally, two of the biggest perceived drawbacks to electric vehicles — range and availability of charging stations — have been addressed by advances in technology and infrastructure. Today’s EVs average a range of nearly 250 miles per charge, and there are now over 130,000 publicly available charging stations in the U.S.
The compounded effect of these changes — addressing consumer concerns while offering ever-more attractive benefits — makes the growth of electric vehicles in the U.S. unsurprising. Aside from the changes in buying behavior, the growth in demand for electric cars has also made a major impact on every aspect of the electric car manufacturing process, as well as the aftermarket experience for consumers in areas such as maintenance. We will explore those changes in this article.
The EV manufacturing impact on industry and consumers
A change in buying behavior, such as the one ongoing with electric vehicles, has far-ranging repercussions throughout the manufacturing process as well as in consumer activity once they own an EV. These impacts include:
New manufacturing processes and materials
While from the exterior many electric vehicles look nearly identical to their gas-powered predecessors, the manufacturing process has become vastly different. In electric vehicle manufacturing, the space normally reserved for the engine block and other components is now typically used for storage (as in the case of the “frunk,” or front trunk). Electric vehicle batteries are usually located on the underside of the chassis — a change that, on its own, necessitates a completely different production process. In addition to new manufacturing processes, the supply chain and materials required has changed as well. Electric vehicle batteries rely on rare earth materials, for example, which must be sourced differently than traditional vehicle production materials.
Different sets of technical skills
While production and assembly personnel and equipment fulfill generally similar roles in EV manufacturing and traditional vehicle manufacturing, there are a host of new skills and roles that must be filled for electric vehicles. For example, computer programmers play a larger role in designing and implementing the software that controls power usage and distribution. Engineers and technicians must be able to design, manufacture and handle EV batteries safely and effectively. Plus, electrical engineers and technicians have greater responsibilities in EV design and manufacture.
Supply chain impact
As mentioned above, electric vehicles draw on a completely different set of raw materials for battery and power distribution. These changes have produced vastly different supply chain management tactics, with the need to turn to different suppliers in different locals (subject to different external macro factors) in order to fulfill production needs. Electric vehicle manufacturers must quickly become experts in this new sourcing reality in order to remain efficient and cost-effective while meeting increased demand.
Higher levels of expertise from dealers and salespeople
When prospective buyers walk into a car dealership, they now expect salespeople to be able to answer their questions and fulfill their requests when inquiring about EVs. Gone are the days of attempting to steer potential buyers back to traditional vehicles — consumers are well aware of the potential benefits of EVs. If a particular dealership isn’t able to meet their needs, they will almost certainly go elsewhere, resulting in a lost sale. Dealerships are in the process of increasing their knowledge, expertise and service level for EV buyers, and must do so in order to remain competitive.
EV manufacturing: New processes and needs
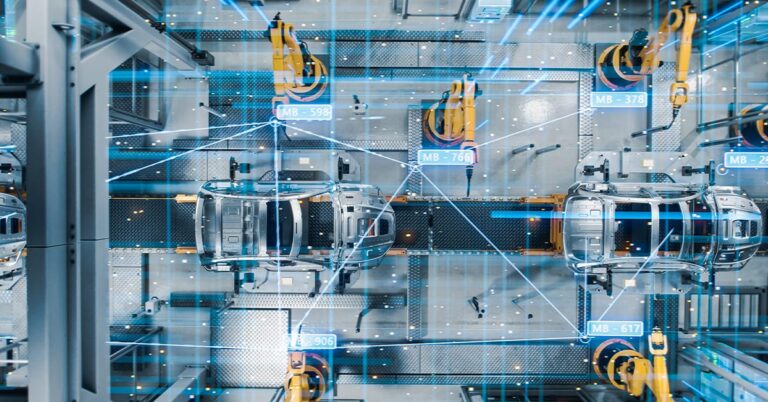
The electric car manufacturing process has created the need for a host of new technologies, practices and skill sets. These include:
- Shop Floor Practices: When working with lithium and other materials that comprise EV batteries, the need for increased shop floor automation is greater than ever. Automation technology such as cobots (collaborative robots) and connected machinery make production processes safer and more efficient. Robots can conduct tasks such as handling potentially dangerous raw materials, while, in the most advanced facilities, technicians can work directly alongside them to carry out critical, high-value inspection, assembly and other tasks.
- Technology: With demand on the rise for EVs, the ability to meet production commitments and deadlines is more important than ever. If suppliers are unable to fulfill orders effectively and on time, OEMs will turn elsewhere — and the potential benefits of retaining contracts are greater as demand continues to rise. Predictive maintenance in automotive industry applications is one of the most effective ways to maximize equipment uptime and meet deadlines — all while reducing maintenance costs and resource expenditures. As Industry 4.0 gains an increasing foothold across manufacturing, EV applications demand these massive advances in efficiency and productivity.
- Skilled Workforce: With new processes and technology comes the need for a newly skilled workforce. Manufacturers must be prepared to find the right personnel and provide the environment and training necessary to attract and retain them. The available technology today — based on automation, programming, efficiency and collaboration — can help attract the next generation of workers, but only when these processes are actually implemented. Manufacturers must take steps to ensure that prospective employees understand the digital transformation in the automotive industry and the current face of manufacturing jobs.
With this understanding of the massive changes that increased EV demand is driving, you are ready to prepare your facility to potentially meet these needs. The need for increased automation and efficiency is the same throughout the entire industrial sector, and the technology to facilitate success and remain competitive is available. For industrial maintenance and predictive technology support, contact us today.